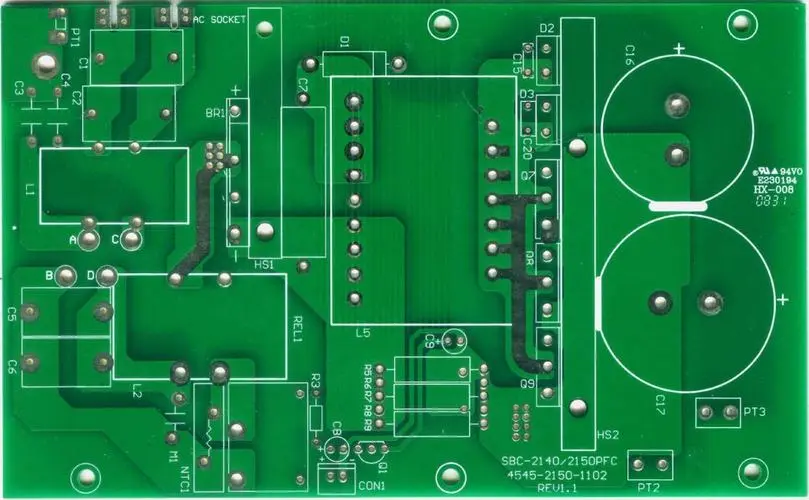
Short circuit is a common processing defect in the manual welding process of SMT chip. In order to achieve the same effect between the manual patch and the machine patch, the short circuit problem must be solved. If the PCBA circuit board is short circuited, it should never be used. There are also many ways to solve the short circuit problem in SMT chip processing
SMT chip processing
The manual welding operation should form a good habit. Use a multimeter to check whether the key circuit is short circuited. Every time the manual SMT placement is completed, use a multimeter to measure whether the power supply and ground are short circuited.
2. Light up the short circuit network on the PCB diagram, find the place on the circuit board where short circuit is most likely to occur, and pay attention to the internal short circuit of the IC.
3. If the short circuit occurs in the same batch during SMT chip processing, you can take a board to cut the wire, and then power on each part to check the short circuit
4. Use the short circuit positioning analyzer to check.
5. If there is a BGA chip, because all the solder joints are covered by the chip and cannot be seen, and it is also a multilayer board (more than 4 layers), it is better to separate the power supply of each chip during the design, and connect it with a magnetic bead or a 0 ohm resistance. In this way, when the power supply is short circuited to the ground, disconnect the magnetic bead detection, and it is easy to locate a chip.
6. Be careful when welding the capacitance of the small SMT chip processing surface, especially the power filter capacitors (103 or 104), which are large in number, can easily cause short circuit between the power supply and the ground.
Characteristics and Selection Requirements of Flux in PCBA Production
Flux is usually a mixture of rosin as the main component, which is an auxiliary material to ensure the smooth welding process. PCB welding is the main process of electronic assembly, and flux is an auxiliary material for welding. The main function of the flux is to remove the oxides on the surface of the solder and the base metal to be welded, so as to achieve the necessary cleanliness of the metal surface. Prevent the surface from re oxidation during welding, reduce the surface tension of solder, and improve the welding performance. The performance of flux directly affects the quality of electronic products.
Characteristics of flux in PCBA production
In general, the military and life support PCB products (such as satellites, aircraft instruments, submarine communications, life support medical devices, weak signal testing instruments, etc.) must use cleaning type flux; Non clean or clean flux can be used for other types of electronic products (such as communication, industrial equipment, office equipment, computers, etc.); General household appliances and electronic products can use cleaning free flux or RMA (medium active) rosin flux without cleaning.