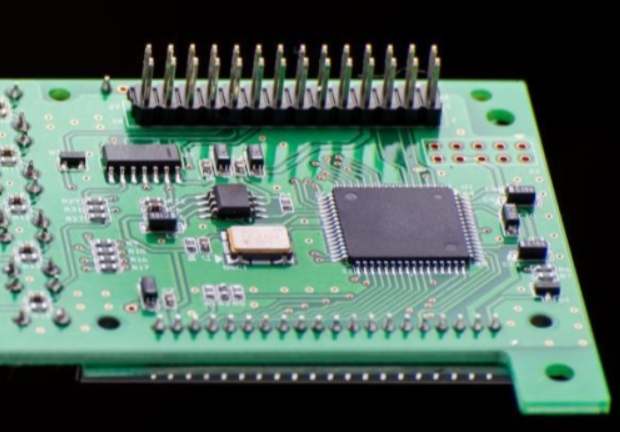
In the SMT process, there are six quality problems that need to be paid attention to
1, mount design quality,
2. Quality of mounting raw materials (components, PCB, welding paste and other mounting materials);
3, mounting process quality (process quality),
4. Quality of mounting welding points (result quality),
5, mounting equipment quality (condition quality),
6. Mounting test and mounting management quality (quality control).
There are three types of PCBA failures
1. The device is faulty
2. Operation failure
3. Mounting failure
◆ Component Fault (Device Fault)
Faults caused by quality problems of components, such as the performance indicators of components beyond the error range, necrosis or failure, misplacement caused by mislabeled models, and broken pins
◆ Operation Fault
Refers to the product does not work properly, but is not caused by device failure and mounting failure. It is usually caused by the circuit schematic and PCB design problems, such as Timing Fault, A/D or D/A error accumulation fault, PCB circuit error fault.
◆ Assembly Fault
Failure due to problems in the mounting process, such as solder bridge short circuit, welding open circuit, mispaste or missing paste devices, etc.
◆ poor Soldering
Solder spot only a small amount of tin welding, resulting in poor contact, circuit break.
In production practice, device faults and operation faults are less than 8%, and mount faults are more than 85%. Mount fault is the main source of SMT product failure.
The most common faults in mounting faults are welding joint bridging (also known as bridge or welding bridge), virtual welding, welding bead formation, vertical piece, missing piece and other faults.
◆ The influence of dispensing
If the amount of coating is too much, the bond strength will increase, but if the bond strength is too large, it is likely to cause micro-cracking of SMC/SMD matrix.
If overcoated, the adhesive will spill out after SMC/SMD mounting, which will cause a fault between the welding joint or welding area and wiring;
If the amount of coating is too little, it is difficult to observe from the appearance, but it will reduce the welding strength.
In addition, the control of coating amount, the guarantee of coating position precision, the reasonable ratio of adhesive composition and other factors will affect the bonding quality of SMC/SMD electrode and substrate welding area.
◆ Tin paste coating (paste) commonly used paste method
① Solder paste printing method: The solder paste is coated on the pad by printing method through the opening hole of the silk mesh plate or template.
② Solder paste injection method: The solder paste is placed inside the syringe and pressurized by pneumatic, hydraulic or electric drive, so that the discharge point of the solder paste through the pinhole is on the surface of the SMB solder pad.
◆ The influence of welding paste coating process (paste)
① Welding paste material quality. Solder paste is composed of solder paste powder and solvent two parts.
② Printing thickness of solder paste. The printing thickness of the solder paste should be uniform
③ Precision of welding paste printing position. The precision of the solder paste printing position shall be within the specified tolerance.
(4) Quality of printing screen.
⑤ the influence of welding paste printing process.
◆ The main influencing factors of reflow welding on SMC/SMD are
Thermal shock during welding. Reliable heating process must be set during operation to reduce thermal shock stress.
◆ If the welding process setting and the control quality of each prior process cannot meet the specified requirements, it will lead to the "Manhattan" phenomenon (also known as "warping" or "standing tablet"), position deviation and lateral swing phenomenon of SMC/SMD.
◆ The main reason that PCB cleaning affects the quality of SMC/SMD mounting is
It is very important to set cleaning conditions and cleaning time reasonably for the erosion of cleaning solvents.
◆ Cleaning process is more commonly used
Ultrasonic cleaning, dip cleaning, steam cleaning or a combination of two different methods.
◆ The main content of mounting quality detection and control
Basic contents: raw material incoming inspection and control, mounting process inspection and control, and component inspection after mounting
◆ Inspection of incoming raw materials:
Including components, PCB, solder paste, solder flux and all SMT mounting process materials testing.
◆ Process detection and control:
Including dispensing, welding paste printing, patch, welding, cleaning and other processes of process quality inspection and control.
◆ Component detection:
Component appearance test, solder spot test, component performance test and function test.
◆ SMT chip processing plant quality detection methods have a variety of, currently used detection methods mainly have the following four types:
Manual visual inspection; Electrical testing; Automatic optical detection; X-ray detection.
◆ QC manual visual inspection
Manual visual inspection is to use human eyes or with the help of a simple optical amplification system to inspect the printing quality of solder paste and solder joint quality, which is a less investment and effective method. It is still widely used in SMT mounting process.
Manual visual inspection can be used to check the content including: printed circuit board quality, glue quality, solder paste printing quality, patch quality, solder joint quality and circuit board surface quality.
Manual visual inspection has great limitations: such as poor repeatability, can not accurately and quantitatively reflect the problem, labor intensity is large, is not suitable for mass centralized inspection, can not check the invisible solder joint, the metal layer inside the pin welding end of the failure of the solder joint can not be checked, the surface of the components can not check the tiny cracks.
Electrical test: contact detection of circuit components.
Electrical fault: polarity paste wrong, solder bridge, welding, short circuit and other defects, so after the installation and cleaning of the circuit components must be carried out contact detection, test the electrical characteristics and functions of components. Online testing (ICT) is the main contact testing technology.
Online test: On the SMA with components installed, the components on the SMA are tested individually and one-by-one by means of electrical isolation through the jig needle bed or flying needle.
◆ AOI automatic optical detection
Using optical means (CCD camera + auxiliary light) to acquire the image of the measured object, and then in a certain way to test, analyze and judge. The commonly used inspection, analysis and judgment methods include design rule inspection (DRC) method and pattern recognition method.
The test function of AOI technology in SMT: PCB light plate test, welding paste printing quality test, component test, post-welding component test.
◆ X-ray, X-ray detection
The coverage of process defects is as high as 97%. Defects that can be checked include virtual welding, bridge connection, stele, insufficient solder, porosity, device leakage, etc. Especially for BGA, CSP and other solder joint hidden devices can also be checked.
High test coverage. It can be checked where the naked eye and online tests cannot. For example, if PCBA is judged to be faulty, suspected to be PCB inner wiring fracture, virtual welding, air hole and poor molding, etc., X-ray can be quickly inspected.
◆ Testing items and methods of electronic components, PCB and other raw materials
Among them, the most critical is the weldability test of components and PCB, which is also the most commonly used test items. The test methods include edge impregnation method, welding ball method, wetting weighing method, wetting balance test, rotary impregnation test, wave solder impregnation test, etc.
◆ IPC Standard (Institute of Printed Circuits)
IPC's main service objects: printed board, electronic mounting parts industry, users and their suppliers
IPC standards are authoritative, systematic, advanced and practical
SMT mounting quality measurement and control technology development trend
Automation development trend, intelligent development trend, real-time development trend, forward development trend, diversity development trend, integration development trend.
◆ Introduction of kingford SMT patch processing plant
At present, global Wei Technology Co., Ltd. has fully upgraded 4 automatic SMT SMT processing production lines, equipped with SPI automatic 3D solder paste detector, new imported high-speed SMT machine, 20 temperature area large reflow welding equipment, ultra high pixel AIO optical detector, X-ray detector, BGA repair table, It can be affixed with high precision components such as 0201/0.25mm spacing BGA/ dual-row QFN.