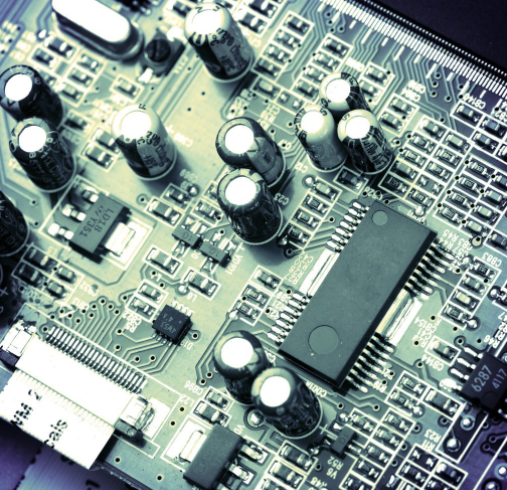
Guide to Authoritative Issues of Industrial PCBA
The structural industrial PCB is much more complex, and the application occasions are much more complex than ordinary PCB
Industrial PCB needs professional designers, skilled workers, high-quality industrial equipment and excellent manufacturers.
These PCBs are manufactured for long-term use. In this case, the data it uses is more durable than the data used in ordinary PCBs.
Industrial printed circuit boards must be manufactured with great care to have multiple specifications.
Due to the complex manufacturing process of industrial PCB, not all PCB manufacturers can manufacture industrial PCB.
Therefore, it is very important to find a suitable manufacturer for PCB design
The use of robotics and automation in industrial operations is increasing.
Industrial PCB is widely used in power control system, industrial intelligent instrument meter, industrial lighting system and other fields.
Industrial PCB is designed for long-term use. These cannot be replaced as often as ordinary PCBs.
In other words, we must pay attention to quality, reliability and efficiency in manufacturing.
Circuit board
The main reason is that all companies want to reduce labor costs and strive to improve accuracy and efficiency.
PCB is an important factor in robot technology and automation. This kind of PCB must have industrial reliability, precision and flexibility.
Polychlorinated biphenyls used in the industrial sector must be flexible, durable and adaptable to harsh conditions. Now we will discuss some key points about industrial PCB.
What is an industrial PCB?
In short, PCB used in the industrial field is called industrial PCB.
High profile PCBs are used in various industrial applications.
These are called industrial PCBs. Like other PCBs, industrial PCBs have multiple layers, and each conductive layer is separated by insulating materials.
The insulating material is usually made of glass fiber, plastic or ceramics.
The standard of PCB data is PIC2221A.
All types of PCBs must comply with this standard.
If the designer wants to use a power conversion device, IPC9592 recommends using other parameters.
Many of the cutting-edge technologies we see today rely heavily on PCBs. Industrial PCB has made contributions to automation in many industries.
Thanks to the industrial PCB, the mechanical arms used in various product manufacturing cells can work smoothly and accurately. Now we will learn more about industrial PCB.
Industrial PCB composition:
Many types of information are used to manufacture industrial PCBs.
Here, layers of different materials are bonded together by adhesives under extreme high temperature and pressure. The side view of the PCB looks like a layered cake.
Now let's analyze each layer of PCB.
Our main goal is to analyze what data each layer consists of and what its functions are.
basal:
The data used for making PCB base layer is called PCB base layer data This primer is often referred to as the substrate
It is usually made of fiberglass material. Almost all types of PCBs use FR4 glass fiber. Because it is difficult in essence.
The reason for using this hard material on the PCB substrate is that the substrate strengthens other layers of the PCB.
For flexible PCB, the base plate is flexible. The substrate is usually made of flexible plastic.
PCB thickness ranges from 0.6mm to 1.6mm. However, other information can also be used for the manufacture of PCBs.
However, other information can also be used for the manufacture of PCBs. As epoxy resin and phenolic resin, they are used in many polychlorinated biphenyls.
One thing we need to remember is that the substrate needs to be hard enough so that PCB can be used in industry.
This is why fiberglass is most useful in all these situations.
Copper layer:
After the bottom layer, the most important layer is the copper layer.
The copper layer plays an important role in maintaining PCB activity.
Under extreme high temperature and pressure, the copper layer is laminated to the base layer with adhesive.
In the case of double-layer and multilayer PCBs, copper layers are arranged on both sides of the layer.
Industrial PCBs usually do not use copper layers because all these PCBs have many complex tasks to perform.
The thickness of the copper layer varies depending on the PCB. Due to the high power of industrial PCB, its thickness is 2-3 ounces.
This means that in all these cases, the thickness of the copper layer is 35um.
The copper layer is the main conductive layer of PCB, that is, various works are carried out here.
To print the required circuit pattern on the substrate, two methods can be used.
One is addition, the other is subtraction.
In the addition method, copper will be coated on the substrate surface according to the pattern we need, while the remaining areas will remain uncoated. Most consumer printed circuit boards are printed in this way.
In subtraction, it is necessary to cover the entire substrate surface with copper first, and then remove unnecessary areas according to the design, that is, remove the coating materials in these areas.
Welding mask:
The most important layer after the copper layer is the solder mask. The green color we see on PCB is due to this soldering mask.
This is the top layer of copper. Protect all traces, paths, and components of the PCB from any external conductive material.
It can also act as a mask during welding, so short circuit will not occur. In short, it can protect PCB from any unnecessary external connection.
Silk Print:
A wire mesh layer is used at the top of the solder mask. It helps to mark the names, values, positions and pin configurations of various components on a PCB.
It is very important to mark all these important things with screen printing. This is because all this information helps to place the assembly in a short time and in a perfect pipe when assembling the PCB. In addition, if any PCB board is damaged, the wire mesh of this brand can help to replace specific components.
Layer based industrial PCB type:
PCB manufacturing is usually much more difficult than PCB design. Over time, designers try to find out how to design a single circuit by integrating multiple circuits on the same platform.
With the innovation of new technology, PCB manufacturers face more and more challenges