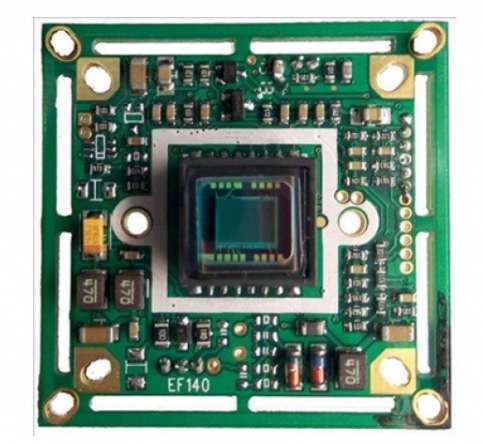
1. Requirements of production line personnel of SMT plant: Operators of all equipment in production line must pass professional technical training and be proficient in operating procedures of equipment. Operators should strictly follow the "safe technical operating procedures" and process requirements.
1. Power supply: power supply voltage and power should meet the requirements of equipment.
2, the voltage to be stable, the requirements: single-phase AC220(220±10%, 50/60 HZ); Three-phase AC380V(220±10%, 50/60 HZ) if not meet the requirements, need to configure a regulated power supply, the power of the power supply should be more than one times the power consumption. Temperature: Ambient temperature: 23±3℃ is the best. Generally 17 ~ 28℃. Limit temperature: 15 ~ 35℃(23±3℃ is the best ambient temperature in the printing room) Humidity: Relative humidity: 45.
3. Working environment: The working room is clean and hygienic, without dust and corrosive gas.
4. The air cleanliness is 100000 (BGJ73-84).
5, in the air conditioning environment, there should be a certain amount of fresh air, as far as possible to control the CO2 content below 1000PPM, CO content control below 10PPM, to ensure human health.
6, anti-static: production equipment is necessary to ground outstanding, should choose the three-phase five-wire grounding method and independent grounding. Production place of the ground, workbench cushion, seat, etc., should meet the requirements of anti-static.
7. Exhaust air: re-flow welding and wave soldering equipment have exhaust requirements.
8, lighting: the plant should have outstanding lighting conditions, the ambition of illumination is 800LUX×1200LUX, at least not less than 300LUX. SMT patch factory
2. Why is there tin bead residue in SMT patch processing?
For SMT processing plant, the appearance of tin beads in the processing process must be solved. An excellent SMT processing plant should try its best to eliminate all processing defects.
First of all, we need to know the cause of the problem. The SMT patch factory will analyze the cause of the appearance of tin beads.
solder beading is a solder beading. It is used to distinguish a solder ball which is unique to the flake element. Tin beads have occurred when the paste has collapsed (slump) or when the slump is depressed during processing. During reflux, the solder paste is isolated from the main deposit and accumulates with excess solder paste from other pads, either bubbling up from the side of the component body to form large beads, or remaining under the component. Tin bead elimination operation as far as possible not through the direct removal of tin beads, in the production process to pay attention to, you can avoid.
A, steel mesh
1, the opening of the steel mesh directly in accordance with the size of the pad opening will also lead to the phenomenon of tin beads in the process of patch processing.
2. If the thickness of the steel mesh is too thick, it may also cause the collapse of the solder paste, which will also produce tin beads.
3. If the pressure of the SMT machine is too high when pasting, the solder paste is easy to be squeezed to the solder resistance layer below the element, and the solder paste melts and runs around the element to form tin beads during reflow welding.
Two, tin paste
1. Other precautions If the solder paste has not been returned to temperature treatment, spatter phenomenon will occur in the preheating stage to produce tin beads.
2. The size of the metal powder in the solder paste, the smaller the particle size of the metal powder, the larger the overall surface area of the solder paste, which leads to the higher oxidation degree of the finer powder, and thus the phenomenon of solder beads is aggravated.
3. The higher the oxidation degree of metal powder in the solder paste, the greater the binding resistance of metal powder during welding. It is not easy to infiltrate between the solder paste and the pad and SMT patch components, resulting in the reduction of weldability.
4. The amount of flux and the amount of active flux is too much, which will lead to the local collapse of the solder paste and produce tin beads. When the activity of flux is not enough, the oxidation part can not be completely removed, which will also lead to the tin beads in the processing of the patch processing plant.
5, metal content in the actual processing of the solder paste used in the general metal content and mass ratio is 88%~92%, the volume ratio is about 50%, increasing the metal content can make the arrangement of metal powder become more closely, so as to combine more easily when melting.
3.SMT patch processing cost calculation?
SMT patch processing is widely used in the electronic manufacturing industry. How should the cost be accounted
At present, the main products of SMT are: lead - free welding process, lead welding process and red glue welding process. And its point accounting method is also very similar, but many users on the patch point accounting and how to calculate the cost of little.
Some companies account for one pad as one point, but have two welds as one point. All you have to do is calculate the number of pads on the printed circuit board, but when you encounter some special components, such as inductors, large capacitors, integrated circuits, you need to calculate the power rating. Detailed experience is as follows: If inductors can be calculated by 10 points, integrated circuits can be discounted by the number of pins (such as 40-pin integrated circuits, 40 divided by 4 equals 10 points). According to the above method, the total number of solder joints of the whole pcb can be calculated conveniently.
Unit price of solder joint: The current unit price of solder joint is 0.01-0.03 yuan/solder joint, depending on the following conditions:
1, unit price according to the process
a. The processing price of the patch with lead solder paste is low;
b. The processing cost of patch lead-free solder paste is high;
c. The processing cost of patch red glue environmental friendly welding paste is low
d. The processing cost of red adhesive patch welding paste plus high cost, the process is more troublesome.
2, according to the order quantity
a. Ordinary SMT chip proofing processing 3-20 pieces, the engineering cost is not calculated by the number of points multiplied by the unit price;
b. If SMT patches are processed in small batches and less than 1000 pieces are produced, the start-up cost shall be multiplied by the unit price;
c. Batch patch processing, calculated by the number of points multiplied by the unit price.
3, according to the difficulty of the plate
a. According to single-side and double-side classification, single-side patch processing speed is faster, double-side patch processing needs two turns, high cost;
b. According to the precision, more fine patch processing, such as bga and other high density integrated circuit board solder paste is expensive, high cost;
c. According to the density of SMT components, the more points in the pcb of the same scale, the higher the efficiency, the shorter the coordinate travel of the SMT machine, the faster the processing speed of the SMT machine.
4. Starting fee
If the single batch processing fee is less than 1000 yuan, it is a small batch processing order. For small-batch SMT patch processing orders, after counting, you will see the type of board and card components, the debugging time of the chip machine, and a starting fee of 400-2000 yuan will be charged for the different difficulties of manufacturing the first piece.
5. Proofing fee
SMT patch processing order A SMT patch proofing order is within 100 pieces, the difficulty of the board, the time to do the program, the time to start the machine, the project cost from 800 yuan to 3000 yuan.
6, wire mesh fee
According to the size of the printed circuit board, open different types of wire mesh. According to the precision of pcba chip, we choose open electrolytic polishing wire mesh or ordinary wire mesh. The cost of different types of steel mesh is about 120-350. Of course, customers can also provide their own wire mesh. SMT patch machining inside