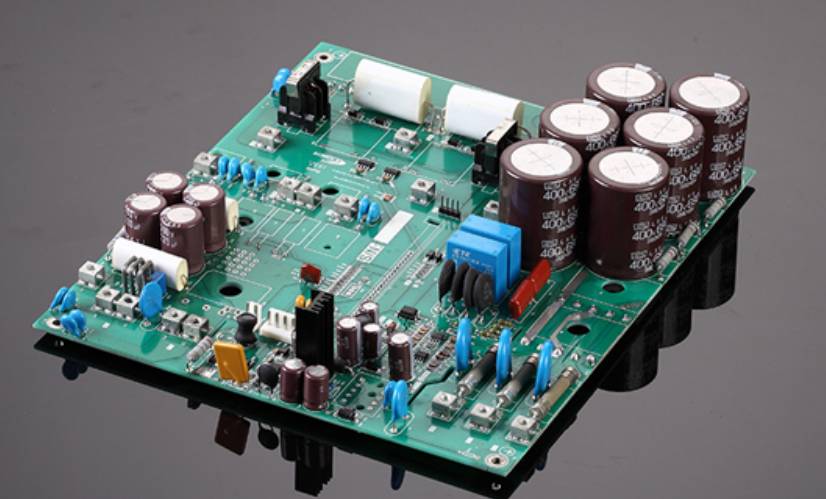
1. Background description
There are two important concepts, "Producibility Levels" and "Component Mounting Complexity Levels" in IPC-SM-782, which are different but all have three corresponding levels. Both concepts are used to describe the complexity of PCBA assembly, and the three levels are divided according to the technologies employed in the assembly -- through-hole insertion, surface assembly, and hybrid installation.
These two concepts are not quite compatible with reality. On the one hand, plug-in components are used less and less; On the other hand, the difficulty and complexity brought by the same plane assembly of ordinary pitch and fine pitch packaging has far exceeded the difficulty and complexity brought by the mixed application of interpolation technology and surface assembly technology. In other words, the complexity of electronics manufacturing today comes from two main challenges: one is the component package size is getting smaller; The second is the mixed use of ordinary spacing and fine spacing packaging on the same mounting surface of PCB. This is also the biggest challenge facing PCB manufacturability design today. The core task of PCB manufacturability design is to solve the mixing problem of common spacing and fine spacing packaging on the same mounting surface by means of package selection, component layout and other design means.
2. Mixed loading degree
Mixing degree, which is an important concept put forward in this book, refers to the degree of difference between various packaging and assembly processes on the PCBA mounting surface. Specifically, it is the degree of difference between various packaging and assembly processes and steel mesh thickness. The greater the degree of difference between assembly process requirements, the greater the degree of mixing, and vice versa. The greater the degree of mixing, the more complicated the process and the higher the cost.
The mixing degree of PCBA reflects the complexity of the assembly process. We usually talk about the PCBA "good welding", actually contains two layers of meaning, the first layer means that there are no components on the PCBA with very narrow process window, such as fine spacing components; Another meaning is the degree of difference between various packaging and assembly processes on the PCBA mounting surface.
The higher the mixing degree of PCBA, the more difficult it is to optimize the assembly process of each type of package, and the worse the process is. Take the PCB circuit board of mobile phone as an example. Although the components used on the mobile phone board are fine spacing or small size components, such as 01005, 0201, 0.4mmCSP, PoP, each package is very difficult to assemble, but their process requirements belong to the same complex level, and the mixing degree of the process is not high. Each package process can be optimized design, the final assembly yield will be very high. While communication PCBA, although the components used are large in size, but the process mixed degree is relatively high, the assembly needs to use stepped steel mesh. Limited by the component layout gap and the difficulty of steel mesh production, it is difficult to meet the individual needs of each package. The final process scheme is often a compromise scheme to take care of various packaging process requirements, rather than the optimal scheme, and the assembly yield will not be very high. This is the significance of the concept of mixing degree.
Packaging with similar installation process requirements on the same assembly surface is the basic requirement of package selection. In the hardware design phase, the establishment of suitable package is the first step of manufacturability design.
3. Measurement and classification of mixed loading degree
The mixing degree of printed circuit board is expressed by the maximum difference of the ideal steel mesh thickness of the components used on the same PCB assembly surface. The greater the difference, the greater the mixing degree and the worse the process.
The greater the thickness difference of steel mesh, the more difficult it is to optimize the process. The process is difficult, not to say that the production of ladder steel mesh is difficult, but the greater the thickness of ladder steel mesh, the more difficult to ensure the printing quality of welding paste. Ideally, the step thickness of steel mesh should not exceed 0.05mm (2mil).
4. The relationship between the pin spacing of components and the maximum thickness of steel mesh
The design of steel mesh thickness is mainly considered from two aspects, that is, pin spacing of components and coplanar package. The pin spacing of components corresponds to the area of the steel mesh window, which basically determines the maximum thickness that can be used, and the coplane of the package determines the minimum thickness that can be used. Because the thickness of steel mesh is not designed according to a single pin spacing of components, the mixing degree cannot be determined simply according to the size of the spacing, but it can be used as a basic reference for the package selection of components.
5. The meaning of the concept of mixing degree
This concept has important guiding significance for PCB component package selection and component layout. We want as little difference as possible in the process of packaging on the same assembly surface.