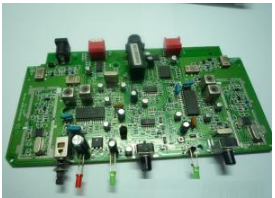
Reflow soldering is an indispensable manufacturing stage in SMT chip processing, and it will continue to endanger the welding quality of SMT chip processing. At present, most SMT production, processing and welding in the factory are all reflow processing processes. So what exactly is reflow soldering? The following technical professional PCBA chip processor Fanyi Circuit gives you a simple introduction.
In simple terms, reflow soldering actually means that there is a heating power circuit in the welding furnace, which heats the gas or N2 to a sufficiently high temperature and blows it to the pcb circuit board with components already attached, so that the solders on both sides of the components are melted and bonded to the computer motherboard. This kind of production and processing method can accelerate the whole process of SMT welding to a level that can not be reached by manual production and welding, and can easily complete mass production, and the cost of PCBA production and processing can be reasonably controlled.
PCBA processing
In reflow welding, the welding layer of PCBA based steel plate is first covered by solder paste, which is generally the compound of solder, small ball and bead of soldering fluid.
The solder paste is automatically packaged and printed according to the position of the screen plate, so that the solder paste can only be left in the area where the terminal blocks of components must be welded.
After SMT components and parts are mounted on the PCBA base steel plate, the quality inspection outside the furnace is carried out. It is determined that the quality clearance board will be put on the chain rail and transferred to the reflow soldering furnace, and the temperature will rise above the solder melting point in the reflow soldering mechanical equipment. Then the solder flows back to the terminal block of the device, and then the circuit board
Precautionary Techniques for Welding Porosity in PCBA Processing
Porosity caused by PCBA plate welding, also known as bubble, is generally caused by flow back welding and wave soldering during PCBA processing. So how to prevent porosity caused by PCBA production, processing and welding?
1. Baked
PCB and electronic devices exposed to air for a long time shall be baked to avoid moisture.
2. Solder paste supervision
Solder paste with moisture is also very easy to cause pores and solder beads. Solder pastes with high cost performance ratio shall be used first. The temperature rise and mixing of solder pastes shall be strictly observed according to the actual operation. The time for the solder pastes to be exposed to the air shall be as short as possible. After the packaging and printing of solder pastes, the solder pastes must be immediately returned for welding.
3. Workshop environment humidity supervision
The environmental humidity of the monitoring workshop with the scheme is controlled between 40-60%.
PCBA welding
4. Set effective furnace temperature curve
Carry out temperature control detection twice a day to improve the furnace temperature curve, and the temperature rise speed cannot be too fast.
5. Flux painting
When passing the wave crest welding machine, the amount of spray paint of the flux shall not be too much, and the spray paint is effective.
6. Raise furnace temperature curve
The temperature of the heating zone shall be specified, and shall not be too low, so that the flux can be fully evaporated, and the speed of passing through the furnace shall not be too fast.
There will be many elements harmful to bubbles, which can be analyzed from the aspects of PCB design, PCB environmental humidity, temperature control, flux (spray size), chain speed, tin wave height width ratio, solder wire composition and so on. It is possible to get a good manufacturing after several adjustments.