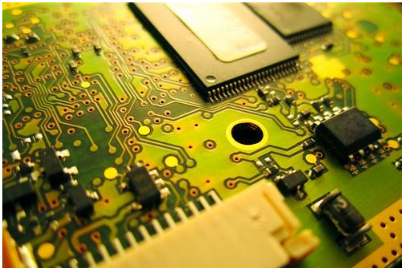
Circuit board is also called board, high-frequency board, thick copper board, impedance board, ceramic board, circuit substrate, etc. It is the carrier of electrical connection or electrical insulation between various electronic components and plays a vital role in circuit layout and optimization; At present, the commonly used substrate materials mainly include:, resin substrate, and metal or metal matrix composites, among which ceramic substrate has become the preferred material for high-power electronic circuit substrate due to its excellent electrical insulation, stable chemical properties, thermal conductivity, mechanical strength, puncture resistance and high temperature resistance; Common ceramic substrate materials on the market mainly include beryllium oxide ceramics, alumina ceramics and aluminum nitride ceramics.
Ceramic substrate
1、 Beryllium oxide (BeO) ceramic substrate: its thermal conductivity is up to 250W/(m.K), which is a dielectric material with unique electrical, thermal and mechanical properties; However, due to its highly toxic powder, long-term inhalation will cause life danger and serious environmental pollution, which is why beryllium oxide ceramic substrate has not been widely used.
2、 Aluminum nitride (AlN) ceramic substrate: aluminum nitride ceramics are high thermal conductivity ceramic materials that are expected to partially replace beryllium oxide ceramics; Its thermal conductivity is up to 200W/(m.k), which has good thermal conductivity, mechanical strength, high temperature resistance and stable chemical properties; Due to the process and raw materials, the price is higher than that of alumina ceramics, which is why many manufacturers prefer to choose alumina ceramics with poor performance as the substrate.
3、 Alumina (Al2O3) ceramic substrate: alumina ceramics have the advantages of low dielectric loss, high mechanical strength, good chemical stability, etc; Although its thermal conductivity is only 28W/(m · K), alumina is more easily accepted by manufacturers in terms of price due to its rich access to raw materials and mature processing technology.
Performance advantages of iron base plate
PCB iron substrate is widely used because of its good thermal conductivity, heat dissipation, electrical insulation and mechanical processing properties. In the process of PCB manufacturer, it is clear that PCB iron base plate can be divided into three layers, namely circuit layer (copper foil), insulation layer and metal base layer. PCB iron base plate is widely used in LED, air conditioner, automobile, oven, electronics, street lamp, high-power, etc. Why can the iron base plate be so widely used and used in high-tech products. The thermal expansion, dimensional stability, heat dissipation and other properties of PCB iron base plate enable it to meet more demanding products. Now let's introduce the related performance of PCB iron base plate.
Iron base plate
PCB heat dissipation: At present, many double-sided boards and multilayer boards have high density, high power and difficult heat dissipation. Conventional printed board substrates, such as FR4 and CEM3, are poor thermal conductors, which are insulated between layers and cannot emit heat. Local heating of electronic equipment is not ruled out, which leads to high temperature failure of electronic components. PCB iron base plate can solve this heat dissipation problem. In addition to PCB iron substrate, copper substrate also has a particularly good heat dissipation, but the price is very expensive.
Dimensional stability of PCB iron substrate: Aluminum based printed boards are obviously much more stable than those made of insulating materials. Aluminum based printed boards and aluminum sandwich boards are heated from 30 ℃ to 140~150 ℃, and the size change is 2.5~3.0%.
Thermal expansion of PCB iron base plate: thermal expansion and cold contraction are the common nature of materials, and the thermal expansion coefficients of different materials are different. The aluminum based printed circuit board can effectively solve the heat dissipation problem, so as to ease the thermal expansion and cold contraction of different materials of components on the printed circuit board, and improve the durability and reliability of the whole machine and electronic equipment. In particular, it solves the problem of thermal expansion and cold contraction of SMT (surface mount technology).
Other reasons for PCB iron base plate: PCB iron base plate has shielding effect; Replace brittle ceramic substrate; Use surface mounting technology with confidence; Reduce the real effective area of printed boards; It replaces radiator and other components and improves heat resistance and physical properties of products; Reduce production costs and labor.