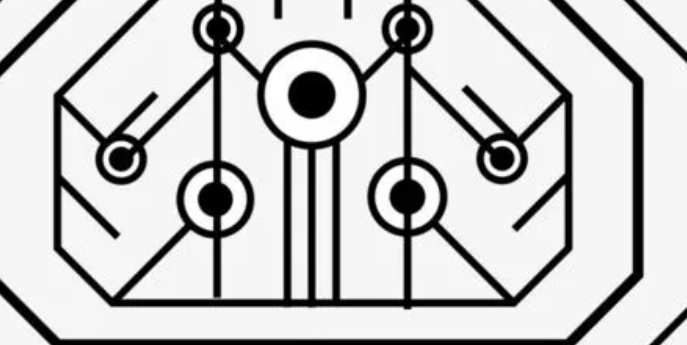
1, wire width should be able to meet the requirements of electrical performance and convenient production is appropriate, its minimum value to withstand the size of the current, but the minimum should not be less than 0.2mm, in high density, high precision printed lines, wire width and spacing generally desirable 0.3mm.
2, wire width in the case of large current should also consider its temperature rise, single panel experiment shows that when copper foil thickness is 50μm, wire width 1-1.5mm, through the current 2A, temperature rise is very small, therefore, generally choose 1-1.5mm width wire may meet the PCB design requirements without causing temperature rise.
3, printed wire public ground wire should be as thick as possible, if possible, the use of lines greater than 2-3mm, this is particularly important in the circuit with a microprocessor, because when the line is too thin, due to the change of the current through the ground potential changes, the level of the microprocessor timing signal is unstable, will make the noise tolerance deterioration.
4. The principles of 10-10 and 12-12 can be applied in wiring between DIP-packaged IC feet, that is, when two wires pass between two feet, the diameter of the pad can be set as 50mil, and the line width and line distance are both 10mil; when only one wire passes between two feet, the diameter of the pad can be set as 64mil, and the line width and line distance are both 12mil.
Bronze and teardrops
Apply tear drops to all holes and pads. Always add tear drops to patches and single panels. The grounding network of each wiring layer is coated with copper to enhance the anti-interference ability of the board.
14 DRC inspection
In order to ensure that the circuit board drawing complies with the design rules and that all the networks are properly connected, we must conduct DRC inspection after wiring.
15 Adjust the information on other layers
After all adjustment and DRC is passed, drag and drop all the characters of the screen printing layer to the appropriate position, pay attention to try not to put under the element or on the hole, welding pad, for too large characters can be appropriately reduced. Finally, put the plate name, design version number, company name, first processing date of the document, plate file name, document processing number and other information, and can be provided by a third party program to add comments in Chinese.
16. Save and export printed board files
Protel DXP drawing PCB circuit board design is completed, we also need to complete the printing board file sorting and archiving, printing out drawings and other work. You can export component specifications, generate spreadsheet documents as component lists, and so on. Finally, we have to explain the special requirements on the circuit board, and then submit to the board processing plant for circuit board processing.
How to optimize the design of heat sink in PCB design?
In PCB design, the improper design of the heat sink of the heat sink hole causes the fracture of many power supply boards. The following Shenzhen Honglijie for you to analyze the specific reasons for the power plate fracture due to the improper design of the heat sink hole, and think about the optimal design scheme.
Analysis: Because of the linear power source heat serious, the PCB board is very long, at the same time, the bottom of the heat sink PCB hole is too large, and the heat sink against the upper cover, when the external force on the upper cover, the pressure will directly act on the PCB board, resulting in PCB fracture, the machine does not work.
Countermeasure: Shorten the heat sink by 5MM and reasonably open the heat sink hole.
Thinking: After the change, the heat of the pressure stabilizer block is still serious, and then many heat dissipation holes are opened at the bottom of the machine. But more serious problems have arisen.
Because of the large sand in the northwest, dust from the heat sink into the bald pollution, resulting in a lot of machines do not read disk or error correction. This is also the later machine rarely open the heat dissipation hole and the main reason for using switching power supply to reduce the heat.
The delay time of the signal on the printed board is related to the characteristic impedance of the lead, that is, the dielectric constant of the printed circuit board material. Roughly speaking, the speed at which a signal travels through a printed board lead is between 1/3 and 1/2 the speed of light. The Tr(standard delay time) of logic telephone components commonly used in systems composed of microcontrollers ranges from 3 to 18ns.
On the printed circuit board, the signal passes through a 7W resistor and a 25cm long lead, with an on-line delay of roughly 4-20ns. That is to say, the shorter the lead of the signal on the printed line, the better, the longest should not exceed 25cm. And the number of holes should be as small as possible, preferably no more than 2.
When the rise time of the signal is faster than the signal delay time, fast electronics processing is required. At this point, the impedance matching of the transmission line should be considered. For the signal transmission between the integrated blocks on a printed circuit board, the situation of Td Trd should be avoided. The larger the printed circuit board, the less fast the system speed.