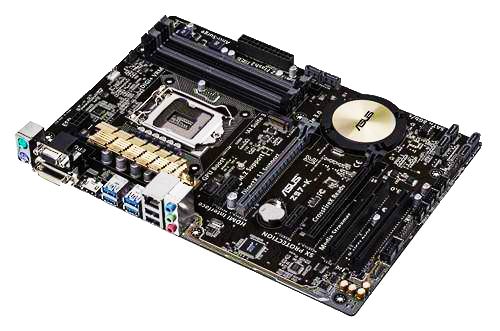
1. First of all, carefully consider the environment in which the PCB board may be used. Over-protection of the product can allow it to survive the harshest environmental conditions, but the "harshest environment" may be temporary or transient, so a resin solution with lower performance in the higher temperature range is usually sufficient. Take extreme temperatures; Your application may sometimes experience temperature spikes of up to 180°C, so you think you need a special resin. However, these conditions usually only last for a short time, whereas under "normal" operating conditions the circuit board is usually only exposed to temperatures up to 120°C, which means that there are many more resin types and application types to choose from.
The chemical resistance required for the resin you choose also depends on the duration and/or intensity of the chemical contamination. In terms of the damage caused, it made a big difference whether there was a thin layer of the polluting chemical on the surface of the resin and it was wiped off within five minutes, or whether 500 milliliters of the chemical were applied to the synthetic resin for an hour or more. In addition, the number of different chemicals to which boards can be exposed is usually very limited. Often an area that is too large is listed during the design phase, just to be "safe".
2. Environmental factors that usually affect the circuit board include temperature, chemical corrosion, physical shock (vibration) and thermal shock. Here you must determine which aspect is likely to have the greatest impact on your circuit board, and you must choose the appropriate synthetic resin accordingly. The three main resin types (epoxy, polyurethane, and silicone) each have advantages and disadvantages. Silicone resins have the widest continuous operating temperature range of any resin composition, making them preferred for low and high temperature applications as well as thermal shock applications. In addition, they maintain their flexibility in the corresponding temperature range and show little degradation over time. However, their disadvantage is that they have little adhesion to some substrates, and their chemical resistance is much worse than epoxy resins.
Epoxy resins, on the other hand, not only have excellent chemical resistance, but also have good performance at a variety of temperatures. However, due to their rigid nature, they also do not protect against impact. On the other hand, polyurethane resin has good moisture resistance and impact resistance, but poor temperature performance. Therefore, polyurethane is best used only when operating temperatures range from -40 to +120°C. However, they have similar flexibility and even better adhesion to many substrates than silicone resins, and are inexpensive.
3. If the printed circuit board is installed in an enclosure, the enclosure material must also be considered when pouring resin into it for complete potting. Plastic shell is usually injection molded; If the resin is not removed, the residue of the release agent may remain on the surface, thus affecting the good adhesion of the resin. Some plastics are very sensitive to moisture and will undergo size changes and other physical changes under wet conditions that may place physical stresses on enclosures, resins, circuit boards and components. For cases made of steel, aluminum or other metals, the difference in coefficient of thermal expansion between the case and the synthetic resin and the surface treatment used must be considered.
4, generally speaking, the thicker the resin layer, the higher the level of protection. However, if all the components on the board are of different heights, the thickness of the resin layer and the degree of protection of each component will vary. Good circuit board design and carefully selected components can best solve this problem. However, given the level of protection provided across the PCB board, the thinnest synthetic resin layer available must be assumed. In order to reduce weight and/or volume, engineers tend to reduce the amount of resin used. Therefore, while thicker coatings generally provide better long-term protection, the expected service life must also be considered.
5. Remember: Before considering packaging or packaging, you must thoroughly clean the PCB board. Surface contamination can have a negative impact on the degree of protection provided by the package, especially on chemical resistance (as this makes it easier for chemicals to penetrate). In addition, due to the weak adhesion of the resin to the PCB circuit board, impurities can affect the resin's ability to absorb shock and thermal shock, ultimately leading to stripping. Of course, after cleaning, all solvent or cleaning solution residues must be removed and the board must be thoroughly dried before the resin can be applied.