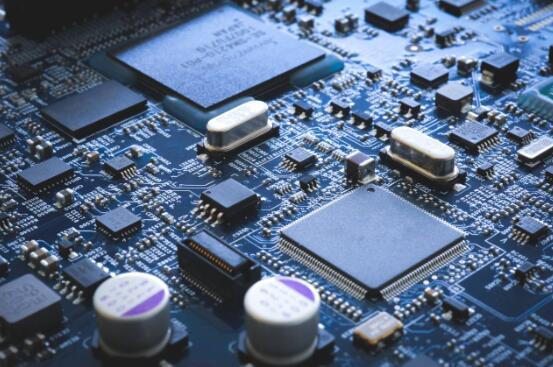
PCB circuit board is connected to the printed wire between each layer, in each layer need to connect the junction of the wire drill a common hole, that is, through the hole, in the production process of PCB processing, the through hole must be plugged. Through the hole plug oil is to guide through the hole with ink inside the plug hole production, the emphasis is the quality and density of the plug hole. Through the hole plug oil process is one of the hole treatment methods, the first is to opaque, above must have ink cover, plugging; The second is the hole can not appear yellow phenomenon, and do not touch tin.
Through hole plug oil processing technology is a key fill through hole cover oil, usually high quality double layer printed circuit boards are made of through hole plug oil, especially for the welding pad like BGA, the regulation is more stringent. Through the hole plug oil first plugs the printing ink outside the full hole plug of the pad and plugs the hole, so that the printing ink on the welding ring is not easy to inject through the hole, and thus does not appear the actual effect of the hole yellowing. The smaller the hole, the easier it is to plug. The hole of fortress oil is not too large. The maximum is 0.5mm.
The pores mentioned above are usually used for interlaminar conduction. Therefore, in order to avoid short circuit when the board is used, usually do cover oil, not only to ensure the electrical performance, but also to avoid the risk of short circuit with other components in the process of use. Therefore, if some printed circuit board needs to pass the hole as a test point or heat dissipation, it will do the window. In addition, for friends with strict technological requirements, those who have done the hole cover oil can change to hole plug oil later if the cover oil is not full enough or yellowish. When docking the plug oil process with the PCB manufacturer, it is important to pay attention to the attributes of the hole when ordering must be consistent with the attributes of the document, so as to reduce the time of mutual confirmation with the PCB manufacturer. If Windows are required, the corresponding solder resistance layer must be clearly drawn. If the board has a large number of pads that need to be welded later, it is recommended that the hole cover oil, so as to reduce the probability of short circuit.
Before the electroplating plug hole and resin plug hole process was popular, PCB manufacturers generally adopted the green oil plug hole process with relatively simple flow, but the green oil plug hole will shrink after curing, easy to appear the problem of air blowing in the air, which could not meet the user's requirements of high fullness. Electroplating and resin plugging processes plug the buried holes of the inner HDI before pressing, which perfectly solves the disadvantages brought by green oil plugging holes and balances the contradiction between the thickness control of the pressed medium layer and the cementing design of the inner HDI buried holes. Although electroplating plug hole and resin plug hole process are relatively complicated and cost is high, they have more advantages than green oil plug hole in terms of plumpness and plug hole quality.
The difference between electroplated plug hole and resin plug hole in PCB processing. PCB board plug holes are usually used after the solderproof layer, followed by a second layer of ink (green paint) to fill the heat sink hole (Termal Pad) with a diameter of 0.55mm or less. The purpose of plugging holes in PCB processing is to avoid short circuit caused by tin infiltration when passing through tin furnace, especially in BGA design, when DIP parts are attached. Maintain surface smoothness; Meet customer characteristic impedance requirements; Avoid line signal damage, etc. Resin plug hole is the use of Solvent free ink plug hole, in addition to make up for the general ink is not easy to fill the problem, but also reduce the ink heat caused by "cracks", usually used when the aperture is relatively large. Electroplating hole filling currently uses the characteristics of additives to control the growth rate of each part of the copper to carry out hole filling action, which is mainly used in continuous multi-layer hole production (blind hole process) or high current design.
1. The surface is different
The electroplating plug hole is filled with copper plating, and the inner hole surface is full of metal, while the resin plug hole is filled with epoxy resin after copper plating on the hole wall, and copper plating on the resin surface. The effect is that the hole can be conductive and there is no dent on the surface, which does not affect the welding.
2. Different processing technology
Electroplating plug hole is to directly fill through the hole through electroplating, no gap, good for welding, but high requirements on the process capacity, general PCB manufacturers can not do. Resin plug hole is the hole wall after copper plating, filled with epoxy resin to fill through the hole, and finally copper plating on the surface, the effect is like no hole, good for welding.
3. Prices vary
The oxidation resistance of electroplating is good, but the process requirements are high and the price is expensive. The good insulation of resin is cheap.