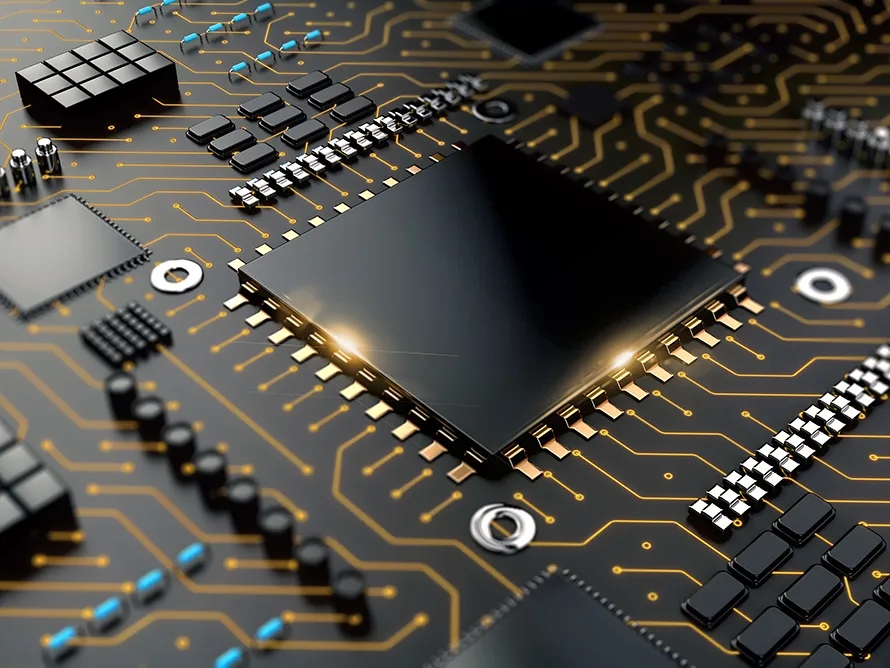
Look, I taught PCB people to write the 8D report required by customers
PCB manufacturers, PCB designers and PCBA manufacturers explain to you and teach PCB people to write 8D reports required by customers
"If it is a human error, how to answer the customer's 8D report? For example, PCB appearance defect, wrong label, quantity shortage, missing processing steps, wrong material issue, etc.
The customer doesn't like us to write rectification measures such as' operation errors, personnel training, quality awareness improvement ', but how can we write them? It's impossible to use error proofing for everything, right?
In fact, first of all, I would also like to say that not only do your customers dislike such 8D reports, but I also don't like people to write about corrective measures, such as "operators have weak quality awareness, strengthen training", "punish the party for 300 yuan", etc. When I was in charge of quality in an enterprise, except for similar problems in my suppliers or internal production engineering, if my SQE or process quality engineer handed me such improvement reports, I would certainly be severely criticized.
Because the responsibility for quality problems is transferred to the operator, either it is irresponsible to deal with it or it is not familiar with quality management. Because in my work experience, most of the operators I met were very simple workers. There are indeed some tricky and slippery people, but few of them. Therefore, all the problems in the above examples can be found out from the management system and methods.
First, let's talk about appearance defects
Generally speaking, appearance defects need 100% visual inspection, which is really easy to cause missing inspection. However, we can still find out the reasons and formulate improvement measures from the following aspects.
——Whether the appearance inspection standards are specific, clear and agreed with customers. The appearance standards of some PCB manufacturers simply write "no flash and burr, no bump". However, during field operation, operators and production management personnel believed that "it is impossible to avoid bumping", so they grasped a vague standard according to their own understanding. The normative approach is to determine the acceptable and unacceptable standards of products one by one according to the possible defects according to the functional aspects. Then it is described clearly in the form of pictures and texts. The standards should be clear, understandable, unambiguous and realistic. Avoid vague "see limit sample for appearance standard". In case of limited samples, there should also be a written description of which aspect and which defect the limited samples are, whether they are defective samples or qualified samples, and the determination conditions of defects and conformity.
——Whether the appearance standards have been clearly and explicitly passed on to the employees. It is prohibited to say that the training is not in place in a general way, and only train the employee on this defect on a case by case basis, while similar things may happen again on another station next time. In case of rectification in terms of employee training, we must find reasons in terms of working methods and process systems from the perspectives of training methods, training processes, post training assessment methods, mutual inspection of new employees at the initial stage of employment, and the accompanying of teachers, so as to prevent similar things from happening next time. For example, for training on appearance defects, in addition to explaining appearance standards or operation instructions to new employees, training should also be carried out in combination with a large number of defect samples, so that new employees can do some defect judgment exercises. At the beginning of the employee's work, the master or quality personnel should be invited to help judge the parts near the standard limit. It is necessary to establish a key position management and replacement personnel training system to prevent new employees from being rushed to work through temporary training.
——Whether the job planning is reasonable. For example, is the illuminance of the light source of the station with appearance inspection requirements appropriate? Is the height of the appearance inspection workbench suitable for workpiece turning and operation observation? Is the sequence of observation operations for employee appearance inspection planned and solidified? That is to say, when an employee inspects the appearance of a part, which faces and which points should his eyes see, and whether the turnover order of the workpiece and the walking path of his eyes are fixed? Can the appearance inspection and production operation be completed within the specified time?
——Are quality warning cards posted for common appearance defects to remind employees to pay special attention?
——Finally, and most importantly, is it necessary to find out the causes at the source and devote to reducing and eliminating appearance defects? For example, for the problem of bumping, will the product transport roller table on the assembly line bump parts? Is there any collision between products? Is the logistics turnover tooling reasonable? Is there a piece stack? Is there any risk of collision during employee operation and workpiece placement?
The second problem is that the labels are incorrectly labeled
The wrong label is also a serious problem for many OEM customers. In some customers, if the label is wrongly pasted twice, it may directly lead to controlled shipment. The wrong label can be improved from the following aspects.
——On site printing, print when you use it, and do not print labels in advance. Generally speaking, the OEM with strict requirements will require the supplier to set a label printer at the packaging station of the production line. If the enterprise has multiple production lines, an independent label printer should be set at the offline packaging station beside each line. Avoid printing a lot of labels in the office. Some enterprises have different products, or different batches. They like to print a stack of labels in the office, and then take a stack of labels to the production line. When packaging, they look for a stack of labels and paste them. Or after packaging, many packing cases are stacked together and then labeled together. Some enterprises even put them for a few days after packaging and then stick labels before shipping. These incorrect practices are not normal unless there are problems.
——If the customer does not have a clear requirement for an independent printer, and the enterprise cannot achieve an independent label printer for the time being, it can also adopt a type change error proofing method to ensure that the label is correct. In the future, I will write a separate article about the error proofing method of the replacement. To put it simply, when multiple products are produced in the same line, raw materials, finished products, semi-finished products, tooling, tools, accessories, various operation instructions, various record sheets, packaging materials, including the programs and process parameters called in the equipment, and of course, labels, are switched to the products with the same model when they are ready to switch to process a certain type of product. In case of inconsistency, ensure to evacuate from the production line and within the range available to the operator or cover it. This makes it impossible to take and use the wrong product, which is called type change error proofing. During the type change, the operator checked and recorded the switching of all software and hardware by using the Type Change Mistake Prevention Spot Check Form, and the team leader checked each other.
Third, quantity shortage
I also don't agree to increase mutual inspection of personnel, because the efficiency is very low. In addition to using counters, improvements can also be considered from the following perspectives:
——If the products are regular, they should be placed neatly. A packing box or a material box is fixed in several rows and several layers. In this way, the spot inspection quantity is converted into a visual inspection of the arrangement shape, and the quantity confirmation becomes very intuitive.
——If there are requirements for collision protection and extrusion at the same time, consider customizing molded blister boxes or boxes with partition plates to place products, one radish for one pit. The pit is not full, and the parts are missing, but the quantity is not enough.
——Weighing method. However, when the number of parts is large and the weight of each part fluctuates within a certain range, it may lead to inaccurate weighing. At this time, you can consider setting up a number of small packages in large packages, and the number of small packages should consider that the sigma of the total weight fluctuation range is less than one sixth of the weight of a part.
Fourth, missed processing
In addition to setting up continuous production lines and error proofing, the following aspects can also be considered for improvement:
——Self inspection and mutual inspection are added. Before the release of each process, the operator shall inspect whether the processing content of this process is completed by himself, and release or put into the material rack box after inspection. The next sequence shall check whether the processing or assembly content of the previous sequence is completed before processing.
——Fixed location management and positioning storage. If it is a single machine operation, the parts to be processed and the processed parts at each single machine station must be placed separately and fixedly. Generally, the left hand side is the part to be processed, and the right hand side is the processed part. It is strictly prohibited to mix and place the processed parts in the same rack or box. In the in-process turnover area, the in-process products of the bin should also be placed in different process states and clearly marked.
——Hang the process travel card. For the production line with single machine operation, the material rack or material car shall be hung with the accompanying card, and the process status shall be marked on the accompanying card.
Fifth, wrong materials
The most common mistake is that two different models of products are mixed into a large package of most correct products. It is generally caused by the following reasons. If these aspects are eliminated, the problem of mixing materials is basically eliminated.
——For this problem, the basic reason is that the error proofing of the replacement is not done well. There are different types of finished products and in-process products at the production station and on the production line.
——Or in the packaging area and the inspection area, different types of products exist at the same time, and they are scattered and mixed. Therefore, fixed location management and 5S are the most basic requirements, not simple, clean and tidy.
In addition to the above problems, another reason that is often used by suppliers is that "commissioning parts are mixed in qualified parts for submission". This is also a statement that I and many SQEs from OEMs hate. We often ask, how do you know which one is the debug one? Is there a traceability number on the part? Does the inspection record of commissioning parts correspond to the traceability number? Even if it is true that commissioning parts are mixed with qualified products, the enterprise also needs to analyze and improve the causes of management methods in the aspects of fixed placement and identification of nonconforming products, fixed placement and identification of commissioning products, pre startup inspection and confirmation, and first article confirmation. It is not simply attributed to operational errors. PCB manufacturers, PCB designers and PCBA manufacturers explain to you and teach PCB people to write 8D reports required by customers.