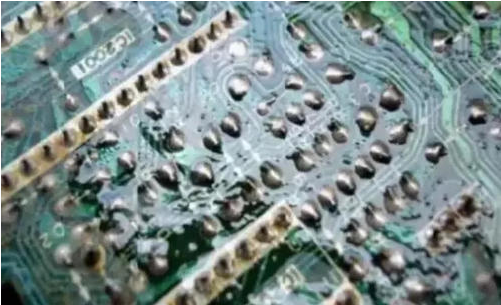
For a product, reliability is the guarantee for its performance. If the product is not reliable, its technical performance will not be brought into play even if it is good. "Product reliability" is equivalent to whether the product is reliable! In other words, "high reliability" means that the product life is longer, and there are few or no failures in the PCB product life cycle!
With the rapid development of science and technology, all walks of life put forward higher and higher requirements for product reliability! Product reliability has become the inspection and evaluation index of product quality, and also an important weight for enterprises to enhance competitiveness and brand image!
1、 The Importance of High Reliability in Improving the Market Competitiveness of Electronic Products
In 1992, China failed to launch the "Ostar" due to the failure of a small part, which caused huge economic losses and political influence! Japan's automobile, household appliances and other products occupy the international market, mainly because of their high reliability. The overhaul period of American Kangxi diesel engines is 12000 hours, while domestic diesel engines frequently break down in less than 1000 hours
For products, reliability is closely related to "maintenance costs, operating efficiency, property safety, casualties, economic benefits, national security", etc. High reliability is an important guarantee to enhance the market competitiveness of electronic products
The Importance of PCB High Reliability
1) Only highly reliable PCB can meet customers' market development needs
A major feature of the development of modern science and technology is the highly complex equipment structure, which is marked by the complexity of component demand types and data. PCB is the core carrier of electronic products linking components. The more layers, components and process requirements, the greater the reliability impact, and the higher the requirements for PCB reliability. Only highly reliable PCBs can meet the development needs of customers.
2) Highly reliable PCB can help customers improve their market competitiveness
Before World War II, Japanese electronic products were once returned to customers in large quantities due to poor reliability, and even were almost forced to withdraw from the international market. After World War II, Japan learned from the lessons and continuously improved the reliability level of electronic products, which ultimately greatly improved its market competitiveness and forcefully seized a huge international market share. Under the double impact of the financial crisis and the COVID-19, the current international market competition is particularly fierce. For "Fanyi", only by improving the reliability of PCB, can we help customers improve brand reputation and continuously enhance market competitiveness!
3) Highly reliable PCB can help customers obtain higher economic benefits
In 1961, at least 25% of the budget of the US Department of Defense was for maintenance. For antenna products sold in the European or North American markets, due to the need to hire qualified professionals for tower operation, there is little difference between the maintenance cost and the price of single antenna. In order to improve the reliability of a certain product, Westinghouse once conducted a comprehensive review, and found that improving the reliability level can greatly reduce the maintenance cost of electronic equipment; On the surface, the cost of early production and control with high reliability will be higher, but the failure rate in the later period will be less, and the maintenance cost and downtime loss will be lower. In order to help customers maximize economic benefits, "Fanyi" is more obsessed with making PCB right, good and reliable at one time!!
PCB Failure and Its Consequence Analysis
The failure of PCB life cycle is highly related to reliability, and the failure consequences caused by low reliability of PCB are also very shocking.
As the carrier of electronic components and the hub of circuit signal transmission, PCB has become one of the most important and critical core components in electronic products. Its quality and reliability directly determine the quality and reliability of the electronic machine.
With the increasing miniaturization, lightweight, multi-function of electronic products, and the continuous promotion of lead-free, halogen-free and other environmental requirements, the industry is moving towards the direction of "thin lines, small holes, multiple layers, thin boards, high TG, high frequency, high speed, high density, and environmental protection", which has led to the increasingly complex internal structure of PCB, increased internal temperature rise, and deteriorating heat dissipation conditions, greatly affecting the reliability.
Secondly, the use environment of electronic products varies greatly, from tropical to cold zone, from land to deep sea, from high altitude to space, from laboratory to field... In addition to the influence of temperature and humidity, various environmental conditions such as sunlight, dust, sea water, salt fog, impact, vibration, cosmic particles, and various kinds of radiation will have different degrees of influence on PCB, and even lead to product failure. For example, in the coastal high salt and high humidity environment, a thin layer of water film will form on the surface of the object, and when the relative humidity is 65% - 80% in the air, the thickness of the water film on the object is 0.001~0.1 μ m. When PCB is working with electricity, the water film and porous copper together form an electrolytic cell, which generates electrochemical reaction and finally generates black corrosives, posing a fatal risk to PCB reliability.
The causes of PCB failure are various and different. For example, the corrosion failure of PTH hole copper, the open circuit failure caused by the cracks at the bottom of HDI blind hole, the failure of layered bursting, the failure of ENIG hole ring cracks, the open and short circuit failure, etc. Different failure types will eventually affect the maintenance costs, business efficiency, economic benefits, brand image, and even may endanger property safety, casualties, and national security!
2、 High reliability comes from high standards for quality and high requirements for production
"High reliability" is the distinctive banner of enterprises based on the market, enabling customers and fulfilling social responsibilities. Since its establishment, "Fanyi" has attached great importance to reliability. It has done a good job of "high reliability" with "high investment, high standards and high requirements". After nine years of hard work, forge ahead and develop to the present ", it has spared no effort to call on the industry to" emphasize reliability ". The reason is that" high reliability "is not only related to the long-term and steady development of the enterprise itself, but also directly affects the brand reputation of downstream customers Even the market image of the industry and the country in international competition.
The circuit starts from the end and never wavers in its mission
Never forget, there must be an echo! Guided by "providing customers with highly reliable PCB"! Starting from the results backward, from the output backward to the input, from the problem backward strategy, by defining the enterprise vision, business philosophy and quality philosophy, and then improving centripetal force, cohesion, create a goal oriented efficient team, and then reverse analyze and comprehensively sort out the production standards and quality control specifications of PCB plants, analyze the key influencing factors of reliability, locate the key management and control processes of reliability, and establish a reliability oriented improvement system, Fulfill commitments with actions to ensure the high reliability of PCB in an all-round way.