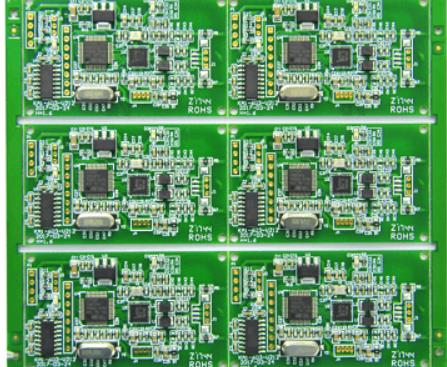
SMT mounting equipment and AOI automatic optical instruments
SMTequipment is actually the machine needed for surface mount technology Generally, the whole SMT production line usually includes the following equipment:
Loading machine, printing machine, connection station, SPI, mounting machine, plug-in program machine, reflow soldering, wave soldering, AOI, X-ray, loading machine and other equipment. The above equipment is a relatively complete smt wiring list equipment, and different manufacturers can add or delete relevant equipment according to the actual product needs. The necessary equipment includes printer, mounter and reflow soldering.
SMT is an abbreviation for Surface Mount Technology. Further reading: What is SMT? What does smt do? What does the smt patch mean?
Translated into Chinese is surface mount technology. Through this technology, the internal circuit boards of various digital household appliances and other electronic products common in daily life are realized. The electronic components are installed on the circuit board through the mounter in the smt device. After welding in the reflow furnace, it will eventually become the main board. Surface mount technology plays a huge role in today's electronic industry. Let me introduce what the SMT device contains.
Circuit board
Smt device
SMT production equipment: distributor, solder paste printer, mounter, reflow soldering, wave soldering
SMT test equipment: SPI solder paste thickness tester, furnace temperature curve tester, AOI optical tester, ICT online tester, X-ray test system, ATE test system
SMT peripheral equipment:
Solder paste mixer, connecting platform, slitter, loader, loader, buffer
SMT accessories: thermocouple/thermal resistance, heating tube, scraper/template, nozzle, dispensing needle, dispensing machine barrel accessories, wave soldering gun tube, feeder
SMT welding consumables: solder paste/solder strip, patch adhesive, flux
SMT electric tools: anti-static soldering iron, soldering iron, tin melting furnace, chip retention pliers, foaming furnace
SMT cleaning equipment: ultrasonic cleaning machine, PCBA cleaning machine
Anti static products: anti-static human body protection, anti-static tools, anti-static turnover boxes, anti-static packaging, anti-static testing instruments.
Testing method and process of AOI automatic optical instrument
The full name of AOI (Automatic Optical Inspection) is automatic optical inspection, which is based on optical principles to detect common defects encountered in welding production, such as online monitoring and inspection of PCBA boards (PCBA is the abbreviation of printed circuit board+assembly in English), that is, the entire production process of empty PCB boards loaded through SMT and then through DIP parts is called PCBA boards).
More and more factories are equipped with AOI test equipment to ensure product quality. The basic principle is to use light reflection to check whether BGA and other components are placed correctly, whether the welding is good, and whether there are defects such as missing, inversion or short circuit. When defects are found through AOI inspection, field staff are required to make visual judgment. After the products are determined, manually modify the test results to be qualified, continue the subsequent production, and repair the defective products.
However, when SMT is bad in the second half of the echo, it occasionally finds more direct bad parts, such as missing parts, reverse parts and wrong parts. These defects were reported in the AOI test, but the field operator misjudged these defects, and they flowed into subsequent production.
Elements of AOI technology realization:
The technical problem to be solved by the invention is to provide an AOI detection method, which can reduce the probability of misjudgment of field operators and greatly improve the product quality.
To achieve the above purpose, use the AOI detection method executed by the AOI detection equipment to detect the PCBA board to be tested, which includes the following steps:
a. Start the AOI inspection program to check the components on the PCBA board to be tested to obtain inspection data;
b. Determine whether the detected data exceeds the preset first threshold. If yes, execute step c, otherwise, execute step f;
c. Determine whether the detection data of the PCBA board to be tested is greater than the preset second threshold. If it is greater than, go to step d, otherwise go to step e;
d. Confirm that the PCBA board to be tested is unqualified, and store the test results of the PCBA board to be tested;
E. Storing test results PCBA board to be tested according to the input information of the on site operator; and
f. Confirm that the PCBA board to be tested is a qualified product, and store the test results of the PCBA board to be tested.