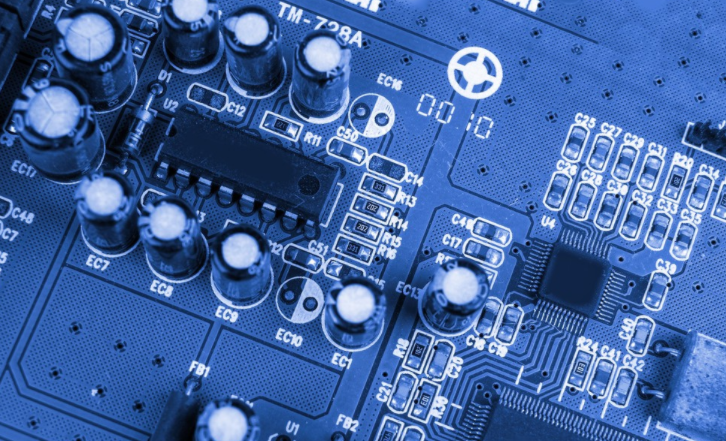
Perfect optical inspection of conformal coating on SMT patch
In some applications, conformal coating is necessary. SMT chip processing equipment is used to protect printed circuit boards from physical impact and moisture corrosion in harsh environments, which may lead to product failure
If conformal coating is not applied properly, long-term reliability of SMT products may be affected For example, the coating defects in the manufacturing process of automobile electronic modules will threaten the safety of passengers Even in today's era of highly automated manufacturing processes, many companies are still manually inspecting conformal coatings In this case, human error may occur depending on operator proficiency and fatigue factors Reducing such human errors and improving the quality and repeatability of the inspection process are the functions of the fully automatic conformal coating inspection machine
The key of conformal coating defect detection is the illumination of the coating. This is achieved by adding tracer data to the coating, which emits light when exposed to ultraviolet light sources. PARMI's PCI 100 lighting system (1) uses ultraviolet LED lighting to obtain inspection images of conformal coatings, and bubble detection (2) uses white LED lighting for teaching and reference mark identification.
Circuit board
PARMI uses a very innovative synchronous image acquisition technology to scan the ultraviolet LED and white LED in a single time, so the inspection time is fast Scan the coated sample and then the printed circuit board. The SMT chip processing factory just needs to click the magic wand button, and the programmer can define the coated and non coated (reserved) areas on the printed circuit board The PCI 100 of PARMI can check the following characteristics of the coating: PCB s: coating presence, coating missing (reserved), overspray/pollution, bubbles, and the coating thickness can be measured at the specified position
As mobile devices and wearables become smaller and thinner, the coating thickness must be strictly controlled. The coating must be thick enough to protect the components and thin enough to carry and minimize the consumption of coating materials. To meet the coating thickness standard, you can choose to add the CTS I (coating thickness sensor) of PARMI to the PCI 100 machine. The laser module in the PCI 100 sensor head first finds the height of the measurement target on the printed circuit board, and then adjusts the Z-axis to the precise focus before thickness measurement, which improves the measurement reliability of the thickness sensor. Coating
PARMI's PCI 100 DSI (double sided inspection) can inspect the top and bottom of the PCB in one continuous operation by turning the inside of the PCB machine It maximizes productivity by minimizing unnecessary processes and shortening cycles The SMT placement plant also minimizes the required footprint by eliminating the need for external circuit board tilters
The perfect optical inspection of conformal coating in SMT wafer processing plant is introduced above