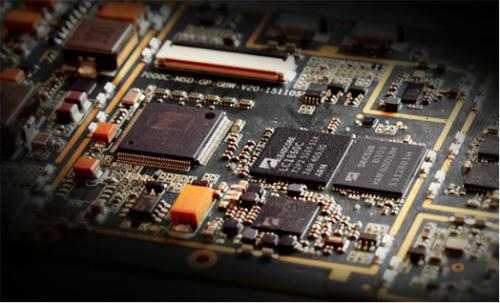
1. Manual welding shall follow the standards of "small before large", "low before high", type and batch welding, first welding chip resistor, chip capacitor, crystal triode, then welding small chip components, large chip components, and finally welding the plug-in.
When welding chip components, the width of the selected soldering iron head should be consistent with the width of the components. If it is too small, it is not easy to locate when welding.
When welding SOP, QFP, PLCC and other components with feet on both sides or four sides, several anchor points should be welded on both sides or four sides first. After carefully checking each foot position is consistent with the corresponding pad, drag welding can be carried out for the remaining foot positions. Drag welding speed can not be too fast,1s up and down drag a tin point.
After welding, you can use 4~6 times of high magnifying glass to check whether there is a bridge between the tin points. The local bridge place can be dipped in a little flux with a brush and drag welding again. The continuous welding of the same position should not be more than 2 times.
When welding chip components, a layer of welding paste is evenly coated on the pad, which can not only play the role of infiltration and welding aid to the tin spot, but also greatly facilitate the maintenance work and improve the maintenance speed.
The two most important processes for successful maintenance are pre-heating and post-welding cooling. smt patch processing
.2 How to judge the quality of the pcb Board
With the rapid development of mobile phone, electronics, communication and other industries, PCB circuit board industry also continues to grow rapidly, people on the number of layers, weight, precision, material, color and layer requirements are increasingly high. Reliability.
Due to the fierce market price competition, the cost of PCB board materials is also rising. More and more manufacturers monopolize the market at low prices to improve their core competitiveness. However, the reason behind these ultra-low prices is the reduced cost of materials and process manufacturing. Equipment is often prone to cracks (cracking), scratches (or scrapes), and its combined factors (such as accuracy and performance) are not up to standard, which seriously affects product solderability and reliability.
Global Wei printed circuit board
So, how to judge the quality of the board, there are two methods
appear
1. Standard rules for size and thickness
The thickness of the circuit board is different from that of the standard circuit board. Customers can measure and check according to thickness and specifications.
2. Light color
The outer circuit board is covered with ink and the circuit board can be used as an insulating layer. If the color of the board is not bright, and less ink is used, the insulation board is not good.
3. Welding appearance
Because there are many parts on the circuit board, if the welding is bad and the parts are easy to fall off, the welding quality of the circuit board will be seriously affected. It's important to have a good look, to identify it carefully, and to have a strong interface.
A high quality PCB board must meet the following requirements
1. The line width, line width and line distance of the line meet the requirements to avoid line heating, open circuit and short circuit
2. High temperature copper is not easy to fall off
3. Copper surface is not easy to oxidize
4. No additional electromagnetic radiation
5. The shape should not be deformed, the hole position of the circuit board and the deformation error between the circuit and the design should be within the allowable range
6. High temperature, high humidity and special environmental tolerance should be considered
3. What is PCBA OEM? How to choose a good PCBA OEM?
PCBA OEM processing mode is more and more attention, the development trend of high-speed electronics industry, then the global Wei Xiaobian to give you the following brief content:
1. What is PCBA OEM?
In the narrow sense, PCBA OEM refers to the service of PCB board, electronic components purchasing and PCBA processing.
In a broad sense, PCBA OEM refers to providing a complete set of PCBA processing services from electronic scheme design, electronic product development to material purchasing, prototype proofing and testing, and post-batch processing and production.
2. What are the types of PCBA OEM?
2.1. Technology-oriented
Mainly focuses on electronic solution development (or forward, or reverse), electronic product design. The company focuses on the research and development of electronic products, but also can provide small and medium-sized batch PCBA processing and corresponding materials purchasing.
2.2. Processing oriented
The company has several SMT SMT processing lines, to provide efficient processing services for electronic products. But in product development to provide less resources, generally need customers to provide relevant technical documents for processing.
3. What should we consider when choosing PCBA OEM?
How to choose PCBA OEM manufacturers needs to be combined with their own needs. If they have related PCB files, they only need to follow the PCBA processing and production. Usually, they choose processing-oriented PCBA OEM factories with great advantages in experience and price, especially for some mass consumption, security and other electronic products processing. If their own products need to be developed from zero, such as some professional industrial control electronic motherboard, instrument control system, automotive equipment control board, choose technology-oriented PCBA OEM factory is relatively better.
kingford is a professional supplier of electronic products OEM, PCBA custom processing, PCBA OEM, , SMT patch processingDIP plug-in processing, mass production of electronic products, PCBA maintenance testing and other services.