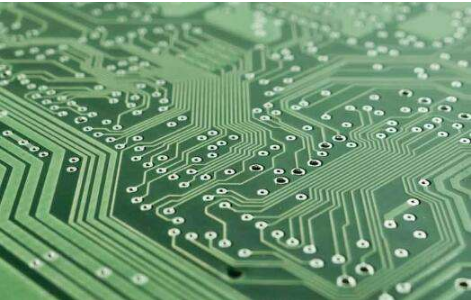
Proofing has a very wide range of applicability, and selecting a high-quality PCB proofing is the ultimate goal of many consumers. However, in addition to selecting a high-quality PCB proofing, the maintenance of PCB proofing in the later stage is more important. But how to maintain PCB proofing?
PCB proofing
PCB proofing maintenance I:
Regular cleaning: After long-term use, there will be some residue and solder accumulation on the PCB proofing circuit board, which will bring unpredictable risks to the solder mask, and even these residues may directly lead to corrosion and pollution risks on the welding surface, which may lead to reliability problems, such as bad solder joints or electrical failures, and increase the probability of PCB proofing failures. And regular cleaning can effectively improve the reliability of PCB proofing in use.
PCB proofing maintenance II:
Strictly control the service life of each surface treatment, and replace the PCB proofing surface processor on time: the most common problems of electronic products also occur in PCB proofing. If the service life of each surface treatment is not strictly controlled, the solderability of PCB proofing may occur due to metallographic changes in the surface treatment of old circuit boards. If the service life is not paid attention, the protective surface of PCB proofing is easily damaged, leading to moisture ingress, which may lead to delamination, inner layer open circuit and other problems in the assembly process or actual use. However, if the service life of surface treatment is paid attention to later, it can effectively improve the solderability of PCB proofing and reduce the risk of moisture intrusion harming other internal systems.
PCB proofing maintenance III:
Use the designated brand and model of strippable blue glue for maintenance: the use of inferior and cheap strippable glue may cause blistering, melting, cracking or solidification like concrete during PCB assembly proofing, so that the strippable glue can not be peeled off or play any role.
How does PCB proofing manufacturer calculate the size of electroplating bath
The relationship between the size of pcb sample plating bath and the average loading capacity, cathode current density, volume current density, etc;
Generally speaking, the size of the plating bath for pcb proofing refers to the volume L of electrolyte in the plating bath, also known as the effective volume, that is, the length X width X depth of electrolyte in the plating bath;
Pcb proofing can generally be calculated and selected according to the processing amount of electroplating or the existing dc electroplating equipment;
PCB proofing
It is very important to select the proper size of electroplating bath for making production plan, estimating production capacity and ensuring electroplating quality;
Three considerations for determining the size of electroplating bath:
1. Meet the dimensional requirements of machined parts;
2. Prevent electrolyte from overheating;
3. It can maintain a certain stability of electrolyte components in the electroplating production cycle;
The current density of the cathode and anode is calculated according to the total area actually immersed in the electrolyte. Because the current efficiency of the cathode and anode is different, there is a slight difference;
DA=I total/S negative (A/dm2)
DA=I total/S positive (A/dm2)
Average load d: electrolyte volume required for electroplating parts per unit area
That is, d=V/S (L/dm2)
Volume current density DV:
Current intensity per unit volume, i.e. DV=ITotal/V (A/L)
It is important and appropriate to control the volume current density in the process of pcb proofing and electroplating, because when the current works through the electrolyte, it will generate heat due to the solution resistance, causing the electrolysis temperature to rise. The speed and height of the electrolyte temperature rise are directly related to the volume current density. In order to prevent the electrolyte from heating up too fast, it is necessary to have more volume of electrolyte to reduce the volume current density;
For example, the acid bright copper plating process: the appropriate volume current density is 0.3-0.4A/L, that is, when the total current is 1000A, 2500-3000L electrolyte should be prepared;
Experience data:
The following data of pcb proofing are some empirical data related to cathode current density and average loading capacity of various common plating species:
Cathode current density range DK, A/dm2 Average loading d, L/dm2
Sulfate copper plating 1.0 --- 3.0 7-9
Acid tin plating 1.0 --- 3.0 7-9
Bright nickel 2.0 --- 4.0 6 --- 8
Nickel oxide 1.0 --- 1.5 6 --- 8
Professional PCB manufacturers and PCB design and solution service providers focus on the development of PCB industry and are trustworthy.