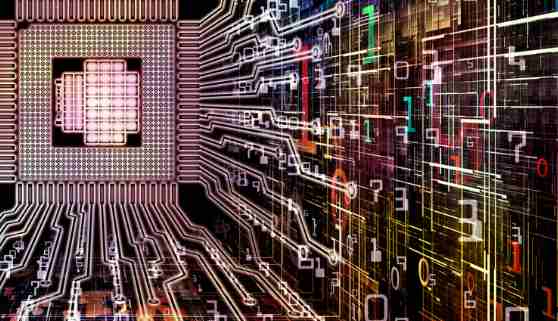
On PCB wire width and current of the empirical formula, the relationship table and software on the Internet are a lot, this paper put the online collated, aimed at the majority of engineers in the design of PCB board to provide convenience.
The following summarizes the relationship between eight kinds of current and line width formula, table and calculation formula, although they are different (roughly similar), but you can in the actual PCB board design, comprehensive consideration of the size of the PCB board, through the current, choose a suitable line width.
1. PCB current and line width
The calculation of PCB current-carrying capacity has been lacking of authoritative technical methods and formulas. Experienced CAD engineers can make more accurate judgment by relying on their personal experience. But for CAD novices, it is not a problem.
The current carrying capacity of PCB depends on the following factors: wire width, wire thickness (copper foil thickness), allowable temperature rise. As we all know, the wider the PCB line, the greater the current carrying capacity. Given the same conditions, 10MIL can withstand 1A, then 50MIL can withstand what current, 5A? The answer, of course, is no. Please take a look at the following data provided by international authorities:
Data provided:
The unit of line width is Inch (1inch=2.54cm=25.4mm).
Data source: MIL-STD-275 Printed Wiring for Electronic Equipment
Second, PCB design copper platinum thickness, line width and current relationship
Before understanding the PCB design copper platinum thickness, line width and current relationship, let's understand the conversion between the PCB copper thickness in ounces, inches and millimeters: "In many data tables, PCB copper thickness is often used in ounces, and its conversion relationship with inches and millimeters is as follows:
1 oz = 0.0014 inches = 0.0356 mm (mm)
2 oz = 0.0028 in = 0.0712 mm (mm)
The ounce is a unit of weight, which can be converted to millimeters because the copper thickness of the pcb is ounces per square inch
PCB design copper platinum thickness, line width and current relationship table
The empirical formula can also be used to calculate :0.15× linewidth (W)=A
The above data are the line current bearing values at the temperature of 25 ° C.
Conductor impedance :0.0005×L/W(line length/line width)
In addition, the relationship between the current carrying value of the wire and the number of holes in the wire pad
Wire current bearing value and the number of wire wire hole welding pad exists a direct relationship (at present did not find the welding pad and hole aperture per square millimeter on the line bearing value of the calculation formula, have a heart of friends can find their own, personal is not too clear, not to explain) here only to do some simple influence on the line current bearing value of the main factors.
1. The bearing value listed in the table data is the maximum current bearing value that can be borne at room temperature of 25 degrees. Therefore, various factors such as environment, manufacturing process, plate process, plate quality and so on should be considered in the actual design. So the table is provided only as a reference value.
2, in the actual design, each wire will also be affected by the pad and the hole, such as the pad to teach more line, after the tin, the pad that its current bearing value will be greatly increased, may be many people have seen some large current plate between the pad and the pad a certain line burned, the reason is very simple, The solder pad enhances the current carrying value of the wire because of the element foot and solder after the tin, and the maximum current carrying value of the pad between the pad and the pad is the maximum current carrying value allowed by the width of the wire. Therefore, when the circuit fluctuates instantaneously, it is easy to burn the section of line between the welding pad and the welding pad. The solution: If the board cannot allow you to increase the width of the wire, add a Solder layer (Generally, you can add 0.6 Solder layer on the 1mm wire. Of course, you can also add a 1mm Solder wire). This 1mm wire can be regarded as a 1.5mm~2mm wire (depending on the uniformity and amount of tin when the wire passes through the tin), as shown in the figure below:
Like this kind of treatment method for those engaged in small household appliances PCB Layout friends are not unfamiliar, so if the amount of tin is uniform enough and the amount of tin is enough, this 1mm wire can be seen as more than a 2mm wire. This is important in a single - sided high - current plate.
3. The treatment method around the pad shown in the figure is also to increase the uniformity of current carrying capacity between the wire and the pad. This treatment is very important especially in plates with large current and thick pins (pins greater than 1.2, pads above 3). Because if the pad is above 3mm pin and above 1.2, it is in the tin, the current of the spot pad will increase many dozens of times, if the large current instantaneous fluctuation, the current carrying capacity of the whole line will be very uneven (especially when the pad is much), it is still very easy to cause the possibility of burning between the pad and the pad. In the figure, such treatment can effectively disperse the uniformity of the current bearing value between a single pad and the surrounding line.
Finally, it is explained again that the current bearing value data table is only an absolute reference value. When no large current design is done, 10% more data provided in the table can absolutely meet the design requirements. In the general single-panel design, the copper thickness of 35um can be basically designed in a ratio of 1 to 1, that is, the current of 1A can be designed with 1mm wire, which can also meet the requirements (calculated at 105 degrees temperature).