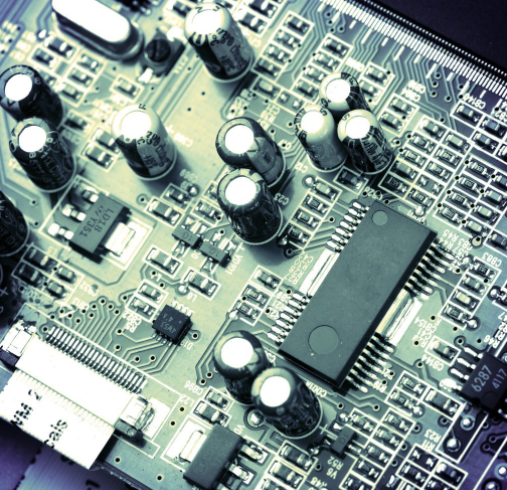
Main equipment required for SMT production
The full name of surface mount technology is surface mount technology, which means surface mount technology SMT equipment refers to the machines and equipment used in SMT workshop chip processing and production Different PCB manufacturers will include different SMT production lines, scales and customer needs according to their own strength The SMT production line can be divided into semi-automatic SMT production line and full-automatic SMT production line. However, the machines and equipment of each SMT workshop production line are roughly the same, but the following SMT workshop equipment is a relatively complete and rich SMT production line The specific ten process steps are as follows:
Surface mount
1. Board loader: PCB circuit boards are automatically transferred to the board suction machine after being placed in the rack;
2. Board suction machine: PCB board is sucked and then automatically transferred to the solder paste printer;
3. Solder paste printer: accurately leak solder paste or paster on the bonding pad of PCB to prepare for component installation. Printers used for SMT technology equipment are generally divided into three types: manual printers, semi-automatic printers and full-automatic printers;
4. SPI: SPI is the abbreviation of solder paste inspection, which is called solder paste inspection machine in Chinese. It is mainly used to detect the quality of the printed circuit board of the solder paste printer, and detect the thickness, flatness, printing area and other functions of the solder paste printing;
5. SMT mounter: use the program prepared by SMT technicians before operation to accurately install the components to the fixed position of the PCB. The mounter can be divided into high-speed mounter and multi-function mounter. High speed mounters are generally used to install small chip components, while multi-function general-purpose mounters are mainly used to install rolls, magnetic or tubular large components or heterosexual components. Their characteristics are high installation accuracy, but the installation speed cannot reach the effect of high-speed mounters;
6. Docking station: equipment used to transmit PCB;
7. Reflow soldering: It is equipped on the back of the SMT machine on the SMT production line to provide a heating environment to melt the solder paste on the bonding pad, so that surface mounted components and PCB bonding pads can be firmly fused together through the solder paste alloy.
8. Discharger: PCBA is automatically collected through the transfer track.
9. AOI inspection: automatic optical identification and inspection system is the abbreviation of English (auto optical inspection). It is called automatic optical testing instrument in China At present, it has been widely used in the appearance inspection of circuit board assembly line in the electronic industry, replacing the previous manual visual inspection During automatic detection, the machine automatically scans PCBA through the camera, collects images, compares the tested solder joints with the qualified parameter values in the database, checks the defective PCBA boards through image processing, and marks the defective PCBA boards on the display screen for the maintenance personnel to further repair the defective circuit boards
10. X-ray: mainly used to detect the internal installation quality of various industrial components, electronic components and circuits.