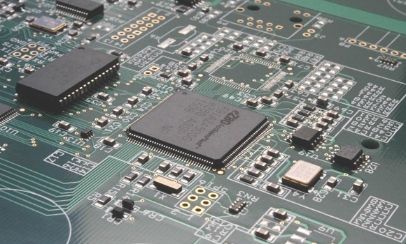
The root of the growth and shrinkage is determined by the characteristics of the material. To solve the problem of the growth and shrinkage of the flexible board, Polyimide, the material of flexible board, must be introduced first:
(1) Polyimide has excellent heat dissipation performance and can withstand the thermal shock during the high temperature treatment of lead-free welding;
(2) For small devices that require greater emphasis on signal integrity, most equipment manufacturers tend to use flexible circuits;
(3) Polyimide has the characteristics of high glass transfer temperature and high melting point, and it should be processed above 350 ℃ in general;
(4) In terms of organic dissolution, polyimides are insoluble in common organic solvents.
The expansion and shrinkage of flexible plate materials are mainly related to the matrix material PI and glue, that is, there is a great relationship with the imitization of PI. The higher the degree of imitization, the stronger the controllability of the expansion and shrinkage.
According to the normal production law, the flexible plate will produce varying degrees of expansion and contraction during the formation of graphic circuit and the combination of soft and hard. After etching the graphic circuit, the density and direction of the circuit will lead to the stress reorientation of the whole plate surface, and finally lead to the general regularity of expansion and contraction of the board surface. In the process of soft and hard bonding, due to the inconsistent coefficient of PI expansion and contraction between the surface covering film and the substrate material, a certain degree of expansion and contraction will be produced within a certain range.
In essence, the growth and shrinkage of any material is caused by the influence of temperature. In the lengthy production process of PCB board, the growth and shrinkage value of the material will have different degrees of subtle changes after many heat and humidity processes, but in terms of long-term actual production experience, the change is regular.
How to control and improve?
Strictly speaking, the internal stress of each roll of materials is different, and the process control of each batch of production plates will not be exactly the same. Therefore, the grasp of the material shrinkage coefficient is based on a large number of experiments, process control and data statistical analysis is particularly important. Specific to the actual operation, the expansion and contraction of flexible plate is divided into stages:
First of all, from the opening to the baking plate, this stage of growth and contraction is mainly caused by the influence of temperature:
In order to ensure the stability of the growth and contraction caused by the baking board, the consistency of process control should be the first thing. Under the premise of unified materials, the operation of temperature rise and temperature fall of each baking board must be consistent. It is not possible to put the baked PCB circuit board in the air for heat dissipation because of the blind pursuit of efficiency. Only in this way can the swelling and shrinkage caused by the internal stress of the material be eliminated to the maximum extent.
The second stage occurs in the process of graph transfer. The expansion and contraction of this stage is mainly caused by the change of orientation of stress inside the material.
In order to ensure the growth and shrinkage stability of the line transfer process, all baked boards cannot be grinded, and surface pre-treatment shall be carried out directly through the chemical cleaning line. The surface shall be smooth after film pressing, and the standing time of the board before and after exposure shall be sufficient. After the line transfer is completed, the flexible plates will show varying degrees of crimp and contraction due to the change of stress orientation. Therefore, the control of line film compensation is related to the control of the combination of soft and hard precision. At the same time, the determination of the range of the growth and shrinkage value of flexible board is the data basis for the production of its supporting rigid plate.
The third stage of expansion and contraction occurs in the process of hard and soft plate compression, this stage of expansion and contraction is mainly determined by the compression parameters and material characteristics.
At this stage, the factors affecting the expansion and contraction include the temperature rise rate of pressing, the setting of pressure parameters, and the residual copper rate and thickness of the core plate. In general, the smaller the residual copper rate, the larger the shrinkage value; The thinner the core plate, the larger the shrinkage value. However, from big to small, it is a gradual process of change. In addition, due to the different material nature of flexible plate and rigid board, its compensation is an additional factor to be considered.