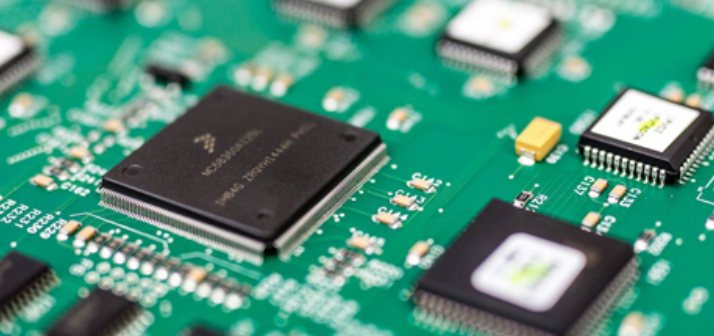
When printing solder paste on the printing board, there is a certain restrictive relationship between the speed of the scraper, the pressure of the scraper, the Angle of the scraper and the mesh plate, the release speed and the viscosity of the solder paste. Therefore, only by correctly controlling these parameters can the printing quality of the solder paste be guaranteed.
1. Printing stroke
Before printing, it is generally necessary to set the pre-printing and post-printing limits, that is, to determine the printing stroke. The front limit is generally 20mm before the template figure, and the back limit is generally 20mm after the template figure. Too large spacing is easy to prolong the overall printing time, and too short is easy to cause defects such as adhesion of welding paste figure. Control the printing stroke of solder paste to prevent solder paste from flowing into the opening at the start and end of the printing position of the template, causing printing defects such as adhesion of the printed graphics there.
2. Angle of the scraper
The included Angle of the scraper affects the vertical force of the scraper on the solder paste. The smaller the included Angle is, the greater the component force Fy in the vertical direction is. The pressure generated can be changed by changing the Angle of the scraper. If the Angle of the scraper is greater than 80°, the solder paste can only keep its original state and move forward without rolling. At this time, the component force Fy in the vertical direction is almost zero, and the solder paste will not be pressed into the printing template window. The best setting of the Angle of the scraper should be within the range of 45°~60°, at which time the solder paste has good rolling property.
3. Speed of the scraper
The speed of the scraper is fast, and the force of the solder paste is large. However, increasing the scraping degree will shorten the pressing time of solder paste. If the speed of the scraper is too fast, the solder paste can not roll and only slide on the printing template. Considering the actual situation of the solder paste pressed into the window, the maximum printing speed should ensure that the vertical and horizontal direction of the QFP solder paste is uniform and full. Usually, when the speed of the scraper is controlled in 20~40mm/s, the printing effect is better. Because it takes time for the solder paste to flow into the window, this is particularly obvious in the printing of fine-spacing QFP graphics, when the scraper along the QFP pad side of the operation, perpendicular to the scraper on the pad of the solder paste graphics is fuller than the other side, so some printing press has the function of the scraper rotation 45°, to ensure that the fine-spacing QFP printing on all sides of the solder paste uniform amount.
4. Scraper pressure
The pressure of the scraper is usually referred to as the printing pressure. The change of the printing pressure has a great impact on the printing quality. Insufficient printing pressure will cause solder paste scraping is not clean and lead to insufficient solder paste on the circuit board; If the printing pressure is too large, it will cause deformation in the front of the scraper and affect the Angle of the scraper which plays an important role in the pressing force. The printing pressure should usually be the same as the pressure generated by rolling, which can be set within the range of 5~100MPa. Too much cave-in and leakage behind the template will occur. In addition, since the force generated by rolling varies with the amount of solder paste supplied, the operator needs to adjust the optimum value appropriately
5. Width of scraper
If the scraper is too wide relative to the PCB, then it needs more pressure, more solder paste to participate in its work, and will cause the waste of solder paste. Generally, the width of the scraper is PCB length (printing direction) plus about 50mm is the best, and to ensure that the scraper head falls on the metal template.
6. Printing gap
Usually maintain the PCB circuit board and template zero distance (early also required to control in 0~0.5mm, but there should be zero distance when FQFP), part of the printing press in the use of flexible metal template also requires the PCB plane slightly higher than the plane of the template, adjusted template metal template slightly up, but the height of the support should not be too large, otherwise it will cause damage to the template. From the running action of the scraper, the correct printing gap should be that the scraper runs freely on the template, which requires the solder paste to be scraped away wherever the scraper goes, leaving no excess solder paste, and at the same time requires the scraper not to leave scratches on the template.
7. Release speed
After solder paste printing, the instantaneous speed of template leaving PCB board is a parameter related to printing quality, and its adjustment ability is also a parameter reflecting the quality of the printing press, especially important in precision printing. While early presses used constant speed separation, advanced presses have a short pause when the plate leaves the solder paste pattern to ensure optimal print pattern. When demoulding, the substrate drops, and the printing template is deformed and flexed due to the adhesion of the solder paste. The template should return to its original position due to the elastic force of flexure. If the separation speed is improper, the template flexure is too large. The result is that the template is quickly reset due to its elastic force, lifting around the solder paste, forming an extremely raised printing shape at both ends, and the lifting height is proportional to the deflection of the template; In severe cases, the solder paste will be scraped off so that the solder paste remains in the opening. Usually, the demoulding speed is set at 0.3~3mm/s and the demoulding distance is generally 3mm.
8. Cleaning mode and frequency
In the printing process, the bottom of the template should be cleaned to eliminate its attachments to prevent contamination of the printed circuit board. Cleaning usually uses anhydrous ethanol as cleaning agent, cleaning methods are wet wet, dry - dry, wet wet dry and so on. In the printing process, the cleaning frequency of the press should be set for 8~10 pieces per printing, which should be determined according to the opening of the template and the continuous printing of the solder paste. When there are fine spacing and high density graphics, the cleaning frequency should be higher to ensure the printing quality. Generally, it is also stipulated that dust-free paper should be used to scrub once every 30 minutes.