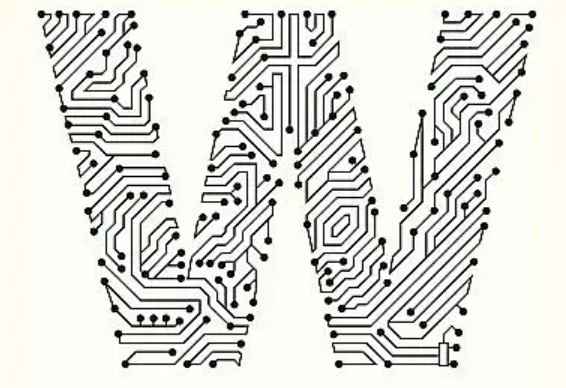
In consideration of signal quality control, the general principles of PCB layering design are as follows:
1. The second layer adjacent to the component surface is the ground plane, which provides the device shielding layer and the top layer wiring to provide the reference plane.
2. All signal layers are adjacent to the ground plane as far as possible to ensure a complete return channel.
3. Avoid two signal layers directly adjacent to each other to reduce crosstalk.
4. The main power supply is adjacent to it as far as possible to form a plane capacitor and reduce the plane impedance of the power supply.
5, taking into account the laminating structure symmetry, conducive to plate production of warping control.
The above is the general principle of cascade design. In the actual development of cascade design, circuit board designers can increase the spacing of adjacent wiring layers, reduce the spacing between the corresponding wiring layer and the reference plane, and then control the cross-talk rate of inter-layer wiring, under the premise of using two signal layers directly adjacent.
For consumer products that pay more attention to cost, the adjacent power supply to the ground plane can be weakened to reduce the impedance of the plane, so as to reduce the wiring layer as much as possible and reduce the PCB cost. Of course, this comes at the cost of signal quality design risks.
For the overlapping design of Backplane or midplane, it is difficult for common backplanes to run adjacent cables perpendicular to each other, which inevitably leads to parallel long-distance wiring. For high-speed backplanes, the general cascading principles are as follows:
1. The Top and Bottom surfaces are a complete ground plane, constituting a shielding cavity.
2, no adjacent layer parallel wiring, to reduce crosstalk, or adjacent wiring layer spacing is far greater than the reference plane spacing.
3. All signal layers are adjacent to the ground plane as far as possible to ensure a complete return channel.
What are the requirements of SMT patch components for SMT processing?
SMT is a technology and technology popular in the electronic assembly industry at present, which is also known as surface mounting technology. Through SMT technology, it can meet the requirements of miniaturization of electronic products. In order to achieve the advantages of high precision, light weight and small area of SMT technology, in addition to high requirements for mounting technology, it also has higher requirements for SMT components. So what are the requirements for patch components?
SMT components such as rectangular patch element, cylindrical patch element, composite patch element and special-shaped patch element are the main surface mount components, while SMT semiconductor devices such as diodes, transistors and integrated circuits are the main surface mount components. So what are the requirements for these components?
1. Shape: component shape standard, then and positioning, suitable for automatic assembly.
Ii. Size: component size standards. The dimensional accuracy of patch components should match the dimensional accuracy of surface assembly technology and surface assembly structure, so as to be interchangeable.
3. Electrical performance: The electrical performance of the components shall meet the requirements of standardization, with good repeatability and stability. Its mechanical strength should meet the technical requirements of the assembly technology and the performance requirements of the assembly structure.
Four, heat resistance: the heat resistance of the materials in the components should be able to withstand the temperature impact of the welding process, not easy to burn out. The surface chemical properties can withstand washing with organic solution.
V. Material properties: The position and material properties of the external outlet of the components should be conducive to automatic welding process, and the external structure is suitable for braiding and packaging, and the model or parameter is easy to identify.
The basic points of PCB layout for switching power supply are summarized in 8 points
PCB novice must have encountered wiring, layout difficult problems, and switching power supply generated electromagnetic nuisance, often affect the normal work of electronic products, the correct PCB layout of switching power supply becomes extremely important. A power supply that is perfectly designed on paper may not work properly on the first debugging because there are some problems with the PCB wiring of the power supply. So what's the ideal solution? Dongguan Hongju Electronics summarized eight key points of PCB fast wiring for switching power supply.
In today's society, electronic products are being updated very quickly. Product design engineers prefer to select AC/DC adapters that are readily available in the market, and install multiple sets of DC power directly on the circuit board of the system. Because the electromagnetic interference produced by switching power supply will affect the normal work of its electronic products, the correct PCB layout of power supply becomes very important. This paper summarizes the basic points of PCB layout of eight-point switching power supply according to experience.
1, the capacitance of the bypass porcelain capacitor can not be too large, and its parasitic series induction is as small as possible, multiple capacitors in parallel can improve the impedance characteristics of the capacitor;
2. The parasitic parallel capacitance of the inductor should be as small as possible, and the distance between the inductor pin pad should be as far as possible;
3. Avoid placing any power or signal wiring on the formation;
4. The area of high-frequency loop should be reduced as much as possible;
5, hole placement should not destroy the path of high frequency current on the formation;
6. On the system board: different circuits need different grounding strata, and the grounding strata of different circuits are connected to the grounding strata of the power supply through a single point;
7, control chip to the upper and lower end of the field effect tube drive circuit loop should be as short as possible;
8. The power circuit and control signal circuit components need to be connected to different ground layers, which are generally connected through a single point.