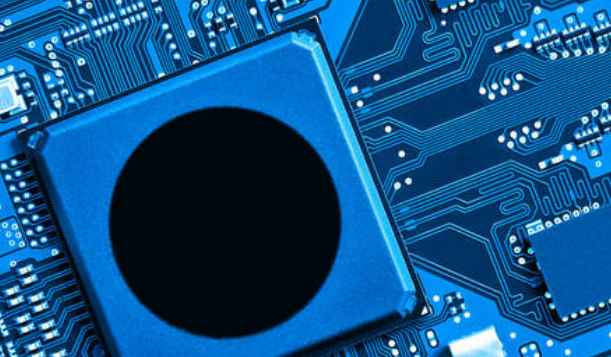
The concept of differential impedance is itself a mathematical structure that does not fully capture the behavior of every signal in the differential routing. Differential impedance is a shortcut to another important value, odd-mode impedance, and vice versa. So what do we need to design for and how do we make sure that the signal is decoded correctly at the receiver?
Differential impedance definition
Differential impedance is related to the fundamental characteristics of the differential signal. All differential signals are interpreted as differential signals by the receiver assembly (hence the name "differential"). One way to think about a differential signal is: it is a propagating electromagnetic interference involving two different signals, ideally sent together along a pair of routes. When we say "electromagnetic interference," we mean the distribution of electric and magnetic fields around two tracks. That, after all, is the whole point of conductors in a PCB: to guide and transmit electromagnetic fields around the layout.
So it will be interesting to see how this electromagnetic interference to the signal propagates along the two tracks. To do this, we need:
Transmission line impedance experienced by electromagnetic sites
The propagation constant of this interference
If you know one of these values, you can calculate the other value. The point of designing a specific differential impedance is to ensure that the electromagnetic field we inject into the channel is interpreted as the same (or nearly the same) electromagnetic field received at the load end of the channel.
What should be interesting here is how each trace-generated field is used. I mean, we care about the difference between the two signals (their fields), or their sum, depending on the function of the receiver. So as far as the Telegrapher's equation is concerned, we want to look at the propagation of the differences between these two signals, a mathematically demanding subject that requires defining the mutual capacitance and inductance between traces.
Differential impedance formula
Calculating differential impedance is an exercise in calculating another important quantity, the odd-mode impedance. When two wires are routed as differential pairs and driven by differential signals, the impedance of a single wire will be the odd-mode impedance value.
Unfortunately, there are not many good analytical models for differential impedance, or more specifically, odd-mode impedance. If you look at Brian C. Wadell's Transmission Line Design manual, you will find that 70 formulas are used to determine the impedance of a pair of microstrip lines (see Section 4.5). This is not a misprint, it does require a total of 70 formulas for calculating the odd-mode or even-mode impedance of a pair of microstrip lines. If you want to use coplanar permutations or asymmetrical trajectories, you will need fewer formulas, but you will need to calculate elliptic integrals, something I have never done, and would employ an application like MATLAB or Mathematica.
You can obtain mutual inductance or mutual capacitance directly from Maxwell's equations, although these results are the subject of many research papers, and the results are not always easy to use. They often involve a set of ugly formulas with multiple parameters. This is why you see so many differential impedance calculators online that use only the formulas IPC-2141A, which are approximations of less used formulas.
Calculate the width and spacing
If you calculate the width needed for the run-out line to reach the characteristic impedance goal (that is, 50 ohm) and then plug that width into a differential impedance calculator, you will find that you will not always get useful spacing results; The spacing may be too small (< 4 mils) and probably beyond the capacity of very thin dielectrics. Conversely, for thicker dielectrics, the spacing can end up being very large. In fact, on a 2-layer standard-thickness PCB, the required wire width for the microstrip to achieve a 50 ohm impedance at the standard core is about 105 ohm. In order for a single trace to have an odd-mode impedance equal to the characteristic impedance, your field solver will tell you that you need to separate the trace by a large amount. If you use a field solver, you'll find that it may stop converging when the spacing is about 10 inches! Apparently, that doesn't help either.
In general, there are many combinations of line spacing and width that will allow you to achieve differential impedance specifications. What you are really designing is odd-mode impedance, not differential impedance, which is simply the specification that defines odd-mode impedance. So, we can't help but ask, without a formula, how can we determine the odd-mode impedance and the objective combination of line width and spacing?
Compare the width and spacing of differential microstrip lines
To see which combination of wireline width and spacing will provide the required differential impedance, let's look at some simulation results. In the example below, I'll run the following procedure
Calculate the line spacing required for a specific line width in the differential microstrip line pair with the goal of achieving a target differential impedance of 100 ohm.