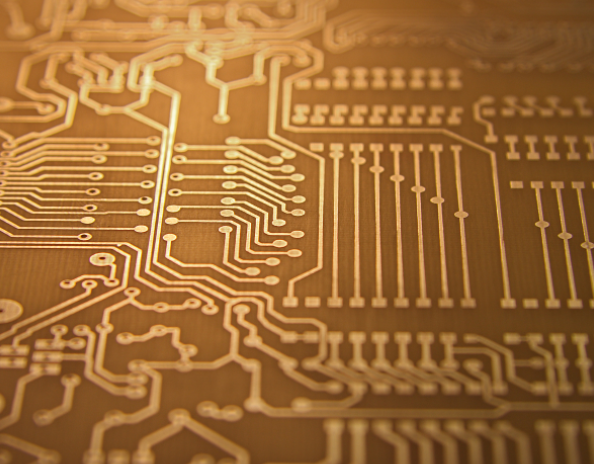
Analysis of PCB welding defects
1 Introduction
Welding is actually a chemical process. Printed circuit board is the support of circuit components and equipment in electronic products. It provides electrical connection between circuit components and equipment With the rapid development of electronic technology, PCB density is getting higher and higher, and there are more and more levels Some all the designs may be correct (such as the circuit board is not damaged, etc Therefore, it is necessary to analyze the factors affecting the welding quality of PCB, analyze the causes of welding defects, and improve these causes to improve the welding quality of the entire PCB
Printed circuit board
2. Reasons for welding defects
2.1 PCB design affects soldering quality
In terms of layout, when the PCB size is too large, although the welding is easier to control, the printed line is very long, the impedance is increased, the noise resistance is reduced, and the cost is increased; Interference, such as electromagnetic interference of circuit board Therefore, the PCB board design must be optimized: (1) Shorten the connection between high frequency components and reduce EMI interaction (2) Components with heavy weight (such as more than 20g) should be fixed with brackets and then welded. (3) The heat dissipation problem should be considered for the heating element to prevent defects and rework caused by large Î T on the surface of the element, the thermal element should be far away from the heat source (4) the arrangement of The components should be as parallel as possible The circuit board is designed as a 4:3 rectangle Do not change the wire width suddenly to avoid wire interruption When the circuit board is heated for a long time, the copper foil is easy to expand and fall off Therefore, avoid using large area copper foil
2.2 The solderability of the circuit board holes affects the soldering quality
The poor solubility of the circuit board holes will cause virtual welding defects, which affect the parameters of components in the circuit, lead to unstable conduction of components and inner layers of multilayer boards, and lead to functional failure of the whole circuit Solderability refers to the property that the metal surface is wetted by molten solder. That is, a relatively uniform, continuous and smooth adhesive film is formed on the metal surface where the solder is located The composition of the solderability and the properties of the solderability Solder is an important part of welding chemical treatment process It consists of chemical data containing flux The commonly used low melting point eutectic metals are Sn Pb or Sn Pb Ag The impurity content must be controlled at a certain proportion to prevent the oxide generated by impurities from being dissolved by the flux The function of flux is to help solder wet the circuit surface of the circuit board being welded through heat transfer and rust removal White rosin and isopropanol solvents are usually used (2) The soldering temperature and the cleanliness of the metal plate surface will also affect the solderability. If the temperature is too high, the diffusion speed of solder will be accelerated At this time, its activity is very high. It will rapidly oxidize the molten surface of the circuit board and solder, resulting in welding defects Contamination of the circuit board surface can also affect solderability and cause defects These defects include tin bead, tin ball, open circuit, poor gloss, etc
2.3 Welding defects caused by warpage
The PCB and components are warmed during the welding process Warpage is usually caused by the temperature imbalance between the upper and lower parts of the PCB For large PCB, warping may occur due to the weight reduction of the board itself Ordinary PBGA devices are about 0. 5 mm from the printed circuit board. If the equipment on the circuit board is large, when the circuit board returns to its normal shape after cooling, the solder joint will bear stress for a long time If the equipment is triggered by 0. 1mm, it is enough to cause false welding When the PCB is warped, the component itself may also be twisted, and the solder joint located in the center of the component is lifted from the PCB, resulting in empty soldering This usually occurs when only flux is used to fill the gap without solder paste When using solder paste, the solder paste and solder ball are connected together to form a short circuit defect due to deformation Another reason for the short circuit is that the component substrate delaminates during the reflow process This defect is characterized by the formation of air bubbles under the device due to internal expansion X-ray inspection shows that solder short circuit is usually located in the middle of the equipment
3. Conclusion
To sum up, improve the solderability of PCB holes by optimizing PCB design and using high-quality solder to prevent warping and defects. The overall welding quality of PCB can be improved