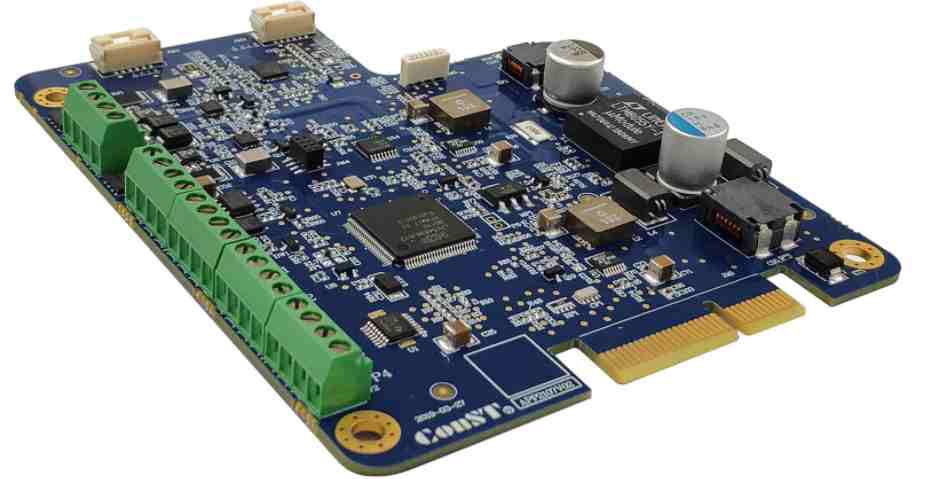
During the welding and assembly process of PCBA, some uncontrollable factors will affect the residual tin beads on the board after the welding of PCBA. If the residual tin beads are too large or the particles of tin beads are too large, it is necessary to clean the residual tin balls of PCBA. There are two ways to clean the residual tin balls of PCBA, namely manual cleaning and machine cleaning. The following patch processing manufacturer to explain how to clean pcba residual tin ball and how to manage the relevant knowledge of the assembly line.
1. How to manage the assembly line
How to manage the smt line management is the planning, organization and control of the daily production activities of the circuit board plant. It is the general term of the management work related to the production of products. It is an important part of the management of the circuit board plant.
1. Production management process organization
(1) The production process consists of production technology preparation process, basic production process, auxiliary production process and production service process.
(2) Organization of production process During the organization of production process, it is required that the production process should be continuous, parallel (parallel operation of each stage and each process), coordinated and rhythmical (balance) to ensure economy. The purpose of the organization of the production process is to arrange the production reasonably and scientifically, so as not to waste manpower and material resources (equipment), improve labor productivity, shorten the production cycle, reduce costs, reduce capital occupation, and complete the plan on schedule, with quality and quantity guaranteed.
2. Workshop production plan is an important tool to organize balanced production, complete production tasks and guide workshop production activities. Its work contents include:
(1) Develop advanced and reasonable quality standards.
(2) Make production and operation plans within the month of the team and the working place.
(3) Calculate and balance the production capacity of the workshop.
(4) Control of production operation plan, including production scheduling, schedule management, WIP management, job accounting, production operation statistics and analysis.
(5) Put forward the production technology organization measure plan.
3. Workshop production control Workshop production control is the supervision, inspection, adjustment and correction of the implementation of the operation plan in the workshop production process. The main work of workshop production control includes production scheduling, job accounting and job analysis.
(1) Production scheduling Production scheduling is the work of checking, supervising and assisting the production input and production schedule of each link in the production according to the requirements of the workshop operation plan. Doing scheduling well is the key to complete shop plan. Dispatching work should have a sound system, including duty system, reporting system, meeting system, field dispatching system and so on.
(2) Operational accounting includes output and input of products and parts (delivery and input period), completion progress, tasks completed in each link, production workers and equipment utilization, etc.
(3) Job analysis Job analysis is the work after the production control requirements, records, accounting, summary, analysis of the completion of indicators, information feedback, so that the basis for production activities and scheduling.
4. Application of Group technology Group technology, also known as group technology (GT for short), is a method of reasonably organizing production technology preparation and product production process based on the principle of similarity. Group technology is to classify and code all parts in the workshop according to geometric shape (shaft, disc, box, gear, etc.), size, processing method (turning, milling, planing, grinding, pliers, etc.), precision requirements (ordinary, precision, high precision), blank type (rod, plate, tube, castings, forgings, etc.) and other classification systems, so as to prepare for production and organize production. The production organization forms of group technology are:
(1) Group process center organizes some parts with similar structure for unified processing on a certain equipment.
(2) Group production unit organizes a group or several groups of parts with similar processes for uniform process route allocation and equipment layout.
(3) Group assembly line Group assembly line is the sequential processing of group production units with the characteristics of line production, and the processing time of each process is equal to the rhythm of the line, which is used for batch production.
2. How to clean pcba residual tin balls
1, manual cleaning
Manual cleaning tools include anti-static brush, washing water, anti-static gloves, etc. By coating the special washing water and then using the brush to clean the tin beads, you can clean the tin beads, but it is not suitable for some high-end products.
2. Machine cleaning
PCBA tin beads can also be cleaned by machine, such as ultrasonic cleaning machine, PCBA water cleaning machine, the use of machine cleaning is more thorough, can effectively ensure the quality of PCBA board. The cleaning of tin beads on PCBA board needs to determine the cleaning method according to the type of components. Some are not suitable for machine cleaning, so manual cleaning can be used.