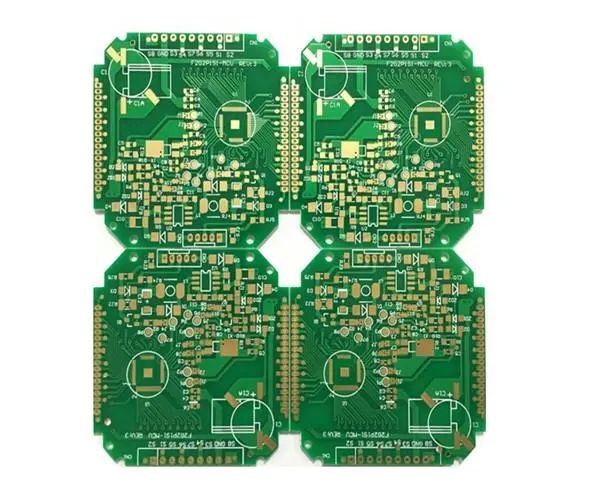
The small editor of PCB manufacturer introduces the competitiveness analysis of PCB industry
At present, the output value of the global PCB industry accounts for more than a quarter of the total output value of the electronic component industry, and it is the largest proportion of each electronic component sub industry, with an output value of 40 billion dollars. At the same time, due to its unique position in the electronic basic industry, and also the most active industry in the contemporary electronic component industry, the proportion of printed circuit boards in the total output value of electronic components is increasing, because with the adjustment of the product variety and structure of the whole machine, the required area of printed circuit boards in the final product of a single machine is gradually reduced, but due to the improvement of precision and complexity, the proportion of PCB value in the cost of the whole machine is increasing, It is the main pillar of the development of electronic component industry. In the electronic component industry, the output scale of PCB industry is only in the semiconductor industry. With the continuous expansion of PCB application field, its importance is still further improved.
We selected the data of three listed companies as reference samples. We are also engaged in the production and sales of other products. For the sake of comparability, we focus on the gross profit margin of their printed circuit boards. It is roughly inferred from the situation of these enterprises that the average gross profit of PCB industry is about 20%.
1. Competitors
The competition among peers is fierce: the enterprises in the industry are divided into three levels: high, medium and low. The middle and high end are dominated by foreign capital, Hong Kong capital, Taiwan capital and a few state-owned enterprises. Domestic enterprises are at a financial and technological disadvantage. Low end refers to small plants that operate irregularly. Due to less investment in equipment and environmental protection, they have cost advantages. At the middle end level, manufacturers are concentrated, and the competition is more fierce. Since 2006, some manufacturers have been rebuilt and expanded, which is difficult for the market to digest quickly, and the price war is becoming increasingly fierce.
The industry concentration of an industry can reflect the intensity of competition in the industry. At present, there are many enterprises in the domestic printed circuit board industry, and the market concentration is low, which reflects that the production scale is difficult to expand and is restricted by the supply of raw materials.
2. Substitutes
Printed circuit board has been widely used in a large number of electronic products. At present, there is no mature technology and product that can replace printed circuit board. The basic manufacturing process of PCB, "reduction method", has not changed significantly in recent decades: that is, the metal is etched by screen printing to obtain PCB, which is the origin of the name of printed circuit board. Because this production process is not environmentally friendly enough and produces a lot of waste water and waste gas, many institutions have started to develop other processes that are fundamentally different from traditional circuit board production methods, such as inkjet circuit boards, photolithographic circuit boards, etc.
The "ink-jet technology" PCB uses liquid metal instead of ink to spray it from the print head, spray the necessary materials to the necessary positions, and form a metal film. With the application of "liquid film forming technology", the circuit patterns on the chip can be described as if they were printed by a printer. Compared with the traditional "photographic flat panel technology", the PCB production process based on inkjet technology has many advantages: because the circuit is only formed where needed, it can save a lot of raw materials; Because the whole process is a dry treatment process, no waste liquid will be produced; The reduction of production steps reduces energy consumption; Moreover, this process is also very suitable for high mixing, small batch production and multi-layer structure production. What's more, the whole process based on ink-jet technology is an environment-friendly and low environmental load production process.
Due to the cost, this kind of circuit board is far from mass production at present; However, in the case of increasingly serious environmental problems, this is a development trend.
3. Potential entrants
Complete machine assembly manufacturers add in house layout to reduce costs.
The rise of Southeast Asia: because the cost of labor and environment is lower than that of China, it has attracted a lot of foreign capital to invest there; Especially in India, there is a great demand for PCB in its own market. Low end products, such as single and double sided PCBs, have low entry costs and investment, and manual workshops can survive with low cost operation.
4. Supplier's power
Affected by the rising price of upstream raw materials, suppliers have the power to rise to maintain profitability. PCB suppliers are highly concentrated and have strong bargaining power.
Copper clad plate, copper foil, semi solidified sheet, chemical solution, anode copper/tin/nickel, dry film, ink and other products are the main raw materials required for PCB production. The proportion of raw material cost in the cost is 66%. In recent years, due to the sharp rise in the price of oil and non-ferrous metals, the cost of raw materials has increased significantly.
CCL accounts for about 40% of the total PCB production cost, which has the largest impact on PCB costs. Large PCB companies will sign long-term contracts with CCL plants to reduce the impact of raw material price fluctuations.
It can be seen that at present, the PCB industry is facing fierce competition, threats and challenges continue to exist, and the industry is generally attractive.