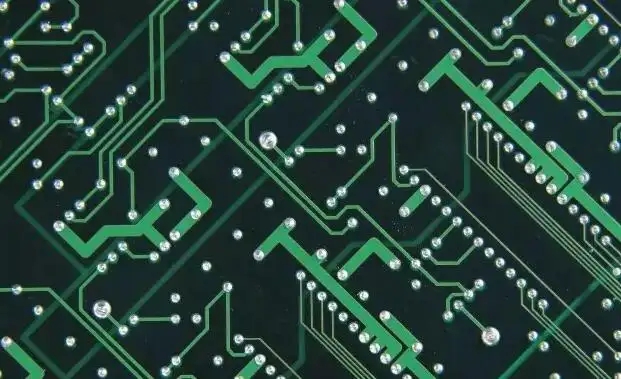
MRB meeting of manufacturing plant and quality judgment of plastic parts
MRB meeting of PCB quality manufacturing factory and quality judgment of plastic parts
I remember when I first worked as a product engineer in a PCBA processing factory, I often had to attend MRB (Material Review Board) meetings, and I was often asked to judge whether some parts that were rejected could be used by special purchase. Otherwise, the production line would be in danger of breaking materials and stopping the line, and few people could afford the loss of starting and stopping the line. At that time, the most annoying thing to encounter was plastic parts, but more than 70% of the defective returned parts in the finished product assembly factory were almost related to plastic parts.
Note: MRB (Material Review Board) is usually composed of distribution, Planner, quality control, process and other units in PCB manufacturers to discuss and solve various difficult and miscellaneous problems in production.
Because the dimensional variability of plastic parts is often very large, structural deformation, insufficient shrinkage or too large are often caused when the plastic parts are not noticed during injection molding, resulting in dimensional overrun. Sometimes these problems clearly do not need to be paid too much attention to, but the designer will mark the tolerance mark very small in the dimension marking, and some will also be marked as [key dimensions], so it is often necessary to pick up these overrun parts for actual assembly, To confirm whether it can be used and whether there is any problem in function, sometimes we have to communicate the dimensional tolerance with the design engineer. If there is enough time and capability, these problems should be raised at the stage of DFM (Design For Manufacture) review before mass production. However, as the pre production work for product launch is getting shorter and shorter, many people will ignore these pre production work intentionally or unintentionally on the pretext of time pressure, and become a war.
However, the problem of plastic size and structure can be solved, because it is usually my (process/engineering) the final say whether to do or not. Anyway, I am still responsible for functional problems in the future. The most annoying problem is the cosmetic problem, because the appearance problem can be accepted by everyone. At this time, it is necessary to work with the quality control engineer to set standards. When there are plastic parts of different colors, use a color difference meter, and then measure what a, b The delta value and so on, but finally it is judged by the naked eye. It is determined by looking at it once under the fluorescent lamp and sunlight respectively, because sometimes the difference between the values is small, but it seems uncomfortable.
As for scratches and dirties, their specifications will also be determined. Scratch will define how deep, wide and long the scratch is; If it is a stain, it defines the diameter, number of points and distance of the stain; The troublesome part is the texture. The texture is usually blurred or faded after the plastic is injected for a period of time. Generally, we will make samples, and then sign samples with engineers from relevant departments. When there is a problem, we will compare the signed samples with the signed samples.
At that time, there was an interesting question, which was "burr" in English. I always wondered why the burr of metal parts was called "burr", while the burr of plastic parts was called "flash". I always thought that flash meant flash. It should be used for the burr of metal? Later, a colleague told me that at the beginning of human history, there was no metal or plastic processing. Burr originally meant "prickly fruit" in English, which means that plants have prickly fruit. Later, with the development of industry, metal processing products began to appear. When people found that metal objects had burrs similar to prickly fruit, they called the burrs on the metal as burr. Later, plastic parts appeared to distinguish the two, So the rough edges of the plastic are called flash. This is the answer that others told me. I don't know whether it is true, but I think it is acceptable!
The circuit board manufacturer and circuit board designer will explain the MRB meeting of the manufacturer and the quality judgment of plastic parts.