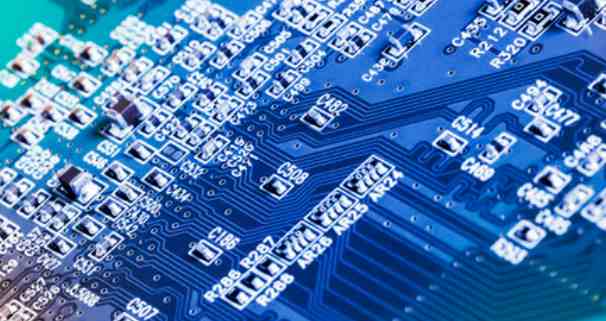
Choosing a long-term PCB manufacturer or assembler (referred to as PCB Factory in the following paragraph) can be a tough job for PCBA Oems because there are so many PCB service providers worldwide. This article provides you with some guidance to help you pick the most suitable PCB package from the long waiting list. In addition, a list of free template surveys will be available so that you can directly use them as criteria when evaluating pcb manufacturing companies for long-term collaborations.
Although the manufacturing and assembly of PCBS consist of many steps that should be carefully examined, the process focuses on products, functions and services. Therefore, this article follows the same route.
product
The quality of PCB will directly affect the application and performance of the final product. Therefore, the first principle of evaluating a PCB plant is to check the condition of its products, which can be extended to the three dimensions of quality, industry and cost.
1) Quality
Everyone wants high quality from: Is SPC used in the PCB manufacturing process (e.g., Cpk control of components or manufacturing management charts)? Whether continuous quality management improvements such as QCC or TQM have been implemented; Whether ECO management (engineering change order) has been applied; Whether the component exemption control principle is published in its terms and conditions; Has passed strict quality control assessment, including material inspection record and management, SMT pass rate, AQL level, document management, BOM preservation, ESD implementation, equipment calibration;
2) Industrial sector
are used in many different industries, and specific industries have strict and special requirements for their manufacturing standards. It is almost impossible for a PCB plant to cover all industries evenly. In general, they tend to be better at serving some industries and less skilled at others. For example, PCB plants that are proficient in mobile phone PCBS must have enough experience to limit the space of the final product, while PCB plants that are mainly used in the aerospace industry must be better in terms of high density.
3) Cost
While there are a few tricks that can reduce the cost of assembling PCb as for PCBS, sometimes price is the main factor in our final decision. When selecting PCB rooms, the cost must be analyzed from two aspects: the overall offer - don't just indulge in the attractive numbers. Reliable PCB factories are responsible for every word they claim to protect. You should make sure that their sales people give you full price and that there isn't any hidden or extra money in the later stages of your order; Continuous cost reduction - This means certain discounts on reorders. While PCB Home will never offer you consistently low prices, you can expect constant discounts on your orders, such as waiving mold costs, etc. This strategy is a solid foundation for long-term cooperation.
ability
Previously said, product quality is the soul of PCB factory, PCB factory to see the ability. PCB manufacturing and assembly capabilities can be demonstrated in the following aspects:
1) Certificate
The certificate represents the true manufacturing capability of the factory. When you work with PCB factories that are certified to ISO9001:2008, UL, RoHS and other standards, you can rest assured that they will strictly comply with the provisions of these certificates to obtain high quality products.
2) Technology
The related aspects of PCB plant technology studied can be summarized as follows: whether the technology adopted meets your requirements and whether the processing capacity meets your requirements; Whether the factory has advanced processing or automation equipment. Are they creative with technology? Whether it has the ability to lead the market in new processing methods; Process capability evaluation; BGA IC repair ability; 0201 or 01005 welding ability and repair ability; RoHS execution capability SOP integrity; How to avoid material selection errors and negative polarity; Ability to review circuits and provide DFM services; Humidity sensitivity (MSL) element control function; Welding paste temperature recovery, sealing and shelf life management functions; Panel processing function.