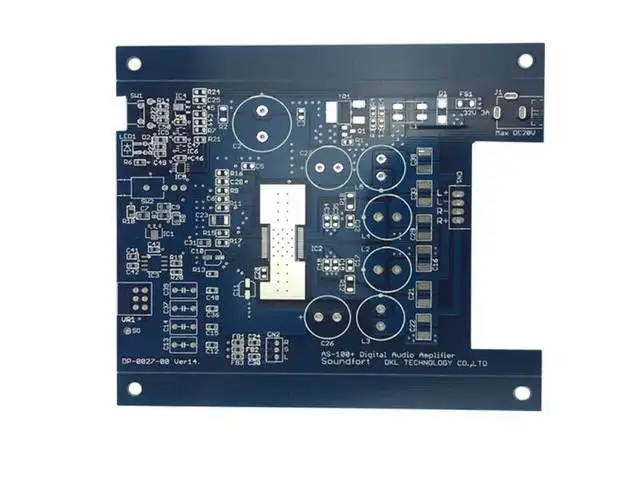
Progress in evaluation and test of three proofing paint
PCB manufacturers, PCB designers and PCBA manufacturers will explain the progress of evaluation and testing of three proofing paint
The purpose of coating the three proofing paint on the circuit board is to protect the printed circuit board and the components installed on the circuit board from the harmful effects of moisture, particles and corrosive gases.
The conventional test method to verify the effectiveness of the three proofing paint is to expose the hardware coated with the three proofing paint to the corrosive environment for several months to determine the average failure time of the three proofing paint. This article introduces a faster test method, which takes less than a week.
This test method uses copper film and silver film coated with three proofing paint, and describes the characteristics of the three proofing paint by the corrosion rate of the film when exposed to hydrogen sulfide gas. This paper describes the design and setting of the test chamber, and observes the influence of temperature and humidity on the corrosion rate of copper and silver films covered by the three proofing paint, and compares them with those of copper and silver films without coating. In this paper, the properties of acrylic acid, silicone resin and atomic layer deposition (ALD) three proofing paint change with temperature and relative humidity. The test temperature is 40 ° C and 50 ° C respectively, and the relative humidity is 15%, 31% and 75% respectively. The temperature will affect the corrosion rate of the copper and silver films covered by the three proofing paint. Relative humidity has little effect on corrosion rate. In this paper, the best conditions for testing the performance of the coatings are discussed according to the obvious differences in the corrosion resistance of the three coatings.
introduction
The purpose of coating the three proofing paint is to protect the printed circuit board and components installed on the circuit board from harmful effects of corrosive environments, which may contain high concentrations of corrosive gases, such as sulfur dioxide, hydrogen sulfide, free sulfur, chlorine, nitrogen oxides and ozone. When the relative humidity in the air is higher than the deliquescence relative humidity of the particulate matter, the particulate matter with low deliquescence relative humidity (DRH) may form a low resistance bridge (electrical short circuit circuit). Once there is a potential difference between the two ends of the bridge, it may cause an electrical short circuit of the circuit board. With the continuous expansion of data centers in the world into areas with high pollution levels and high relative humidity, it is very necessary to use three proofing paint for electronic products, especially for hardware that performs critical tasks and military tasks. Another factor that makes the three proofing paint an indispensable protective layer is the shrinking size of components. With the gap on electronic products getting smaller and smaller, dust particles and particles generated by corrosion may be more likely to form a bridge. Therefore, it is necessary to seriously consider the design of three proofing paint.
The price range of commercial three proofing coatings is large, which is easy to apply and can effectively protect the metal under the coating from corrosion. The standard evaluation method of the three proofing paint industry is to apply the three proofing paint on the actual hardware and determine the average failure time of the three proofing paint applied on the hardware. This testing method is very inconvenient and slow. Even if it is possible to monitor the corrosion status of the components coated with the three proofing paint, such as observing the corrosion status of the resistor on the surface mounted resistor, it may take more than one year to evaluate the coating, and under very limited conditions of temperature, humidity and environmental corrosivity..
A convenient method to evaluate the three proofing paint is to apply the three proofing paint on the copper film and silver film, and monitor the corrosion rate of the metal film coated with the three proofing paint in the corrosive environment and humid environment. The effective three proof paint can well protect the metal under the coating. This paper describes in detail the method we proposed to test the anti-corrosion properties of the three coatings. Our test method tests three different coatings (acrylic, silicone epoxy and ALD coatings) under four temperature and humidity conditions. The environmental bin used in the test is an improved iNEMI sulfur (FoS) bin.
Experimental process and results
The test tool used to evaluate the three proofing paint includes a serpentine copper film or silver film, the thickness of the film is 800 nm, and the coating is splashed at 5 × 15mm silicon oxide wafer. Paste the silicon chip on the prototype printed circuit board (PCB). One end of each of the four L-shaped connector pins is welded to the PCB, and the other end of the pin is connected to the four point contact pads of the serpentine film with silver epoxy resin. The silver epoxy resin we selected must be baked for one hour in flowing nitrogen at 140 ° C. The metal film covered with nitrogen will not be oxidized. The welding end of the L-shaped pin is further connected to a connector which is also welded to the PCB and can receive electrical signals. It is a serpentine film testing tool and a picture of the film settings on the circuit board.
PCB manufacturers, PCB designers and PCBA manufacturers will explain the progress of the evaluation and testing of the three proofing paint.