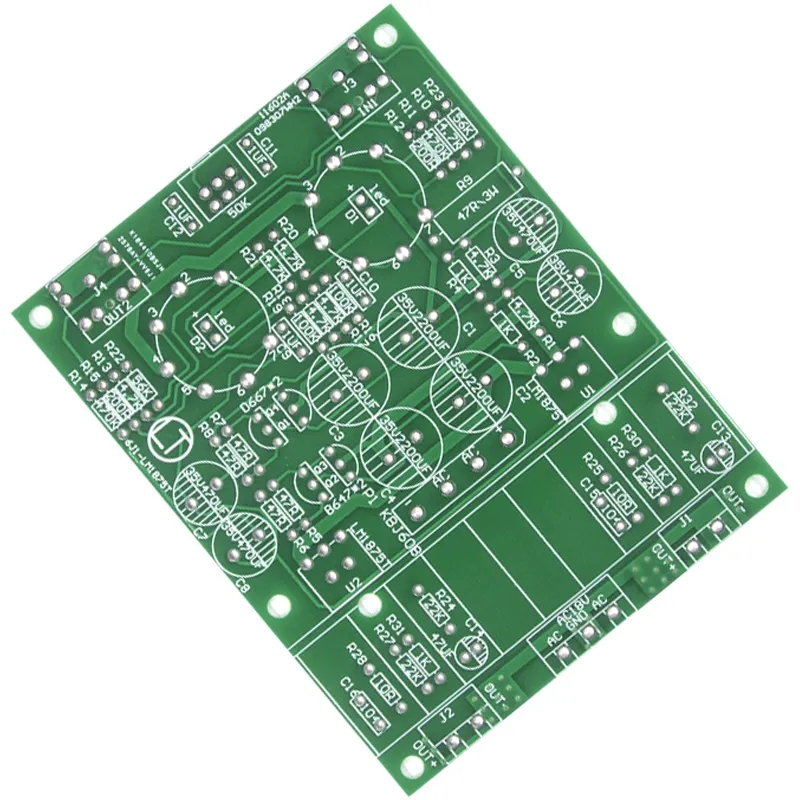
Work content of SMT processing
The circuit board manufacturer and circuit board designer will explain the work content of SMT processing in depth
1. Production planning process and preparation before production
The production workshop supervisor shall reasonably arrange the workshop plan according to the weekly and monthly plans of the planning department and in combination with the material supply situation, and reach the extension and technicians of each line in the workshop.
The foreman and technician shall make preparations in advance according to the issued production plan, and check whether there is steel mesh and whether the serial number is printed
The BOM list is confirmed, the placement machine program is confirmed, and the production process is confirmed.
The materialman shall count the production materials in combination with the ingredient list according to the production plan issued by the workshop, and send them to each line after counting. The solder paste and red glue shall be warmed up in advance according to the process requirements.
The equipment engineer, in combination with the weekly and monthly plans of the planning department, shall prepare the procedure for the new products to be sampled in advance.
The operator prepares the materials for the next work order in advance according to the workshop plan, and tests the steel grid setting and tension.
Before production, the technician shall check the program backed up in the computer into the mounting machine and transfer it out, adjust the track thimble of the mounting machine, check whether there are springboards and other errors in the program, and then load the material after confirmation, and adjust the use temperature of reflow products into the mounting machine and adjust the track.
Before production, technicians need to check the printing quality of the solder paste and red glue of the printing operator, whether the materials of the paster are in good condition, and whether FEEDER places them according to specifications. Production can only start after all are confirmed to be correct.
2. Work management during production and operation:
The printing operator needs to check the quality of solder paste every 1 hour, clean and check the steel mesh every 2 hours, test and record the thickness of solder paste, and handle simple faults of the printing machine. Problems that cannot be solved should be timely notified to the technician for solution.
The operator of the placement machine shall check the materials on the machine every 2 hours. If there is any abnormality in the material throwing inspection, the technician shall be notified in time to handle it. The placement quality shall be checked, and the simple failure of the placement machine shall be handled. If the problem cannot be solved, the technician shall be notified in time to handle it.
The inspector shall inspect the products according to the inspection specifications. If more than 3 problems with the same tag number are found continuously during the production process, the technician shall be notified in time to handle them.
During the production process, the technician shall check and confirm the machine throwing, solder paste printing quality, machine and equipment operation, and product quality every (two hours), check and record the reflow temperature, and timely solve the problems found, and timely notify the engineer or workshop leader and supervisor of the problems that cannot be solved.
The workshop leader shall supervise and guide the staff's production discipline, standardized operation, and track the achievement of production plan at any time.
The engineer shall supervise and guide the standardized operation of the equipment and check the operation of the machine.
3. The process of solving abnormal production problems:
In the process of SMT processing, when the production is abnormal and cannot be produced, or when more than 3 PCS of defective products with the same tag number and the same problem are continuously found, the operator shall immediately report to the technician, who shall promptly analyze and solve the problem, and analyze the reason that the product or process is not consistent with the standards or regulations due to machine failure, materials, process, design, human factors, and environmental factors, Develop solutions, implement and track them.
In case of abnormal material elongation, it is necessary to fill in the abnormality sheet in time, specify the reason for the abnormality and the defective ratio, and notify the production director to confirm the review. After the confirmation by the production director, it is necessary to submit it to the production manager for confirmation, and finally to the quality department for confirmation and analysis. If it is necessary to return the materials after the exception list is replied, the material clerk shall be notified in time to return the abnormal materials.
If the equipment abnormality cannot be solved by the technician, the engineer shall be notified in time to solve the problem. If the engineer cannot repair the problem, the engineer shall report to the production manager. After the production manager confirms, the engineer shall notify the manufacturer's maintenance engineer to repair the problem in the factory, and register the cause of the abnormality in the "Equipment Record".
For the abnormalities fed back by the later section (welding, inspection, maintenance, quality), the shift leader shall be responsible for filling in the causes of the abnormalities, and the technician shall write in the analysis of the causes of the outflow and the improvement measures, and then submit them to the workshop director for confirmation. The foreman and technician shall implement the improvement measures strictly, and the workshop supervisor is responsible for tracking and confirming the improvement of subsequent production.
4. Management of SMT procedures and new products:
In combination with the monthly plan and the BOM and PCB tag number map provided by the Engineering Department, the engineer prepared the product program for new product proofing in advance to ensure that the program can be produced before going online.
For permanent BOM changes issued by the Engineering Department, the engineer shall immediately modify the computer backup program. After the modification, the engineer shall copy the new program to the computer backup to cover the old program, including the program stored on the machine, to ensure that the product can be directly produced without adjusting the program before going online.
The first production of new product proofing; The engineer shall check the program into the machine coordinate, angle and parts database to ensure the smooth and qualified production of new products.
After the new product proofing is completed; The engineer shall make a summary report on the product, and notify the production technician, quality, engineering and planning personnel of the proofing summary report by email for subsequent improvement. The engineer shall track the improvement during the next production, and feed back to the relevant personnel if there is no change.
The production technician cannot change the procedure (patch tag number, material change, FEEDER tag number change) without permission. The technician's main authority for patch machine modification is: program input, position coordinate adjustment, position angle adjustment, alarm information cancellation, and part database adjustment.
5. Machinery and equipment management:
Equipment acceptance:
The equipment engineer shall conduct commissioning and acceptance according to the requirements of the order contract and the specifications and performance data provided by the manufacturer.
When the supplier delivers the equipment to the factory, the engineer shall be responsible for receiving and acceptance. After the acceptance is qualified, the acceptance related contents shall be filled in the "Equipment Resume", and the relevant units shall put forward comments and countersign. Finally, the General Manager shall sign off (according to the company's order approval authority) and send the draft of "Equipment Record" to the procurement department.
Create equipment data:
After the equipment acceptance, the engineer shall log in the "List of Equipment and Fixtures", and shall establish the "Equipment Record" of the equipment, as well as various equipment use specifications and maintenance point inspection forms. The record shall include the product name, number, value, payment, supplier/brand, common identification, date of putting into use, date of damage and scrapping, and service life. The updated account shall be shared for the convenience of each department to consult and understand.
The equipment shall be numbered according to the coding principle and managed in parallel with the standing book.
All equipment accompanying data shall be kept by the equipment engineer, and the user unit or technician shall borrow them from the equipment engineer when they need to borrow them. The equipment engineer shall keep the equipment accompanying data account and borrowing account.
Maintenance work:
The production operator must carry out daily spot check and maintenance of the machine in accordance with the maintenance spot check list formulated by the engineer.
The production technician must carry out daily point inspection, weekly maintenance and specified test of reflow furnace temperature according to the maintenance point inspection table formulated by the engineer.
The production engineer must carry out monthly and annual maintenance according to the maintenance point check list.