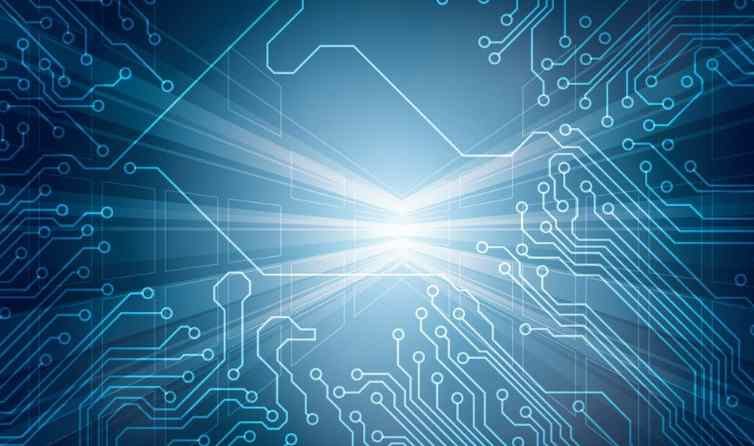
The consumer electronics market has been under pressure to greatly reduce the time to market for new products, as intense competition and continued innovation result in very short product lifecycles compared to other technology-based industries. There is a short window of time to launch innovative products and realize sales revenue before competitors produce cheaper alternatives and saturate the market. Development times must be as short as possible, so these competitors have little warning that new products will appear that they need to analyze, understand, and copy to make this window larger.
PCB development
Typical consumer electronics devices are relatively complex, crammed with features in as little space as possible. Complexity requires collaboration between subject matter experts for each functional block of the overall design. This design process must be trouble-free to meet the short development times required for rapid time-to-market. All design elements had to fit together seamlessly the first time because there was little time to fix incompatibilities or interface breaks. A complete, correct and coherent data set accessible to all collaborators is the foundation of this "one hit" philosophy.
The end result of the PCB design process is the data used to convey the manufacturing and assembly information needed for the prototyping or production process. Tracking, pad and hole layout, screen covering, solder resistance layer -- all of this information is necessary for PCB manufacture. With multilayer panels, the amount of data can be large and the impact of the slightest error is critical. For example, a single pad or drill with slightly wrong coordinates can render a manufactured circuit board unusable.
risk
Any errors in the design data set will translate directly into product problems. At best, a function may be slightly out of specification; In the worst case, the product may not work. Design errors can come from component data table information. For example, manufacturer data may be incorrect, or it may be incorrectly transcribed into the design data set. Therefore, all manufacturer data should be checked at source. Experienced designers will find obvious errors, but more subtle errors can only be found by comparing them with other vendors' data sheets.
Design errors can come from multiple versions of the same component in the design data set, where collaborating teams may use different data for the same component. Therefore, the data set should be structured to avoid duplication or to prevent old data from being retained when component data is modified.
When dynamic data affects the design process, design errors can occur, and different teams access and utilize the data at other times, so different values are used. Therefore, the presence of dynamic data must be obvious, and processes must be in place to ensure that changes do not adversely affect static design decisions.
Manufacturing errors can result from corruption of design data during transmission to the production process due to incompatibilities or process errors. If it is not obvious, no error can be detected until the first production product is tested.
Manufacturing errors can come from physical component size errors, such as pin spacing or leg diameter, that prevent the assembly of the affected component. Operational errors may result from errors in track spacing or width that were not detected during the design simulation, but through electromagnetic interference, current losses, or excessive temperatures in the operating environment.
PCB data complexity
As the complexity and variety of components continue to expand to meet market demands, the complexity of PCB data increases year by year. As a result, the resources necessary to maintain a coherent library of complex data force people to turn to automated processes and third-party services. Monitoring component data tables for changes would be a full-time task, not to mention validating data and monitoring duplicate or stale data.
PCB data integration
The electronic design process is built around computer-based solutions, from schematic capture to circuit simulation, PCB circuit layout, to computer-aided design. This joint approach requires that the PCB design data set be compatible with the design tool. The adoption of product lifecycle management solutions further extends compatibility requirements to a range of new business management tools.
Component procurement
A key part of the design process is to ensure that the selected components are available at an acceptable price and the required delivery cycle to support the project timeline. Therefore, the PCB data set will include dynamic availability and cost data to support project management activities. Ideally, a data management solution should support the analysis of components in use and the identification of alternative supply sources through price monitoring so that you can switch to lower-cost options when available. The same function should also inform the production process if a supply problem occurs that could hinder manufacturing.
Key requirement
PCB data must be available to everyone who needs it when needed. In addition, it must be error-free, and everyone accessing the data set must see the exact same data. Achieving these requirements by creating centralized resources sounds easy, but with large data sets of complex data, it can be a management challenge. Redundancy controls are necessary to ensure that a single failure does not prevent the design team from accessing the data, effectively bringing the design process to an abrupt halt. A local copy of a central resource sounds like a simple solution. Nonetheless, it creates huge problems in ensuring that local data is maintained and consistent across geographically dispersed collaborating teams.
Security controls are needed to prevent data from being accidentally or maliciously destroyed or deleted, dropping a wrench in the design process. In addition, by designing the team to remotely access the centralized solution, control needs to ensure that any type of network outage does not cut the team off from the data.
Controls need to be configured to ensure that only authorized personnel can change data, that changes are recorded and validated, and that the impact of changes on ongoing design projects can be automatically identified and affected parties notified.
A formal release management function should manage the creation of production data sets and bills of materials and their transfer to the purchasing and manufacturing processes. In addition, this capability should include an authorization process to prevent the release of incomplete or unverified data.
generalize
PCB data management is a complex task, if done correctly, it can improve the design accuracy and shorten the time. However, if not implemented properly, any problem can cause the design process to stop or cause the product to not work properly.