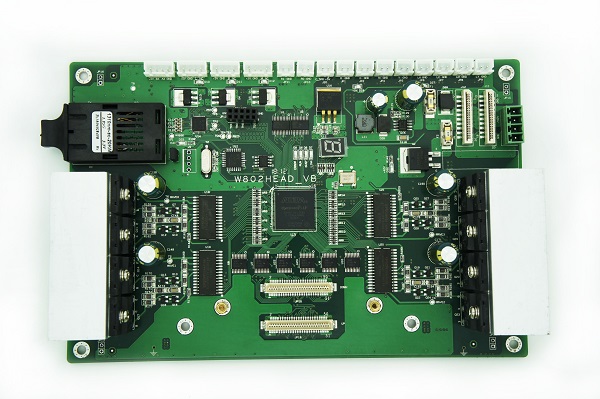
1. smt manufacturers shall assemble and deliver the finished products after smt assembly and processing. pcba manufacturers shall sort out inspection and test data and materials, issue qualification certificates, and prepare attached test boards and packaging materials for testing after passing the inspection. The delivery shall include accepted printed boards, certificates of conformity, necessary (or as stipulated in the contract) test data and attached test boards (for grade 3 products, multilayer boards shall at least include circuit on-off test data, metallographic microcut photos of coated holes).
2. Attachment test plate can add appropriate test graphics to the need of outside the borders of PCB (near the touchline lateral) as part of the in system board (makeup), and the need of PCB processing at the same time, at the end of the SMT processing finished form, to represent the finished circuit boards used to do some thermal stress such as voltage, resistance, simulate the rework and microscopic cutting has a destructive test. The attached test plate shall generally be marked by the batch number; When the circuit BOARD is in the form of a split-board for SMT assembly, the attached test board shall be marked as a printed board so that it can be traced from the attached board to the representative finished board. For grade 3 products, printed boards must be attached with test boards. For grade 1 and 2 printed boards, whether to attach test boards shall be decided by the user or stipulated in the contract.
3. Packaging, storage and transportation
(1) Packaging
smt SMT factory packaging is to ensure that qualified printed board products can withstand transportation, storage environment, without damage and quality degradation before use. The qualified pcb circuit boards shall be cleaned, dried and dehumidified according to regulations, cooled to room temperature and packed, then packed into polyethylene plastic bags or laminated plastic bags composed of polyethylene/polyamide and polyester/polyethylene for vacuum-sealed packaging, and the multi-piece multilayer boards shall be lined with neutral wrapping paper. It is usually packed with laminated plastic vacuum suction. If the storage environment is harsh and the storage time is long, and the storage conditions are beyond the specified, the plastic aluminum foil laminated bag made of aluminum foil and polyethylene or polyester film can be used as vacuum-absorbing packaging as agreed by the supply and demand parties. When LONG-DISTANCE transportation is needed, THE PACKED MULTILAYER board should be put into the packing box, the outer ring of the box is sealed, the box is lined with moisture-proof paper, and the desiccant is put in. Each batch of qualified products shall be accompanied by the product certificate. If the products are packed in boxes (or in other packaging forms), the packing list including the product name, finished product model, specification, batch, quantity, production date, packaging date, production unit and other contents shall be attached.
(2) In the process of storage and transportation, moisture and long exposure to the sun should be prevented, and contact with strong alkali, strong acid gas and mechanical damage should be prevented. The printed board boards should be stored in a clean container or box with a temperature of 10 to 35 ° C and a relative humidity of no more than 75%. The surrounding environment should not be acidic or alkaline.
Nowadays, SMT SMT processing technology has also become a major field of application of the process, the process will use different welding technology. But some manufacturers will find that there will be some quality problems in the processing process. Why and how to fix it?
1、, the thickness of the welding resistance film is larger
Due to the need to use welding resistance film in SMT patch processing, if the thickness of the welding resistance film is large, even if the overall thickness exceeds the thickness of the welding resistance film, it is easy to fail. Therefore, in this case, attention should be paid to the selection of a new welding form, and the suspension bridge design can be directly adopted, and then rewelded and machined.
SMT SMT processing
2, processing accessories meet the requirements
If in the process of processing, the size of the workpiece is not appropriate, there will be some pollution on the surface of the pad, leading to solder ball problems. These are SMT SMT processing prone to welding problems, so pay attention to the selection of appropriate accessories, especially the size of the problem. Only in this way can normal welding be ensured and other problems can be avoided.
If there are some quality defects in SMT SMT processing, we should understand the specific reasons. After all, there may be a variety of situations in the process. Need to fully check before processing, pay attention to whether there are other problems, timely adjustment. Only in this way can we reduce the occurrence of quality problems and complete product processing through these processes.