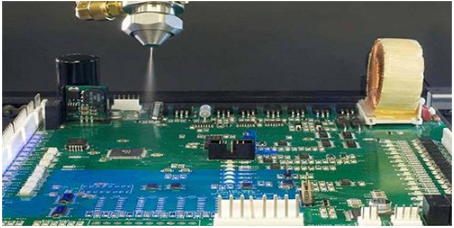
PCB assembly technology has reshaped our world in many ways, but the most important impact is in on-site medical care. Diagnosis is the most critical aspect, and electronic medical devices may be helping it. There are many machines related to the medical field on the market. X-rays, CT scanners, ultrasound, medical images and MRI are all part of this. It does not end here, there are treatment, life support, monitoring, treatment and laboratory equipment; Or medical wearable PCB devices. In order to achieve the goal of producing the best product in the field of medical engineering, specific steps are required. It starts with concept, research on circuit design, printed circuit design, packaging, prototype design, design review, manufacturing setup and quality assurance. Circuit design, packaging and prototype design are the most important parts. PCBA stands for printed circuit board assembly. Because components are attached, they are called components. The printed circuit board is a green chip on which components are assembled. Assembly is a printed circuit board specially designed for relevant medical equipment.
Medical device PCB
PCB manufacturing of medical equipment
Manufacturing is another important step towards product completion. After designing the circuit, the next step is to make it into product shape. Prototyping of the product is required to evaluate the results. Medical PCB manufacturing is one of the last steps that the final product must be sold on the market. It is worth noting that medical PCB manufacturers should have sufficient knowledge of the final product design. Medical devices have some strict requirements on the size of the final product. In addition to size, there are other special requirements, such as fluid resistance. Here is an interesting example of a pacemaker. It must be installed in the human body. The design of medical device PCB should be the unique feature of these applications.
Biological science equipment is bound to bring us a promising future. It enriches our way of life. Every year we encounter hundreds of new devices. With the emergence of medical wearable PCB devices and their 18% growth, they are very important to PCB design industry every year. The US market will only exceed US $8 billion in 2018. Whether you are developing fitness equipment, health diagnosis equipment or automatic treatment equipment, it is a unique challenge to make medical wearable PCB equipment suitable for human body each time. These equipment must be sturdy for some time. But for certain applications, it must be waterproof. Scale is still an important part of innovation and progress in the electronics industry. Multilayer PCB really improves the product results. When it comes to the size of the final product, the main factor determining the optimization space is PCB design.
The future of medical engineering will greatly change the industrial demand of PCB industry. Electronic equipment is designed to meet the requirements of the medical industry. Both diagnostic and laboratory equipment are part of our common needs. Some medical devices are a source of life support for millions of people worldwide. A specific example of life support equipment is dialysis equipment; Many patients survive by using it. There are eight different steps in designing a medical device PCB or any electronic product. The most important steps are circuit design and PCB assembly. Medical PCB assembly is the process of adding components to the printed circuit board to design devices, which is another step of product design in manufacturing. Biomedicine is considered as one of the emerging approaches in the future, with 8 billion dollars in the United States alone. Wearable devices have become very popular in the past few years, and it has challenged PCB manufacturers to optimize production and small design. The requirements for medical devices are not limited to small designs. Specific applications require rugged, fluid resistant PCBs. Finally, the manufacturing of medical equipment PCB occupies an important part of the electronics and PCB assembly industry.