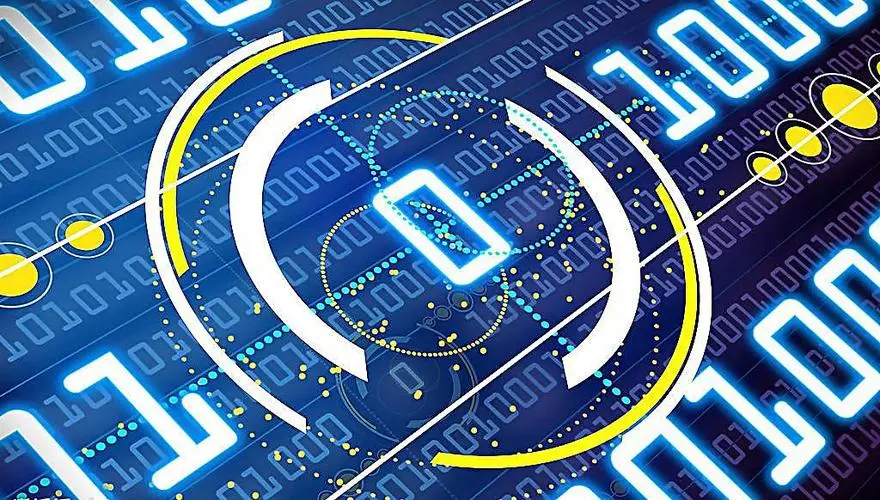
As the name implies, the color of the PCB board is the color of the oil on the board, which is often referred to as the color of the PCB board. The common colors are green, blue, red, black, and so on.
Green ink is the most widely used and oldest ink so far, and it is also the cheapest ink in the market today. Therefore, green is used by a large number of manufacturers as the main color of their products.
In general, the entire PCB product must go through the process of board making and SMT in the production process. In the process of board making, there are several processes that must go through the yellow light room, because the effect of green in the yellow light room is better than other colors, but this is not the main reason. When SMT is welding components, PCB will go through processes such as solder paste, patch, and final AOI calibration. These processes require optical positioning calibration, with a green background for instrument identification. Common PCB colors are red, yellow, green, blue and black. However, due to the production process and other problems, the quality inspection process of many lines still depends on the visual observation and identification of workers (of course, most of the current use of flying probe detection technology). It's a hard work process to keep your eyes on the board under strong light. Green is the least harmful to your eyes, so most manufacturers on the market use green PCB.
The principle of blue and black is that they are doped with cobalt and carbon elements respectively, which have certain conductivity. Short circuit problems are easy to occur when power is on, while green PCBs are more environmentally friendly than green PCBs, and generally do not release toxic gases when used in high temperature environments. In addition, a few manufacturers in the PCB market will use black PCB boards, mainly because Xiao Bian believes that there are two reasons: first, PCB boards look high-end; Second, it is difficult to see the wiring in the black board, so it is difficult to copy the board. What I learned is that most Android embedded boards currently use black PCB.
Since the middle and late last century, the color problem of circuit boards has attracted the attention of the industry, mainly because the color design of high-end circuit boards in many first-line large factories is green, so people slowly believe that if the color of circuit boards is green, they must be high-end.
What is the obvious difference between pcb board and aluminum substrate
For some small partners who just touch the aluminum substrate, the difference between aluminum substrate and PCB is still questionable. Today, I will specifically talk to you about this question.
Aluminum substrate is a kind of metal copper clad plate with good heat dissipation performance. Generally, the veneer is a three-layer structure, including circuit layer (copper foil), insulation layer and metal base layer. Printed circuit board, also known as printed circuit board, is a device that provides electrical connection of electronic components.
The circuit board belongs to a large category, and the aluminum substrate is just one of them, which is designed according to the requirements of pcb board. Generally speaking, the aluminum substrate is a single-sided PCB based on aluminum, which has good thermal conductivity and is generally used in the LED industry. Now the most commonly used LED aluminum substrate has two sides, the white side is the welding of LED pins, and the other side is the aluminum substrate. After contacting the heat conduction part, it is generally coated with heat conduction gel.
Usually, PCB refers to copper base. It can be divided into single-layer and multi-layer according to different layers. Compared with aluminum substrate, copper substrate and aluminum substrate. Due to the particularity of polypropylene material, aluminum substrate has better heat dissipation than PCB and is relatively expensive.