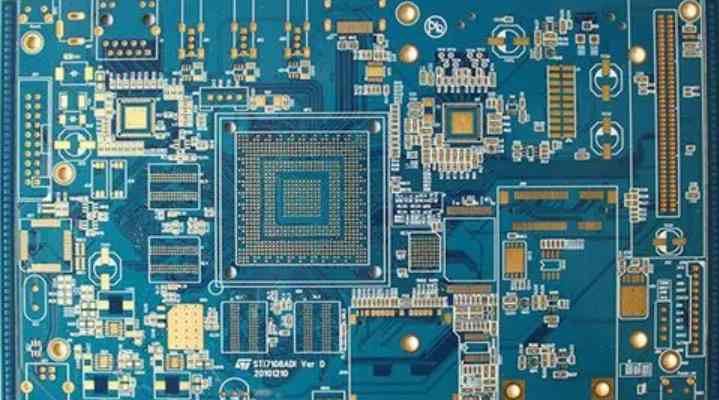
Ceramic PCB substrate plays the role of mechanical support protection and electrical interconnection (insulation) in the process of electronic packaging. With the development of electronic packaging technology towards miniaturization, high density, multi-function and high reliability, the power density of electronic system increases and the heat dissipation problem becomes more and more serious. There are many conditions affecting the heat dissipation of devices, among which the selection of substrate material is also a key link. In order to improve the performance (especially reliability) of these microelectronic devices, the chips must be enclosed in a vacuum or protective gas to achieve air-tight packaging (the chips are placed in a closed chamber and isolated from external oxygen, moisture, dust, etc.). Therefore, it is necessary to first prepare the three wire-board with cavity (enclosing dam) structure to meet the requirements of packaging applications. At present, the common 3D ceramic substrates are: high/low temperature co-fired ceramic substrate (HTCC/LTCC), multi-layer sintered 3D ceramic substrate (MSC), directly bonded 3D ceramic substrate (DAC), multi-layer copper plated 3D ceramic substrate (MPC) and directly formed 3D ceramic substrate (DMC), etc.
At present, there are four types of substrate materials commonly used in electronic packaging: polymer substrate; Metal substrate; Composite substrate; Ceramic substrate. Ceramic substrate material is widely used in electronic packaging substrate because of its high strength, good insulation, excellent thermal and heat conductivity, small thermal expansion coefficient, good chemical stability and so on. Ceramic packaging substrate materials mainly include Al2O3, BeO and AlN. At present, Al2O3 ceramics are the most mature ceramic packaging materials, because of its good heat resistance and electrical insulation, production and PCB processing technology is mature and widely used. Relative to plastic base and metal base, its advantages are:
(1) Low dielectric constant, high frequency performance.
(2) Good insulation and high reliability.
(3) High strength and good thermal stability.
(4) Low thermal expansion coefficient and high thermal conductivity.
(5) Good air tightness and stable chemical properties.
(6) Good moisture resistance, not easy to produce micro-cracking phenomenon.
The disadvantages of ceramic packaging materials are: high cost, suitable for the packaging of advanced microelectronic devices, such as aerospace and military engineering of high reliability, high frequency, high temperature resistance, strong air tightness packaging.
It is also widely used in mobile communication, household appliances, automobiles and other fields. Some countries have developed multi-layer ceramic substrate, making it a kind of widely used high-tech ceramics, from the structure and production process, ceramic substrate can be divided into high temperature co-fired multi-layer ceramic substrate, low temperature co-fired ceramic substrate, thick film ceramic substrate, direct bonding copper ceramic substrate and so on.
The preparation process of high temperature co-fired multilayer ceramic substrate is: Firstly, ceramic powder (Si3N4, Al2O3, AlN) is added into the organic binder and mixed evenly to form paste paste, then the paste is scraped into sheets with a scraper, and then the sheet paste is formed into green blank through drying process, and then the pilot hole is drilled according to the design of each layer, and the metal paste is printed with silk screen for wiring and filling holes. Finally, each green blank layer is superplaced. It is sintered in high temperature furnace (1600℃). Because of the high sintering temperature, the selection of metal conductor materials is limited (mainly tungsten, molybdenum, manganese and other metals with high melting point but poor conductivity), high production cost, thermal conductivity is generally in 20~200W/ (m ℃), depending on the composition and purity of ceramic powder.
In addition, due to the limitation of screen printing process, the circuit precision of HTCC substrate is poor, which is difficult to meet the requirements of high-precision packaging. But HTCC substrate has high mechanical strength and thermal conductivity [20 W/(m·K) ~ 200 W/(m·K)], stable physical and chemical properties, suitable for high power and high temperature environment device packaging. When the HTCC process is applied to the micro steam thruster, the resulting micro heater is more efficient than the silicon based thruster, reducing energy consumption by more than 21%. In order to reduce the temperature of HTCC preparation process and improve the conductivity of line layer, LTCC substrate has been developed. It is similar to the HTCC preparation process, except that LTCC preparation adds a certain amount of glass powder to the ceramic slurry to reduce the sintering temperature, and uses Cu, Ag and Au with good electrical conductivity to prepare metal slurry.
The preparation process of low temperature co-fired ceramic substrate is similar to that of high temperature co-fired multi-layer ceramic substrate. The difference is that low melting point glass material with mass fraction of 30%-50% is mixed into the Al2O3 powder to reduce the sintering temperature to 850~900℃. Therefore, gold and silver with good conductivity can be used as electrode and wiring materials. On the other hand, due to the glass phase in the ceramic material of the low temperature co-fired ceramic substrate, its comprehensive thermal conductivity is only 2~3W/ (m·℃). In addition, because the low temperature co-fired ceramic substrate uses screen printing technology to make metal lines, it is possible to cause alignment errors due to mesh problems. In addition, the shrinkage ratio difference exists in the sintering process of multilayer ceramics, which affects the yield.
Due to the addition of glass powder in the ceramic paste, the thermal conductivity of the substrate is low [generally only 3 W/(m·K) ~ 7 W/(m·K)]. In addition, like HTCC, LTCC substrate uses screen printing technology to make metal lines, which may cause alignment errors due to mesh problems, resulting in low precision of metal line layer. Moreover, the shrinkage ratio difference exists in the process of embryo formation and superpressing sintering of multilayer ceramics, which affects the yield and restricts the development of LTCC substrate technology to a certain extent. After surface treatment, the warpage of LTCC substrate is reduced from 150μm ~ 250μm to 80μm ~ 110μm. By improving the form of LTCC substrate packaging and removing the insulating layer between the chip and the metal substrate, the simulation and experimental results show that the thermal resistance is reduced to 7.3 W/(m·K), which meets the requirements of high-power LED packaging.
It should be noted that in actual production, in order to improve the thermal conductivity of low-temperature co-fired ceramic substrate, heat conduction holes or conductive holes can be added to the patch area, but the disadvantage is that the cost will increase. At the same time, in order to expand the application field of ceramic substrate, the multi-layer laminated co-firing process is generally used to prepare the multi-layer structure containing cavity (usually called ceramic shell rather than ceramic substrate), to meet the requirements of electronic device airtight packaging, widely used in aerospace and other areas with harsh environment and high reliability requirements such as optical communication.
MSC substrates are prepared by multiple sintering in some factories, unlike HTCC/LTCC substrates which are prepared by one molding. The process firstly prepared the thick film printed ceramic substrate (TPC), then printed the ceramic paste on the flat TPC substrate through multiple screen printing to form the cavity structure, and then sintered at high temperature to obtain the MSC substrate sample. Since the sintering temperature of ceramic paste is generally around 800°C, the wiring layer of the lower TPC substrate is required to withstand such high temperatures to prevent defects such as delamination or oxidation during the sintering process.
The circuit layer of TPC substrate is prepared by sintering of metal slurry at high temperature (generally 850°C ~ 900°C), which has good high temperature resistance and is suitable for the subsequent preparation of ceramic cavity by sintering method. The production equipment and process of MSC substrate technology is simple, the plane substrate and the cavity structure are sintered independently, and because the cavity structure and the plane substrate are inorganic ceramic materials, the thermal expansion coefficient matches, there will be no delamination, warping and other phenomena in the preparation process.
Its disadvantage is that both the lower TPC substrate line layer and the upper cavity structure are wired with screen printing, and the graphic accuracy is low. At the same time, due to the limitation of screen printing technology, the thickness (depth) of the prepared MSC substrate cavity is limited. Therefore, MSC three wikis board is only suitable for small volume, precision requirements are not high electronic device packaging. Many microelectronic devices (such as accelerometers, gyroscopes, deep ultraviolet leds, etc.) chips are very sensitive to air, moisture, dust, etc. For example, LED chips can theoretically work for more than 100,000 hours, but water vapor erosion can greatly shorten their life (even down to a few thousand hours).