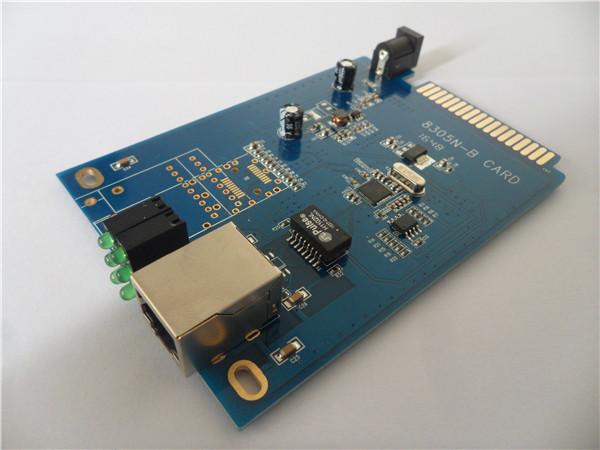
One, soft and hard combined board applICation background
Military, medical facilities, vehicles, communications, laptops, CAMeras and other products.
Two, the combination of soft and hard board unique place
Soft and hard combination board is considered appropriate and the use of rigid (FR4) materials and flexible (PI or PET) materials combination, is a kind of both rigid PCB durability and flexible PCB suitable force of the new printed circuit board. The combination of soft and hard plate has: light weight, thin interlayer, short transmission path, SMAll aperture, less noise, high trust advantages. The combination of soft and hard board can be assembLED in two-dimensional presets and manufacturing lines, three-dimensional interconnection, and can replace the signer, greatly reducing the signer point and assembly cost.
Three, soft and hard combined plate process
Four, soft and hard combined board electronic circuit presets
(1) to prevent the sudden expansion of the line or from large to small, the thickness of the line between the appropriate and the use of tear shape repayment.
(2) The welding pad in accordance with the electrical requirements of the situation, should take the maximum, the welding pad and conductor cosigned office considers appropriate and use the sophisticated transition line, prevent 90 degrees Angle, independent pad should be added toe, in order to enhance the support effect.
(3) As many solid copper foils as possible are preset in the area of soft plate copper waste, which improves the dimensional stability to a certain extent.
(4) The wire in the rigid and flexible transition zone should be smooth and transition, and the direction of the line should be straight with the direction of buckling.
(5) The wire in the rigid and flexible transition zone should be evenly distributed in the whole buckling area.
(6) The wire width of rigid and flexible transition zone should be maximized in the whole buckling area without affecting the electrical performance.
(7) Rigid and flexible transition zone tries its best to prevent PTH presets.
(8) The flexible board bending area shall not be preset through the hole
(9) The bending area should be as large as possible without affecting the assembly situation.
Five, the combination of soft and hard board process is not easy to solve
(1) The size stability of FPC soft board is worse than that of PCB hard board, and the variation coefficient is large, which is easy to lead to the difficult production process after lamination deviation.
(2) During the lamination of the soft plate, it is easy to generate buckling and wrinkle problems, which affect the appearance of the soft plate.
(3) During the second drilling, because there are more adhesive layers, drilling dirt is easy to sprout in the hole, affecting the metallization of the hole.
(4) Because of the drilling stain left in the hole after the second drilling, the common wet method is difficult to remove the stain, affecting the metallization of the hole.
(5) PCB hard screen printing ink is easy to produce ink infiltration into soft board, oil, plate edge exposure copper and other problems, affecting the appearance and performance.
(6) shape molding is considered appropriate and the use of milling process, soft plate area is easy to generate rough edge, not delicate, uneven length problem.
(7) If it is appropriate to use PCB hard board without opening flexible window process in advance, full-plate PCB production is considered appropriate, but it is difficult to use common process to manufacture appearance, and special process will cost higher.
Six Preset specifications for soft and hard combined plate engineering
PCB manufacturability:
1. Material selection is particularly tight for the production of soft and hard binding board FPC, and there is no special requirement to satisfy the customer's internal performance. The reason why the substrate without bonding layer is selected is that the adhesive between the dielectric layer and copper foil is mostly acrylic acid, polyester, modified epoxy gas natural resin and other materials, which has poor flexibility of the modified epoxy gas natural resin adhesive. Polyester adhesives have good flexibility, but poor heat resistance, while acrylic adhesives are good in heat resistance, dielectric properties and flexibility, but it is necessary to consider their glass conversion temperature (Tg) and pressing temperature is high (about 185℃), and the deformation coefficient of non-adhesive substrate is less than that of adhesive substrate. Therefore, it is considered appropriate to use non-adhesive substrate to make soft and hard combined board effect is better.
2. After the inner layer is made, it is necessary to measure the expansion and shrinkage coefficient of the soft plate first before making the window of the hard plate and the inner line, so as to avoid the deviation problem of the inner layer caused by the different expansion and shrinkage coefficient.
3. In the presets, we should consider the presets of matching spots and target punching spots, so as to ensure the very accuracy when punching the matching holes or nail holes, so as not to cause the deviation of the interlayer graphics and waste when stacking plates.
4. In order to solve the problem of drilling burr and peeling, it is best to use aluminum foil plate or epoxy rubber board for drilling pad, and it is not suitable to use cardboard. Secondly, the speed of drilling bit is a particularly tight process parameter. When the feed is too slow, the temperature rises rapidly and the number of drilling dirt, while the feed is too fast, it is easy to lead to broken bit, bonding piece and media layer tear and nail head phenomenon, so it is necessary to adjust and select reasonable and appropriate process parameter in manufacturing.
5 Common sense potassium permanganate, PI debugging, sulfuric acid solution for soft and hard combined plate to drill dirt is difficult to effect, affect the metallization hole. When making, it can be considered appropriate to use plasma cleaning to remove the drilling dirt. Plasma cleaning can quickly and evenly dispose the drilling dirt from the hole wall, and form a certain dent. It can successfully realize three-dimensional co-sign and increase the reliability of metallized holes.
6. Soft and hard combined with hard plate adopts pre-opening flexible window process manufacturing, silkscreen sensitive ink can be made by film screening process, flexible area to shield screen printing ink, avoid ink infiltration into the flexible area to affect the appearance (solder resistance exposure film soft plate area can also adopt shielding manufacturing, but must ensure that the ink can not expose copper)
7. Appearance production generally has the following processes:
(1) Hard-plate pre-opened flexible window is considered appropriate and the use of edge milling process: Due to the flexible local easy distortion resulting in the length of the shape of the milling is not uniform and not delicate, manufacturing can be in the flexible window pad up and down with the rigid outer thickness of the same gasket, and in the milling shape of the press, you can ensure that the milling smooth and average shape edge, of course, the number of planer rotation is particularly tight, too slow, too fast may lead to burr problems, Therefore, it is necessary to adjust and select reasonable and appropriate process parameters during manufacturing.
(2) The die punching process is used when the flexible window of hard plate is pre-opened as appropriate: the production model can be made by presetting the jump punching process, and the first punching soft plate area is in the punching hard plate. This scheme is suitable for mass production.
(3) The hard board does not open the flexible window in advance to control the deep gong board: the deep gong board is long to the precision of the machine tool and the flatness of the board, and the thickness of the base material is required to be correct, the gong board is too deep, it is easy to damage the soft plate, too shallow, the hard plate gong constantly. This kind of shape production has a certain production risk, be sure to use according to the structure of the graphics preset that is appropriate, common products do not propose to use that is appropriate.
(4) The hard board does not open the flexible window in advance to take the laser shape: this method of making the same control deep gong plate is slightly the same, but the laser shape has a certain limit on the thickness, FR4 thickness is higher than 0.4mm laser is difficult, and the cost is high.