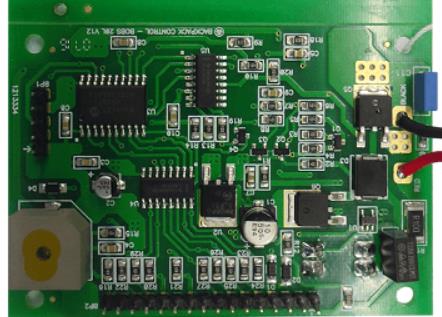
How to prevent warping and deformation during PCBA production?
Everyone knows that PCB warping has a great impact on the production of PCBs Warpage is also one of the important problems in the production process When PCB boards are equipped with components, they will bend and the bottom of the components is difficult to be neat Polychlorinated biphenyls cannot be installed on the host shell or socket inside the machine, so the warping of polychlorinated biphenyls will affect the normal operation of the whole subsequent process
Now PCBs have entered the era of surface mounting and chip mounting. Surface mount technology requires higher and higher warpage of printed circuit boards, so we need to find out the causes of warpage and deformation of printed circuit boards.
1. PCB engineering design:
Precautions shall be recorded in PCB design:
(1) The arrangement of prepreg between layers should be symmetrical, for example, the thickness of six layers of PCB, 1-2 layers and 5-6 layers and the amount of tension of prepreg should be the same, otherwise the PCB is easy to warp after lamination;
(2) Multilayer core board and semi solidified board shall be manufactured by the same supplier;
(3) The graphic area of the outer A and B surfaces should be as close as possible. If the A side is large copper and the B side is only a few lines, the PCB is easy to warp after etching. If the area of PCB lines on both sides is too large, you can add a separate grid on the sparse side to balance them.
2. PCB baking board PCB factory before discharging:
The purpose of baking the copper clad board before cutting (150 degrees C, 8+2 hours) is to remove water from the PCB board, while fully curing the PCB board to further eliminate the PCB board, which helps prevent the PCB board from warping
At present, many double-sided and multilayer PCB boards still adhere to the baking step before or after cutting, but there are some exceptions in the board factory. At present, the baking time of SMT process equipment in PCB factory is also inconsistent, ranging from 4-10 hours. It is recommended to decide according to the grade of PCB produced and the customer's requirements for warpage. It is suggested that the cut baking board or inner baking board should also be baked.
Polychlorinated biphenyl manufacturing
3. Longitude and latitude of semi cured plate:
After lamination, the longitudinal and transverse shrinkage of the semi cured plate are different. When cutting and layering, it is necessary to distinguish between transverse and longitudinal directions. Otherwise, even if the pressed baking board is difficult to correct, it is easy to cause PCB warping after lamination; Many reasons for warpage of multilayer printed circuit boards are due to the lack of longitude and latitude separation in the laminating process, which leads to the overlapping of semi cured boards.
How do you distinguish longitude from latitude? The rolled semi solidified plate is rolled up along the latitude and width direction. For copper foil, the long side has longitude and latitude, and the short side has direction. If you are not sure, you can ask the manufacturer or supplier.
4. Stress relief after PCB lamination:
After hot pressing and cold pressing, remove the PCB multilayer board, trim or mill the bristles, and then lay it flat in an oven at 150 ℃ for 4 hours to gradually release the stress in the PCB board and completely cure the resin. This step cannot be omitted.
5. PCB electroplating needs to be straightened:
When 0.4-0.6mm ultra-thin PCB multilayer boards are used for surface electroplating and graphic electroplating, special rollers shall be made. After the thin plate is clamped on the flying rod on the automatic electroplating line, use the round rod to string the rollers on the whole flying rod together, pull all PCB boards on the rollers, so that the plated PCB boards will not be deformed.
Without this measure, after electroplating 20 to 30 micron copper layer, the plate will be bent and difficult to repair.
6. PCB cooling after hot air leveling:
During the hot air conditioning process, the printed circuit board is impacted by the high temperature of the welding groove (about 250 ℃). After removal, it shall be naturally cooled on flat marble or steel plate and cleaned in the post-processing unit. This is beneficial to the warping prevention of PCB. In some PCB factories, in order to improve the brightness of lead and tin surfaces, PCB boards are put into cold water immediately after hot air leveling, and then taken out for post-treatment after a few seconds. This cold and hot shock may cause some types of PCB boards to warp, delaminate or bubble. In addition, air floating bed can be added to SMT technology equipment for cooling.
7. Treatment of warped PCBs:
For well managed PCBs manufacturer, PCBs will undergo a 100% uniformity check during the final inspection Any PCBs that fail will be selected and placed in an oven, baked at 150 ℃ and high pressure for 3-6 hours, and cooled naturally under high pressure Then remove PCBs and check their flatness This will save some PCBs Some PCBs need to be baked two or three times to flatten If the warpage prevention process measures are not implemented for the PCBs mentioned above, and some PCBs are useless for baking, the PCBs manufacturer can only scrap the PCBs