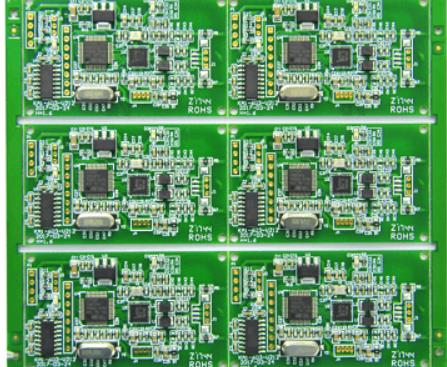
SMT element placement accuracy and machine function
Use CAD tools to ensure PCBA components
There are many utilities in PCB design CAD tools, which can help designers accurately place component schematics on the circuit board
Library tool: The importance of creating precise components in CAD tools occupies space, but this step cannot be overemphasized. In short, the space occupied by bad components will not only lead to unexpected manufacturing problems, but also may lead to part placement problems if the distance between components is too close or too far. This, if possible, please use the automatic part generator and wizard. These tools are usually based on IPC specifications and will bring you heavy part creation work. Another good resource is the use of online library services, which usually have complete design tool resources that you can use.
Design rules: These frequently underutilized functions may be of great help to PCB designers. They can not only set basic gaps, such as the spacing between pads, but also usually have advanced functions. These can include defining different gap values for component groups, areas, and sides of the board. In addition, make sure to use the cross detection function of the design tool so that components can be placed in the correct order according to the signal path defined in the schematic diagram.
Circuit board
Placement: Many tools have utilities that allow you to automatically perform many component placement tasks, such as part alignment or copy placement mode. These features can save you a lot of time and effort, and you should use them as much as possible.
3D: By using STEP models, many PCB design systems allow you to view the design as a full 3D pipe. Although the layout tool has the function of checking the clearance conflicts on the X axis, Y axis and Z axis, it is very useful for designers to be able to see them when actually assembling parts. For example, design rules may allow for manufacturing gaps between parts, but 3D allows you to see if there is enough space to insert connectors or manually rework parts.
In addition, PCB designers should ensure that components are placed in accordance with the electrical, thermal, mechanical, and manufacturing specifications of the circuit board. Here, it is useful to use schematic diagrams as a roadmap for component placement, just as it is to use various analysis tools to verify the accuracy of final placement. Another useful technique is to fully understand the component placement rules before the layout starts, and this information can be obtained from the PCB contract manufacturer.
Functions of the chip mounter
As we all know, when using the mounter, we also need to maintain it. So why should we keep it? How to maintain? Let's understand according to SMT placement equipment:
1. Clean and lubricate the movable part of the support. During the long-term operation of the machine, due to improper environment, a large amount of dust will adhere to moving parts (such as screws, guide rails, sliding blocks, drive belts, motor couplings, etc.). The purpose of maintenance is to prevent the SMT machine from being maintained and cleaned timely and professionally. If the machine is overloaded for a long time, it will inevitably affect the service life of the machine.
2. Clean and remove the dust and scale on the surface of the mounter and the circuit board of the mounter. The purpose of maintenance is to prevent the poor heat dissipation inside the machine caused by dust and scale, which will lead to overheating and burning of power components;
3. Chip mounter maintenance can effectively reduce chip transfer rate, reduce alarm times, improve production efficiency and improve production quality
4. Disassemble and clean the internal air circuit, solenoid valve, vacuum generator, cylinder, etc. of the mounter; The purpose of maintenance is to prevent the oil in the gas path from blocking the gas path and causing high-capacity components if it cannot be cleaned and maintained in time; In serious cases, the oil accumulated in the air circuit will corrode the internal sealing rings and components, such as solenoid valves, vacuum generators, cylinders, etc., causing damage to components and seriously affecting the normal use of the machine;
5. After the warranty period and long-term operation, how to conduct comprehensive and professional maintenance on the mounter? There are hidden dangers in some parts of the machine (such as: wear of machine circuit, wear of cable rack, looseness of motor fixing screws and screws, failure of some mechanical parts, incorrect parameter setting, etc.). The purpose of such maintenance is to avoid potential hazards, which will inevitably pose a threat to the normal production of the machine. Therefore, it is necessary to carry out large-scale maintenance on the machine, timely check and find out the hidden dangers inside the machine, and solve them.
6. After a long time of operation, the relevant parts of the machine will be worn, deformed, and deviated from those of the elderly The original parameters of the placement machine have not yet adapted to the current machine state, which affects the installation accuracy of the machine Therefore, the purpose of maintenance is to calibrate the machine regularly, so that the machine can be produced with high precision and improve the product quality of PCBA products