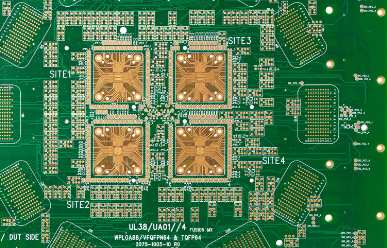
(1) According to the size of the PCB current, the width of the power cord and ground wire should be thickened as far as possible to reduce the loop resistance. At the same time, the direction of the ground wire of the power cord should be consistent with the direction of data transmission, which helps to enhance the anti-noise ability.
(2) As far as possible to choose the patch component, shorten the length of the pin, reduce the decoupling capacitor power supply circuit area, reduce the influence of the component distribution inductance.
(3) Add a power filter at the front end of the power transformer to suppress common-mode noise and differential mode noise and isolate the interference of external and internal pulse noise.
(4) the power supply circuit of the printed circuit board should be added with a filter capacitor and decoupling capacitor. A large-capacity electrolytic capacitor is added to the power inlet end of the board for low-frequency filtering, and then a capacitor with a smaller capacity is connected in parallel for high-frequency filtering.
(5) Do not overlap the analog power supply and digital power supply, so as not to produce coupling capacitance, causing mutual interference.
PCB board ground wire design
(1) In order to reduce the ground loop interference, we must find ways to eliminate the formation of the loop current. Specifically, we can use isolation transformer, optocoupler isolation to cut off the formation of the ground loop current or use balance circuit to eliminate the loop current.
(2) In order to eliminate the coupling of the common impedance, the impedance of the part of the public ground wire should be reduced, and the thickened wire or the ground wire is covered with copper; On the other hand, mutual interference can be avoided through appropriate grounding, such as parallel single point grounding, series mixed single point grounding, completely eliminate public impedance.
(3) In order to eliminate the interference of digital devices on simulator parts, digital ground and analog ground should be separated, and analog ground and digital ground should be set separately. High frequency circuit adopts series grounding mode, ground wire should be short and thick, high frequency components around as far as possible with a large area of grid copper to be shielded.
Layout of crystal oscillator circuit of PCB board
The high frequency of crystal oscillator circuit makes it an important interference source in the system. Regarding the layout of crystal oscillator circuit, there are the following points for attention:
(1) The crystal oscillator circuit should be as close to the integrated block as possible, and all the printed lines connected to the crystal oscillator input/output should be as short as possible to reduce noise interference and the influence of distributed capacitance on the crystal oscillator.
(2) The crystal oscillator capacitor ground wire should be connected to the device with printed wire as wide and short as possible; The digital ground pin closest to the crystal oscillator should minimize overhole.
(3) crystal oscillator shell grounding.
Electrostatic protection design of PCB board
Electrostatic discharge is characterized by high potential, low charge, high current and short time. The electrostatic protection of PCB design can be considered from the following aspects:
(1) Try to choose components with high antistatic grade, and sensitive components with poor antistatic ability should be far away from electrostatic discharge power. The test shows that the breakdown distance of electrostatic voltage is about 1mm per kilovolt. Therefore, if the component is kept 16mm away from the electrostatic discharge power supply, it can resist about 16KV electrostatic voltage.
(2) Ensure that signal reflux has the shortest path, selectively add filter capacitor and decoupling capacitor, improve the electrostatic discharge immunity of signal line;
(3) Use protection devices such as voltage transient suppression diode to protect the circuit design;
(4) Relevant personnel must wear electrostatic bracelets when touching PCB to avoid the accumulation of electrostatic damage caused by the movement of human charge.
4 Conclusion
PCB electromagnetic compatibility design is to reduce external electromagnetic radiation and improve the ability to resist electromagnetic interference, reasonable layout and wiring
It's the key to design. The various methods and techniques described in this article are helpful to improve the EMC characteristics of high speed PCBS. Of course, these are only part of the EMC design, and usually consider the interference caused by reflection noise, radiation emission noise, and other technical issues. In the actual design, according to the design objective requirements and design conditions, the use of reasonable anti-electromagnetic interference measures, make comprehensive consideration, design has good EMC performance of PCB circuit board.
The DECP project was organized by the National Electronics Manufacturing Initiative (NEMI) and involved IPC and Valor; Its purpose is to facilitate the formation of a unified data exchange standard for PCB design/manufacture. NEMI persuaded IPC and Valor to work together, using Valor's ODB + + (X) data format as a prototype to incorporate strong parts of IPC GenCAM, resulting in a yet-to-be-announced integration standard IPC-2581, which IPC would eventually maintain and manage.
At present, PCB industry has dozens of EDA and CAM software vendors as well as the chain of organizations are involved in DECP. If it can be successfully implemented in each link of the industrial chain, it will bring huge benefits in cost and development cycle. There is obviously a long way to go to achieve this goal. Participants and the industry are cautiously optimistic.
Concluding remarks
As PCB enters the stage of high frequency and high density, designers must consider more compromise between testing and manufacturing requirements, and absorb the participation and interaction of manufacturing and assembly parties. The result of this interaction will be frequent changes to the original design, thus avoiding or reducing manufacturing errors. Designers, test engineers, and manufacturing engineers all need complete data to be able to communicate in both directions. Therefore, we must give up the traditional exchange structure centered on EDA tool output and adopt the new model centered on data. Data-centered PCB data exchange mode calls for the birth of data format standards that can adapt to various EDA software and manufacturing equipment.
The exchange of PCB design/manufacturing data is the key to the information integration of electronic design and manufacturing. Therefore, it is urgent to establish a new format standard of PCB data exchange. Most of the research is currently in the testing phase, as the DECP data exchange project continues. It can be predicted that a set of unified, perfect data exchange format standard is coming out. Due to the low level of domestic participation in this research activity, it is of positive practical significance to promote and intervene in the corresponding research content.