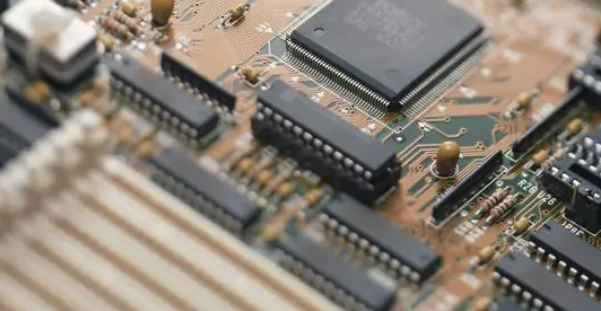
The circuit containing the magnetic sensor is more sensitive to the surrounding magnetic field, and the bend of the wiring when the high-frequency circuit works is easy to radiate electromagnetic waves, if the magnetic sensor is placed in the PCB, it should ensure that the wiring corner has a certain distance from it.
Wiring on the same level is not allowed to have crossover. For possible crossed lines, the solution can be "drill" and "wind", that is, let a lead from other resistors, capacitors, transistors and other devices at the foot of the gap "drill" in the past, or from one end of a lead that may cross "wind" in the past. In special cases, if the circuit is very complex, in order to simplify the design, it is also allowed to use wire jumper to solve the crossover problem.
When the high frequency circuit operates at a higher frequency, it is also necessary to consider the impedance matching of the wiring and the antenna effect.
2.3 Cabling Requirements for power cables and ground cables
According to the size of different working currents, try to increase the width of the power cord. High-frequency PCB should try to use a large area ground wire and layout on the edge of the PCB, which can reduce the interference of external signals on the circuit; At the same time, the grounding wire of the PCB can be in good contact with the housing, so that the grounding voltage of the PCB is closer to the ground voltage. The grounding method should be selected according to the specific situation, and the low-frequency circuit is different, the grounding wire of the high-frequency circuit should be grounded nearby or multi-point grounding, and the grounding wire is short and thick to minimize the ground impedance, and the allowable current requirements can reach 3 times the working current standard. The ground cable of the speaker should be connected to the ground point of the PCB power amplifier output stage. Do not ground arbitrarily.
In the wiring process, some reasonable wiring should also be locked in time to avoid repeated wiring. Execute the EditselectNet command to select Locked in the pre-wired property to lock it away from moving.
3. Design of welding pad and copper coating
3.1 Pad and aperture
In order to ensure that the minimum wiring spacing does not violate the electrical spacing of the design, the design of the pad should be large to ensure sufficient ring width. Generally, the inner hole of the pad should be slightly larger than the lead diameter of the component, and the design is too large, which is easy to form virtual welding in welding. The outer diameter of the pad D is generally not less than (d+1.2)mm, where d is the inner aperture of the pad, and for some PCB with relatively large density, the minimum value of the pad can be (d+1.0) mm. The shape of the pad is usually set to round, but it is best to use the runway shape of the pad for DIP-packaged integrated circuits, so that the area of the pad can be increased in a limited space, which is conducive to the welding of integrated circuits. The connection between the wiring and the pad should be smooth, that is, when the width of the wiring into the round pad is smaller than the diameter of the round pad, the teardrop design should be used.
It should be noted that the size of the aperture d in the pad is different, and should be considered according to the size of the actual component lead diameter, such as component holes, mounting holes and slot holes. The hole distance of the pad should also be considered according to the actual installation method of the components, such as resistors, diodes, tubular capacitors and other components have "vertical" and "horizontal" installation methods, and the hole distance of these two methods is different. In addition, the design of pad hole spacing should also consider the minimum gap requirements between components, especially the gap between special components needs to be guaranteed by the hole spacing between the pads.
In high-frequency PCBS, it is also necessary to minimize the number of holes, so that the distributed capacitance can be reduced and the mechanical strength of the PCB can be increased. In short, in the design of high-frequency PCB, the design of the pad and its shape, aperture and hole spacing should consider its particularity and meet the requirements of the production process. The standardized design can not only reduce the cost of products, but also improve the efficiency of production while ensuring the quality of products.
3.2 Applying Copper
The main purpose of copper coating is to improve the anti-interference ability of the circuit, and it has great benefits for PCB heat dissipation and PCB strength, and copper grounding can play a shielding role. However, a large area of strip copper foil can not be used, because the use of PCB for too long will produce large heat, at this time the strip copper foil is easy to expand and fall off, therefore, it is best to use grid copper foil when applying copper, and the grid is connected with the grounding network of the circuit, so that the grid will have a better shielding effect, the size of the grid grid by the interference frequency to be shielded The rate depends.
After completing the design of wiring, pads and holes, DRC(Design Rule Check) should be performed. In the inspection results, the differences between the designed graph and the defined rules are listed in detail, and the network that does not meet the requirements can be found. However, the DRC should first be parameterized before running it, that is, by executing the ToolsDesign Rule Check command.
4 Closing remarks
High frequency circuit PCB design is a complex process, involving many factors, may be directly related to the performance of high frequency circuit. Therefore, designers need to continue to study and explore in the actual work, accumulate experience, and combine the new EDA (electronic design automation) technology in order to design a high frequency circuit PCB with excellent performance.