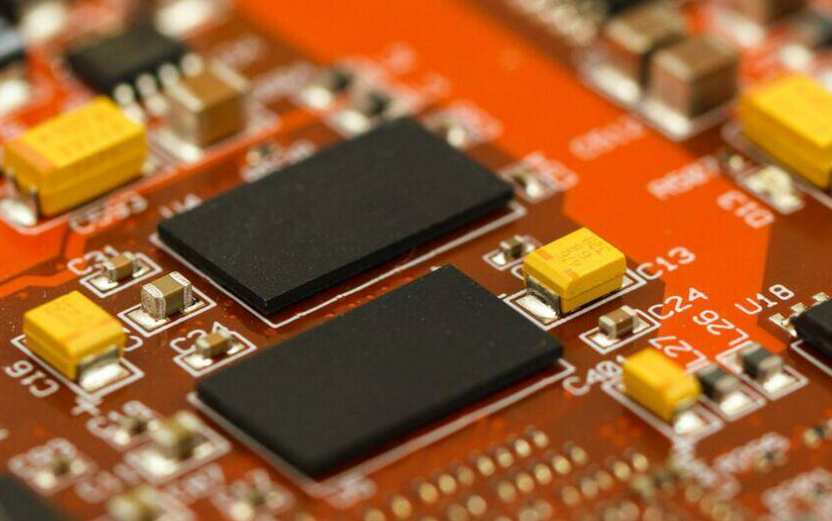
Production efficiency is one of the fundamentals for the survival of PCBA processing plants. Production efficiency, together with quality, cost, delivery time, safety and morale, is called the six tasks of production management. Therefore, the improvement of production efficiency is one of the topics that the managers of each PCBA processing plant need to study.
First of all, before thinking about ways to improve production efficiency, we need to know what factors affect production inefficiency.
Common factors affecting circuit board production efficiency:
1. The sales department does not place orders in time
2. The order only has the delivery date, and the processing start date is not set
3. There are too many emergency or temporary orders, and the production plan changes frequently
4, production workshop machine, mold failure, maintenance time is long
5. The quality of the production process is unstable, with frequent rework or repair
6. The production department did not carry out a complete capacity analysis
7. The procurement of materials is often delayed and the quality of procurement is often poor
8. Material purchase plan and production plan cannot be coordinated and synchronized
9. No outsourced processing schedule
10. Frequent technical changes of products
According to the above factors, the plan is summarized as follows:
No.1
Sound production and operation system should have the basic skills
To maintain a steady footing and ensure efficiency
The root is not solid, why pull branches germinate, blossom and bear fruit; Good trees come from healthy roots. Is to understand the foundation of production operations management ---- basic management.
Use 5S techniques, combined with production and operation process optimization, so as to find solutions.
The key is to make processes and processes transparent, visible, standardized and stable so that they are easy to manage.
No.2
Know oneself and enemy, clear goal, improve efficiency
Asking others is better than asking yourself and helping yourself.
The so-called waste of PCB production site is to reduce the various elements of production efficiency.
Through the action plan, the field diagnosis, the use of seven wastes to establish the real cause of production operation management efficiency loss.
Seven wastes are mainly: 1, the waste of waiting, 2, the waste of handling, 3, bad waste, 4, the waste of action, 5, the waste of processing itself, 6, the waste of inventory, 7, production of too much waste.
No.3
How to use site quick improvement techniques
Source and flow management to improve efficiency
Efficiency is life, time is money. In the fierce market competition, enterprises want to remain invincible, the key lies in the "fast" and "new", the speed is fast, powerful is new. Identify methods and processes to improve productivity and track problems quickly.
Quick improvement on site:
1, IE quickly improve the four ideas: eliminate, cancel, rearrange or replace, simplify
2. Source and flow management by the Fifth Method. Eg.
No.4
Make the plan well-documented
Reduce planned losses and improve efficiency
The process of planning is actually the process of emancipating the mind, seeking truth from facts, is the process of reform and innovation; Only by fully demonstrating the possible situation can we prevent it from happening.
Plan is the key to connecting the team, plan is the line of commitment to the goal, plan is the communication tool, plan is the guarantee of success.
Through production and marketing meetings: to ensure the close cooperation between production and sales, so that the product quality, production capacity and so on continue to improve, with the most reasonable production efficiency, to obtain the maximum benefit.
No.5
Use reasonable purchasing mechanism to ensure both parties
Co-existence and co-prosperity consciousness to enhance production efficiency
Modern win-win model: to assist suppliers, help suppliers reduce costs, improve quality, accelerate product development progress; Build trust, improve efficiency, and build long-term partnership with suppliers.
First, for different suppliers to do a good job of assessment and classification of grades, the premise is to establish a useful evaluation mechanism, according to the ratio of procurement.
Second, incentive measures
No.6
How does material and production schedule control show speed and freshness
Avoid waiting for waste to increase efficiency
After receiving orders from the Department of health management, all staff should be mobilized to complete the arranged plan. Do not change the plan, the relevant departments take the initiative and actively cooperate with each other, take the initiative to respond to the work progress with other units, and jointly complete all the printed circuit board production plan.
Production control operation:
I. Management personnel take the initiative to follow up materials and check regularly
2. Reasonable use of materials for warehousing management; 3. Quick line change
No.7
How to use performance indicator improvement method
To evaluate the health of enterprises and improve production efficiency
Adopt lean method, shorten delivery time, reduce waste, make quality, output and efficiency to a new level.
Constantly analyze the reasons why productivity targets are not being met.
Measuring index:
1. DTD (Accounting of shipment time from raw materials to factory to products)
2, the first qualified rate 3, equipment comprehensive efficiency 4, production schedule up to the standard rate
No.8
How can leadership be implemented through departmental management performance
Improve production efficiency and effectively achieve business efficiency
As an enterprise management cadre should realize that he is the master of the enterprise. Pay close attention to the development of the business and be willing to protect it.
Through the performance of department management, implement the leadership policy, effectively achieve business results: daily important items management is to make the department/workshop full play of strength, produce good performance; If there is an anomaly, it can also be effectively found and dealt with, indeed do a good job of maintenance management.
No.9
Use reasonable production and operation performance
To boost morale and improve efficiency
The biggest goal of enterprise management is to make money and benefit from management. In today's society, only by constantly adapting to development and change, in line with interests, not in line with interests, maintain competitiveness; Otherwise, management and market disconnection, no matter how good the system will not get the ideal economic benefits.
Incentive system rationalization:
1. Performance bonus
2. Performance indicators
No.10
Take advantage of the rapidly changing laws of production operations
Let enterprises improve production efficiency
Plan not as fast as change? On the other hand, it is impossible to cope with change without a plan. In fact, this means how to adapt to rapid changes in the environment.
Timely response to changes in the situation, rapid modification of the plan, rapid and accurate communication, PCB production plan preparation and modification flexibility is the most important condition.
By shortening construction time and compressing work-in-process retention.
Difficulty is the ladder of success, the success of the process is reasonable, reasonable, reasonable.