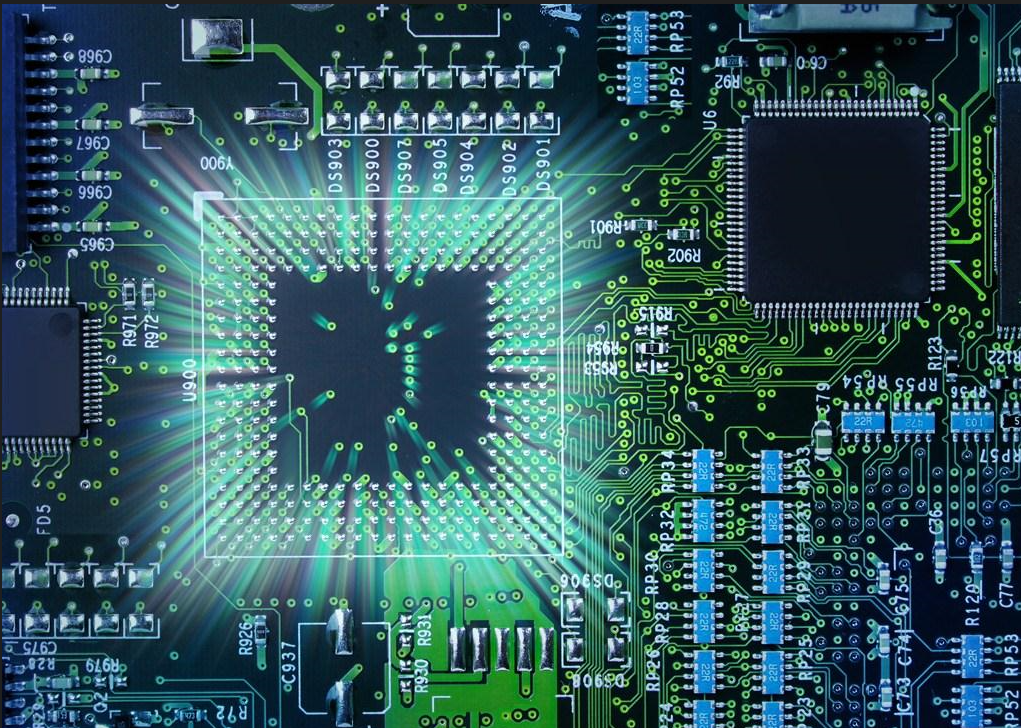
Guidelines for the selection of ideal conformal coatings for PCB
As the world continues to witness the miniaturization of circuits and electronic products, conformal PCB coatings seem to fly higher than before In order to protect PCB from the influence of moisture, extreme temperature, and dust, the manufacturer has adopted conformal coating It is important to choose the best surface type to use
However, it is a difficult task to delete the vast amount of information found on the Internet. But this is no longer the case in this era. In this article, we will provide 12 guidelines to guide you how to select the ideal conformal coating for PCB.
Function of PCB conformal coating
In order to protect electronic components from corrosion and environmental factors, surfaces also play other important roles.
Other functions include being an insulating material for printed circuit boards and minimizing environmental stresses when assembling printed circuit boards. Conformal coatings are also important because they help eliminate the need for complex enclosures.
The conformal coating also protects the printed circuit board from fungus, heat, moisture and air pollutants (such as dust and dirt), thus ensuring the life of the printed circuit board.
Classification and content
There are many options for conformal coating technology, and the best choice depends on the required protection. Reworkability and application method are also important factors to be considered. The following are some typical classifications of conformal coatings:
-Acrylics - They are excellent for providing general protection and moderate elasticity. It also has moderate moisture resistance and dielectric strength.
Circuit board
In addition to producing hard coatings, epoxy resin is also divided into two parts. They have excellent moisture resistance, high chemical resistance and wear resistance.
-Silicone This silicone has average antifungal and moisture-proof properties. It performs well in the high temperature range and is suitable for high vibration tools.
The polyurethane coating has excellent chemical resistance and moisture resistance. In addition, polyurethane has abrasion resistance and solvent resistance.
-Polyethylene terephthalate, a unique surface type for curing applications, provides high vapor deposition. In addition to excellent dielectric strength, this type of cover is also suitable for high temperature applications.
It is well known that UV curable coatings are difficult to repair or rework and can be rapidly produced.
3 anti paint selection principles
To ensure that the PCB has the correct conformal coating material coating, you may need to follow a series of selection principles. This will ensure that you find the best information. The following are the selection principles you should pay attention to:
Single piece is easier to operate
When choosing conformal coatings, you first need to select a unique component. One component conformal coating means that the surface does not need to be mixed before application to maintain composition. Based on the fact that single group delamination provides excellent chemical resistance and moisture resistance, single group delamination is very preferred.
Single coat components are also one of the best paints to use because they are easy to apply and have a long service life. The only major disadvantage of a single ingredient is that it takes a long time to cure to achieve the best care.
Data solidification mechanism
When selecting the type of surface to be used, the curing mechanism is not the main criterion. However, in the long run, it will directly affect the nature of feasible application methods.
Several curing mechanisms are known to be relatively reliable. At the same time, some applications are complex, and there may be multiple application errors, mainly when used in an uncontrolled environment. Some of the most basic healing mechanisms include:
-UV curing is here, and the coating is cured with UV and provides fast delivery. The UV curing layer is challenging to rework and repair.
-Thermal curing This type of curing is used as part of secondary UV curing, evaporative curing, or wet curing. If the curing mechanism cannot meet the required curing characteristics, thermal curing is the ideal choice.
Wet curing This is a curing used with evaporation curing.
– Evaporative curing mechanism, in which the liquid carrier evaporates first, leaving a coating. Although theoretically simple, the PCB may have to be impregnated at least twice to ensure that sufficient layers are formed at the edges of the components.
Long shelf life
The shelf life or product shelf life is the longest recommended shelf life of the product. During this period, the defined quality remains unchanged, as described in the specified display, storage and distribution conditions. You don't want to buy products that will deteriorate after a few days or weeks.
Among other problems that customers often complain about, the short shelf life makes it a series of major problems, especially for customers who like products that can be used for a long time. This is also true when choosing conformal coatings. The shelf life of some coatings is not long, so it is necessary to avoid using them as much as possible. Organic silicon conformal coating 433B is an ideal product, not only because of its faster curing time, but also its longer shelf life.
Wide operating temperature range
As you may know, many PCB designers are squeezing more and more performance from PCB recently. Power density seems to be rising, and high temperatures can also cause serious damage to dielectric and conductors. Some PCBs often work in high temperature environments, such as PCBs for military applications.
When conformal coating is used on PCB, you will be more suitable to withstand the data of various operating temperature ranges. The surface shall be conducted without affecting the function of the circuit board. For example, silicone is one of the best materials that can provide protection over a wide temperature range.
Engineering or performance characteristics
When purchasing PCB conformal coating, its engineering or performance characteristics are the most important. What are its chemical properties? Have you checked whether the surface can withstand dust and moisture? You do not want to use lower than standard layers on a PCB.
Before selecting the type of coating to be used, ensure that it does not cause or cause stress to the component, especially under extreme heat conditions. The surface must be able to withstand the hot spots generated by the component.
Capable of protecting the circuit board from extreme/low temperature and mechanical impact
Single PCB is widely used in high temperature environment, such as military equipment. However, individual PCBs are often exposed to significant mechanical effects. In addition to high mechanical effects, components on the printed circuit board must also be protected from high/low temperatures. To do this, you must purchase conformal coatings with these characteristics.
At high or low temperatures, some types of conformal coatings will fail, affecting the function of the entire circuit board. Cured coatings require abrasion resistance to withstand continuous handling, especially during manufacturing.
Conformal coating shall be cured at high speed without by-products
The conformal coating shall be cured immediately after the dispensing or coating process. When the conformal coating on the printed circuit board is not sticky during processing, the surface is considered to be completely cured.
Sometimes, even if drying takes a long time, it can be cured at average room temperature. Most engineers hope to produce PCB at a high speed to achieve considerable profit margins. The conformal coating selected must be able to cure at high speed without by-products to realize these profits.
Low toxicity and cost
As a PCB manufacturer, nothing is more dangerous than handling toxic substances that may have a negative impact on your health Unfortunately, this is very common in PCB manufacturing Many PCB companies commercially use highly toxic compounds, some of which were banned several years ago To make things worse, some of them use high cost data and pass on manufacturing costs to the end customer
A good conformal coating material, in addition to ensuring its low cost and reasonable price, should also be made of non-toxic materials.
Repairability
The conformal coating you choose to use must be easy to repair or rework. Repairability is an aspect of ensuring weld contact as needed during component placement. For good results, the repair materials you select must be the same as those used in the initial assembly coating.
Verification method and technology
Finally, when choosing the best conformal coating for PCB, you need to ensure that it is validated using methods and technologies. Basic validation and scientific and technological methods include inspection, demonstration, testing and analysis.
Validation will ensure that you avoid errors before starting mass production of PCBs. You need to be sure to check the conformal coating you use and use calculation and test models to prove that it works, tests, and analyzes.
generalization
When choosing conformal coatings for your customers, you need to keep in mind the functional and application requirements of PCB boards It is very important to protect PCB, and you must also ensure that the correct data is used for protection