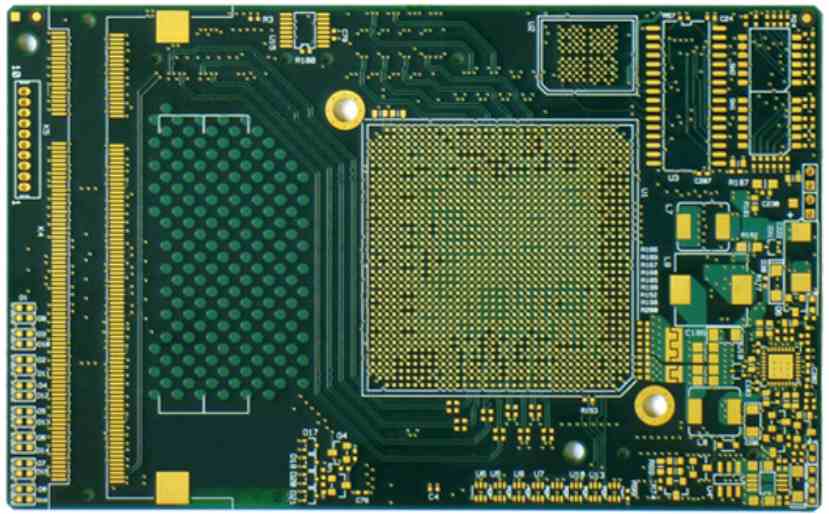
The automotive electronics market is the third largest application area of PCBA after computers and communications. With the automobile from the traditional sense of mechanical products, gradually evolve, develop into intelligent, information, mechanical and electrical integration of high-tech products, electronic technology has been widely applied in the automobile, whether engine system, or chassis system, safety system, information system, interior environment system, etc., are without exception, the use of electronic products. The automobile market has obviously become another bright spot in the consumer electronics market. The development of automobile electronics naturally drives the development of PCB for automobile.
In today's key application objects of PCB, PCB for automobile is occupying an important position. However, due to the special working environment, safety and high current requirements of vehicles, they have high requirements for PCB reliability and environmental adaptability, and involve a wide range of PCB technology types, which is a challenge for PCB enterprises. For the manufacturers who want to develop the automotive PCB market, they need to do more understanding and analysis of the new market.
With special emphasis on high reliability and low DPPM for automotive PCBS, does our company have the accumulation of technology and experience in high reliability manufacturing? Is it consistent with the direction of future product development? In the process control, can be well in accordance with the requirements of TS16949? Has low DPPM been achieved? These need to be carefully evaluated, just see this attractive cake and blindly enter, will be harmful to the enterprise itself.
The following provides a representative part of the professional production of automotive PCB enterprises in the testing process of some special practices to provide the majority of PCB colleagues for reference:
1. Second test method
Some PCB manufacturers adopt the "second test method" to improve the rate of finding the defect plate through the first high voltage breakdown.
2, bad board anti-stay test system
More and more PCB manufacturers have installed "good board marking system" and "bad board error prevention box" in the light plate testing machine to effectively avoid artificial leakage. The good plate marking system marks the tested PASS plate for the test machine, which can effectively prevent the tested plate or bad plate from flowing to the customer. In the test process, when the PASS board is tested, the test system outputs the signal that the box is open; Conversely, when a bad board is tested, the case closes, allowing the operator to properly place the tested circuit board.
3. Establish PPm quality system
At present, PPm(Partspermillion defect rate) quality system has been widely used in PCB manufacturers. In many of my company's customers, to Singapore's HitachiChemICal its application and results are the most worthy of reference. There are more than 20 people in the factory who are responsible for the statistical analysis of the abnormal quality of online PCB and the abnormal return of PCB quality. Statistical analysis method of SPC production process was used to classify each broken plate and each returned defective plate for statistical analysis. Besides, auxiliary tools such as microslicing were used to analyze in which production process bad and defective plates were produced. According to the results of statistical data, purposefully solve the problems in the process.
4. Comparative testing method
Some customers use two different brands of PCB models in different batches for comparative testing, and track the PPm of corresponding batches, so as to understand the performance of the two test machines, so as to choose a better performance test machine to test automotive PCB.
5. Improve test parameters
Select higher test parameters to strictly detect such PCBS. Because, if you select higher voltage and threshold, increase the number of high voltage leakage reading, you can improve the detection rate of PCB defect board. For example, a large Taiwan-funded PCB enterprise in Suzhou uses 300V, 30M and 20 euros to test automotive PCB.
6. Check the parameters of the test machine regularly
After long-term operation of the test machine, the internal resistance and other related test parameters will be deviated. Therefore, the machine parameters should be adjusted regularly to ensure the accuracy of test parameters. Test equipment in a considerable part of large PCB enterprises are half a year or a year to complete machine maintenance, adjust the internal performance parameters. The pursuit of "zero defect" automotive PCB has been the direction of the efforts of the majority of PCB people, but the limitation of the process equipment, raw materials and other aspects, so far printed circuit board world's top 100 enterprises are still exploring ways to reduce PPm.