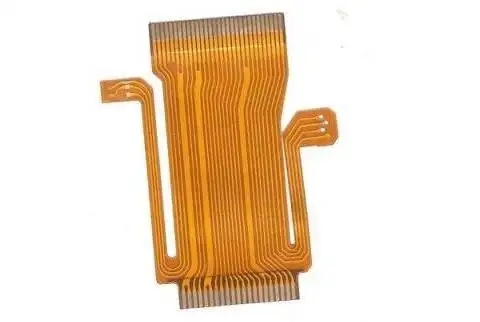
Introduction to peel strength and flexural performance of FPC
Today, FPC is used more and more widely. Then the requirements for FPC are getting higher and higher. From 3-Lay to 2-Lay, their main properties are flexural properties and peel strength.
A) Peel strength of FPC
Peel strength mainly measures the performance of adhesive. Generally speaking, the thicker the adhesive is, the better the peel strength will be, but this is not absolute, because the formula and structure of adhesive from different manufacturers are different. If the molecular structure of adhesive is very small, the bonding area between adhesive and copper foil will increase. So as to improve the adhesion, the peel strength will be improved. At present, the material manufacturers use this method to improve the peel strength and reduce the adhesive thickness.
PCB manufacturers, PCB designers and PCBA processors will explain the peeling strength and flexural performance of FPC
In addition, the blackening process of the copper foil itself and the composition of the blackened layer will also affect the adhesion between the adhesive and the copper foil.
The main components of the blackened layer are: as far as the production process is concerned, the curing degree of the adhesive also directly affects the adhesion. There are three stages in the application of epoxy adhesive in FPC: A, B and C. After mixing in the material factory, when the epoxy adhesive is in the liquid state, the crosslinking degree of the cross polymer is stage A; when the epoxy adhesive is in the semi curing state after coating and baking, the crosslinking degree of the cross polymer is stage B; when the FCCL is in the curing state after curing, the crosslinking degree of the cross polymer is stage C. The coverlay is pressed by the FPC factory into Grade C. When the adhesive is in Grade C, it must be completely cured. If the temperature and pressure during curing or pressing cannot reach the curing temperature and full curing time of epoxy adhesive, its peel strength will be significantly reduced.
B) Flexural performance of FPC
a) First of all, from the perspective of FPC material itself, the following points have an important impact on the flexural performance of FPC.
First, the molecular structure and direction of copper foil (i.e. the type of copper foil)
The bending resistance of calendered copper is obviously better than that of electrolytic copper foil.
Second, the thickness of copper foil
For the same variety, the thinner the copper foil is, the better its folding resistance will be.
III. Type of adhesive used for base material
Generally speaking, the flexibility of epoxy resin adhesive is better than that of acrylic adhesive. Therefore, the choice of high flexible materials is mainly based on epoxy system. And the higher tensile modulus (vs) can improve the flexibility.
IV. Thickness of glue used
The thinner the glue is, the softer the material is. The flexibility of the flexible circuit board can be improved.
V. Insulation substrate
The thinner the insulation base material PI is, the better the flexibility of the material is, which improves the flexibility of FPC. The better the flexibility of FPC is when the PI with low tensile modolos is selected.
The main influence factors of materials on deflection are summarized as two main aspects: the type of materials selected; Thickness of material
b) The influence of FPC's flexibility is analyzed from the process.
First, symmetry of FPC combination
After the substrate is bonded with the covering film, the better the symmetry of the materials on both sides of the copper foil is, the better its flexibility can be. Because the stress is the same when it is flexed.
The thickness of PI on both sides of the circuit board tends to be the same, and the thickness of glue on both sides of the circuit board tends to be the same
II. Control of pressing process
The adhesive shall be completely filled in the middle of the line during coverlay crimping, without layering (section observation). If there is delamination, it is equivalent to bare copper in bending, which will reduce the number of deflections.
In conclusion, to improve the flexural performance and peel strength of FPC, both the material selection and the production process should be considered. For flexure, we hope to choose thinner materials, which are constrained by peel strength and cost. This may be a contradiction in FPC industry. The trend of electronic products is smaller, lighter and more convenient, which makes FPC require more layers, thinner materials and better performance.