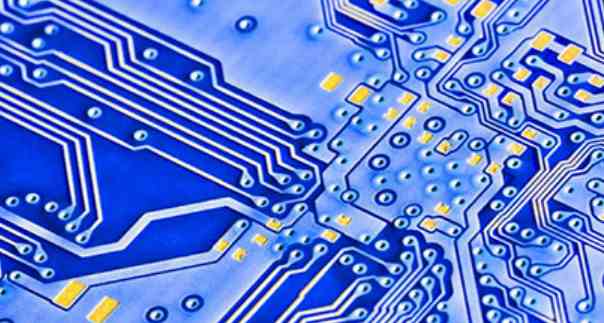
Coordinating the validation of machine Settings is an ideal role for the process monitor, who leads the machine operator through the production line validation process with the help of a checklist. In addition to verifying the feeder setup, the process monitor should carefully examine the first two plates using the available tools. After reflow soldering, the process monitor should perform a quick but detailed inspection of critical components (close-spaced components, BGA, polar capacitance, etc.). Meanwhile, the assembly line continues to assemble the plates. To reduce downtime, the line should be filled prior to backflow while the process monitor checks the initial two boards after backflow. This can be a bit dangerous, but you can gain the confidence to do so by verifying the machine Settings.
X-ray examination. Based on experience, X - rays are not necessarily mandatory for BGA assembly. But it's certainly a good tool to have on hand, if you can afford it. It should be recommended for CSP assemblies. X - rays are very good at detecting welding short circuits, but not very good at finding welding open circuits. Low-cost X-ray machines can only look down, and inspection for welding short circuitsis sufficient. An X-ray machine that tilts the object under examination is better for opening the way.
Automatic optical inspection (AOI). Ten years ago, optical inspection was used as a tool that could solve quality problems for everyone. The technology was discontinued because it could not keep up with assembly technology. In the past five years, it has re-emerged as a desirable technology. A good process monitoring strategy should include overlapping tools such as online testing (ICT), optical inspection, functional testing, and appearance inspection. These processes overlap and complement each other, and neither alone provides adequate coverage.
Two-dimensional (2-D)AOI machines can check for missing components, alignment errors, incorrect part numbering, and polarity reversals. In addition, three-dimensional (3-D) machines can evaluate the quality of welding points. Some vendors are offering desktop, 2-D AOI machines for less than $50,000. These machines are ideal for initial product inspection and small batch sample planning. In the higher performance category, 2-D stand-alone or online machines cost between $75,000 and $125,000, while 3-D machines cost between $150,000 and $250,000. AOI technology has considerable promise, but processing speed and programming time remain a limiting factor.
Data collection is one thing, but using that data to improve performance and reduce defects is the ultimate goal. Unfortunately, many companies collect a lot of data without using it effectively. Reviewing and analyzing data can be laborious, and it is often seen that this work is performed only by engineering staff, not production activities. Without accurate feedback, production goes on blindly. Weekly quality meetings can be an effective way for engineering and production to communicate key information and drive necessary improvements. These meetings require a leader and must be well organized, especially if they are short (30 minutes or less). The data presented at these meetings must be user-friendly and meaningful (e.g., Pareto charts). When a problem is identified, an investigative researcher must be assigned immediately. In order to ensure a successful conclusion, the meeting leader must take accurate notes. Closure means root cause and corrective action.
What should we pay attention to in PCB process design
PCB circuit board has a variety of technological requirements, its production process is complicated and complex, if there is no reasonable design, it is easy to appear all kinds of bad problems, resulting in poor product quality. So what should we pay attention to in the process design of PCB circuit board? The following Jingbang circuit board manufacturer Xiaobian for you to sort out and introduce:
1. Shape
PCB board appearance should be smooth and flat, not warped or uneven. The appearance of PCB circuit board is usually rectangular, and the right-angle PCB board is easy to produce cards when transferring, so in the design of PCB board, to do arc Angle processing of the board frame.
2. Size range
The size of PCB circuit board should not be too large as far as possible. The large board is easy to bend and the installation is not accurate. From the perspective of production, the ideal size range is "wide (200mm ~ 250mm) x long (250mm~350mm)". For too small PCB circuit boards, the way can be used to convert to meet the production requirements of the ideal size for welding.
3. Positioning hole
Design at least three positioning holes at the corner of each PCB board. The size of the positioning holes is Φ3+0.1mm. Do not electroplate the inner wall of the holes to avoid inaccurate dimensions. Depending on these two positioning holes and a number of thimbles with magnets at the bottom of the printed board are evenly arranged, which can fully ensure the firm and smooth positioning of the printed board.
4. Safe distance of components
Considering that there is a certain error when the machine is mounted, and considering the convenience of maintenance and visual inspection, the two adjacent components should not be too close to each other, and a certain safe distance should be left, which is best reflected directly on the packaging.
5. Component layout rules
If conditions permit, the layout of PCB circuit board components should be arranged in the same direction as far as possible, and the modules with the same function should be arranged together. The direction of the positive and negative elements is unified, so that the components can be mounted, welded and tested.
6, components of the welding pad width
The lead width on both sides of the component pad should be the same. If there is a gap between the size of the time pad and the electrode, it is necessary to pay attention to whether there will be short circuit phenomenon. Finally, it is necessary to pay attention to keeping the unused pin pad and correctly grounding or connecting the power supply.