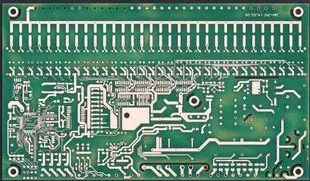
1、 PCB pads overlap
1. Overlap of PCB pads (except surface pads) means overlap of holes, which will lead to drill bit damage and hole damage due to multiple drilling at one location during drilling.
2. Two holes on the multilayer PCB board overlap. For example, one hole is the isolation plate, and the other is the connection plate (flower bed). Therefore, after the negative film is stretched, it will appear as an isolation plate, resulting in scrapping.
Second, the abuse of graphic layer
1. Some useless connections have been made on some graphics layers. At first, the four layer board was designed to have more than five layers of circuits, which caused misunderstanding.
2. The design requires less trouble. Take Protel software as an example, draw all the lines of each layer with the board layer, and mark the lines with the board layer. In this way, when the data is polished, the circuit will be cut off and the connection line will be missed because no board layer is selected, or the circuit will be short circuited because the marking line on the board layer is selected. Therefore, the integrity and clarity of the graphics layer will be maintained during the design process.
3. This violates the traditional design, for example, the surface design of components is at the bottom layer, and the welding surface design is at the top layer, causing inconvenience.
3、 Random placement of characters
1. The chip pad of the character cover brings inconvenience to the on-off test of the printed circuit board and the welding of PCB components.
2. The character design is too small, which makes screen printing difficult. Too many characters overlap and are difficult to distinguish.
4、 Setting of single pad hole diameter
1. One side welding pad usually does not drill holes. If the hole needs to be marked, the hole diameter shall be designed as zero. If a numerical value is designed, when the drilling data is generated, the coordinates of the hole will appear at that position, and problems will occur.
2. The single-sided cushion, such as drilling, shall be specially marked.
5. Drawing board with filler block
The drawing board with filler block can pass the inspection of the Democratic Republic of the Congo when designing the circuit, but it is not suitable for processing. Therefore, solder mask data cannot be generated directly for such PCB pads. When the solder mask is applied, the filler block area will be covered by the solder mask, which will lead to difficulties in device welding.
6、 The formation of electricity is flower pad and connection
Because the power supply is designed in a pattern of flower pads, the ground plane is opposite to the image on the actual printed board, and all connecting lines are isolation lines, which should be very clear to the designer. By the way, care should be taken when drawing isolation lines for several groups of power supplies or several types of grounding. No gap shall be left to short circuit two groups of power supplies or block the connection area (to separate one group of power supplies).
7、 Unclear definition of processing grade
1. The veneer is designed on the top floor. If not stated at the front and back, the panel may be fabricated with components installed instead of welding
2. For example, when designing a four layer board, the top middle layer 1 and the middle middle layer 2 and the bottom four layers are used, but they are not arranged in this order during processing, which needs to be explained.
8、 Too many filler blocks or extremely thin lines are filled in the design.
1. Data loss exists in the light drawing, and the light drawing data is incomplete.
2. Because fill blocks are drawn line by line in the process of light rendering data processing, the amount of light rendering data generated is quite large, which increases the difficulty of data processing.
9、 Surface mount device pad too short
This is for switch test. For too dense surface mount devices, the distance between the two legs is very small, and the bonding pad is very thin. In order to install the test pin, the upper and lower (left and right) staggered positions must be used. For example, if the pad design is too short, the device installation will not be affected, but the test pin will not open correctly.
10、 Large area grid spacing is too small
The edges between the same lines that make up a large area of grid lines are too small (less than 0.3 mm). In the process of PCB manufacturing, many damaged films are easily attached to the circuit board after image display, resulting in wire breakage.
11、 Large area copper foil is too close to the outer frame
The distance between the large area copper foil and the outer frame should be at least 0.2mm, because when milling the shape, such as milling the copper foil, it is easy to cause the copper foil to warp and the PCB solder mask to fall off.
12、 The outline frame is not clearly designed
Some customers have designed contour lines in the reserved layer, slab layer, top layer, etc. And these contour lines are inconsistent, which makes it difficult for printed circuit board manufacturers to determine which contour line should prevail.
13、 Inconsistent graphic design
When the pattern is electroplated, the uneven coating will affect the quality.