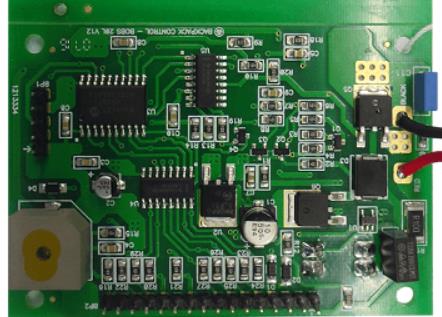
Solution to Material Dispersal in PCBA Production
PCBA manufacturing is an indispensable step in the process of electronic equipment design and production The PCB carries the control system of electronic equipment Its quality directly affects the operation of electronic equipment and product quality Good products are inseparable from high-quality PCBA manufacturing and PCB support In PCBA manufacturing, we will inevitably encounter some problems
PCBA manufacturing
Today, kingford will explain one of the PCBA manufacturing solutions: the cause and solution of throwing
Cause 1: nozzle problems, such as nozzle deformation, blockage, damage caused by insufficient air pressure, air leakage, inability to pick up suction, improper selection of data, failure to pass identification but thrown by PCBA.
Countermeasures: Clean and replace the nozzle;
Cause 2: Feeder failure or defect caused by feeder problem, incorrect feeder setting, distorted position, poor feeder mechanism, and PCBA throwing.
Countermeasures: reset the feeder, clean the equipment, calibrate or replace the feeder.
Cause 3: identification system problem, poor vision, unclean vision or laser lens, foreign matter interference identification, improper selection of identification light source or insufficient intensity and gray scale, or possible poor identification system.
Countermeasures: Clean and wipe the surface of the identification system, keep it clean, free of foreign matters and oil contamination, adjust the intensity and gray scale of the light source, and replace the identification system components;
Cause 4: position problem, position deviation, the nozzle is not in the data center when sucking, and the data height is incorrect (usually 0.05 mm after contacting the parts), resulting in deviation, incorrect data, and deviation. When it does not match the corresponding data parameters, the identification system will discard it as invalid data.
Countermeasures: Adjust the feeding position, height and other parameters;
Cause 5: Vacuum problem, insufficient air pressure, insufficient vacuum gas pipe channel, foreign matter blocking the vacuum pipe, or insufficient air pressure caused by vacuum leakage, which makes it impossible to pick up data or fall off during pasting.
Countermeasures: Adjust the pressure value at the air pressure steep slope according to the equipment requirements (generally 0.5~0.6MPa for the chip mounter), clean the ventilation pressure pipe, and repair the air leakage channel;
Cause 6: The program problem of the slicer, the incorrect parameter setting of the component in the program being edited, and the inconsistency with the data size, incoming brightness and other parameters led to the identification failure and discard.
Countermeasures: Modify the element parameters and find the best parameter value of the element;
Cause 7: Nonconforming products such as problems with incoming materials, non-standard incoming materials or oxidation of incoming pins.
Countermeasures: IQC shall do a good job in incoming material inspection and contact parts suppliers;
Cause 8: Feeder failure, feeder deformation, feeder feeding defects (feeder ratchet gear damage, feeder ratchet gear belt without holes, foreign matters under the feeder, aging spring, insufficient force or poor power), resulting in failure or poor feeding, PCBA throwing, and feeder damage.
Countermeasures: correct the feeder, clean the feeder platform, and replace damaged parts or feeder;
pcba
According to relevant research, static electricity is also the cause of PCBA falling. This placement machine should be grounded and anti-static work should be done at the production site.
It is normal for the placement machine to throw PCBA, but if the high throw rate of PCBA seriously affects the production efficiency and production cost, it must be solved. In case of serious PCBA throwing, you can ask the on-site personnel first, and then observe and analyze according to the above seven reasons to find out the problem directly, so as to find out the reason more effectively and solve the problem. While improving the production efficiency, it takes up too much machine production time.