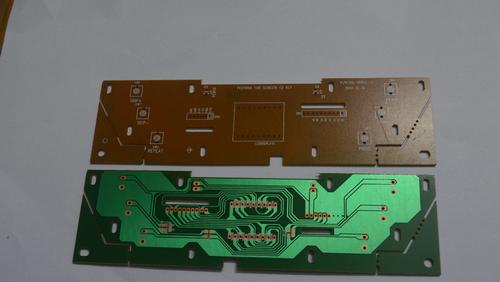
PCB problems can only be solved by quality control engineering?
、
To solve the quality or customer complaints of electronic products, we usually have to use 8D or Problem Solving to find the real cause step by step and take solutions. However, some problems can not be solved through quality control engineering. At this time, only personal investigation can find the answer.
If it is a problem on the production line, it is recommended that each process should be run once or even more times in person, because sometimes the problems that occur on the site are not unimaginable, and there are various strange reasons for various strange things to happen; If it is a problem with the client, it is better to go there and confirm that the problem occurred when unpacking, and observe how the client operates the product, because most customers don't say they have a problem at all, and some customers don't know they have a problem at all.
Case I: SMT solder is poor
SMT always has poor soldering. The engineer checked the solder paste usage time, solder paste printing, circuit board quality, part quality, and furnace temperature from beginning to end, but he couldn't find the problem. Later, after watching the product process for more than four hours on the production line, he suddenly found that the operator used alcohol to scrub the steel plate and blew it dry with his mouth. Instead, he left saliva on the steel plate. No wonder there was no problem everywhere.
In addition, after the steel plate is cleaned, an air gun is usually used to clean and dry it. At this time, check whether the compressed air has water and oil filtering equipment. Otherwise, the air blown out may contain oil and water, causing pollution to the steel plate.
Case 2: The mainboard jumper is lost
The computer motherboard is often complained by customers that the [jumper] is missing. The engineers studied the pulling force of the jumper and worked out the specifications in detail, which caused the supplier to flip his horse. However, they continued to receive complaints from customers. Later, they flew to the customer's workplace to visit. It was discovered that the customer needed to remove the "jumper" first when installing the display adapter, and then install the jumper back after the display adapter was installed, But at lunch time, the jumper pulled out was placed at random. After dinner, he returned to work. He forgot where the jumper was placed or accidentally lost it, so the customer complained that there was no jumper.
At this time, the solution is definitely not to go to the customer to protest against their operation methods and need to be improved. Even if you win the argument now, you may lose the order or get more customer complaints in the future. Therefore, the solution is very simple, that is, you can give the customer a packet of jumpers for free. A packet of jumpers does not cost much, but you can get 100% satisfaction from the other party.
Case 3: Circuit board oil contamination
Previously, we posted a blog explaining that the oil stain and white powder on the circuit board caused a customer complaint about poor buttons. At that time, we couldn't find any possible sources of pollution. Although we did Fourier analysis later and confirmed that the flux was one of the sources of pollution, we just didn't know why the flux was stained on the key circuit.
Later, our resident personnel stationed in the pcb generation factory persevered and filtered all possible actions of using flux. They came to the conclusion that the operator accidentally used the flux as IPA alcohol, so that the flux was mixed with alcohol without knowing it, and it was directly used to wipe on the line of keys.
If you are not familiar with the manufacturing process and filter the problem step by step, it is really difficult to find the cause.