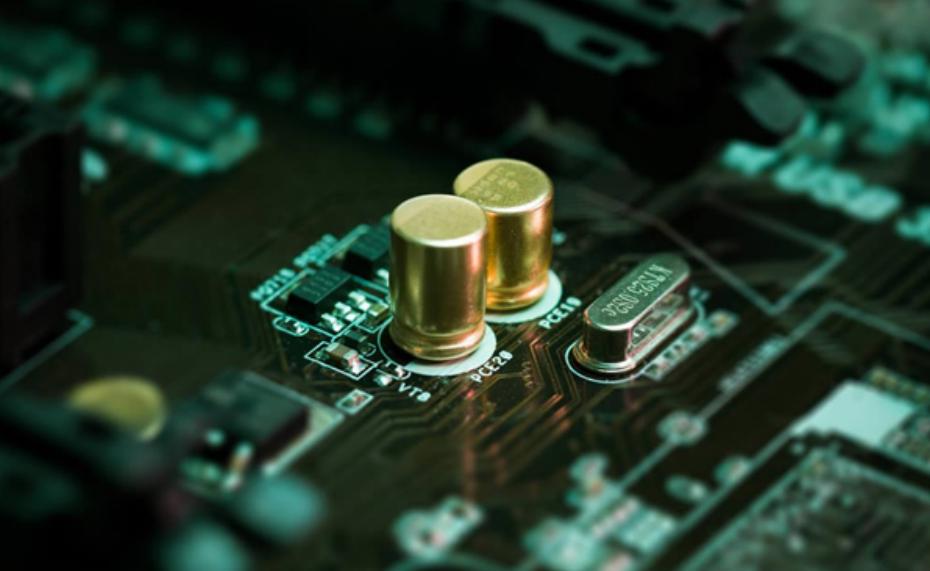
1.PCBA manufacturability design program
The core concept of DFM is that circuit designers and technicians must master and comply with PCBA manufacturability design procedures prior to the layout, wiring and pad design of printed circuit boards. Following PCBA manufacturability design procedure is the first prerequisite for product manufacturability design.
Determine the design process to determine the function of electronic products, performance indicators and the overall goal of the overall size of the machine, electrical principle and mechanical structure design, determine the size and structure of the printed circuit board according to the structure of the machine, select the printed circuit board materials and electronic components according to the function of the product, performance indicators and product grade, determine the process plan, complete the assembly manufacturing process design Finally, PCB circuit design. If you do not follow the above procedures, do not determine the process plan and complete the assembly process design on the printed circuit board circuit design, then the PCBA manufacturability is inevitable.
Determine the process plan and complete the assembly process design must be carried out in the overall program design of the product, that is, in the overall program demonstration of each project and product, the process plan proposed by the chief engineer, and by the circuit design chief engineer, structural design chief engineer and process chief engineer in the program demonstration report to complete this work, as a product program evaluation of an irreplaceable must review project! This is the important work we must do in the project design stage of the product.
In the demonstration of product scheme, the chief process engineer and electrical installation technician participate in the demonstration of all product schemes, and put forward the process scheme and quality assurance outline according to the tactical technical index of the product: introduce the latest achievements of electronic installation technology at home and abroad to the circuit designer, put forward the requirements of electronic installation technology in circuit design and the best electronic installation process scheme to ensure the tactical technical index of the product The leader in charge proposes the test items, implementation ways, equipment and infrastructure to be added, and the characteristics of electronic assembly that should be noted for the product. This is the first prerequisite to implement product manufacturability design.
The process work in the planning stage is the core and priority among priorities of the whole process! At the same time, according to the environmental requirements of the product, installation density safety and reliability requirements, analyze the high-density components and micro components that may be selected, and propose to the supervisor the test project, implementation approach, equipment and infrastructure that need to be added, as well as the characteristics of electronic assembly that should be paid attention to in this production surface.
It is the first prerequisite for the manufacturability design of the product that the electrical assembly technician participates in the demonstration of all the product schemes. At present, many of the quality problems of electronic products, basically from the early planning is not in place! The process work of many enterprises is basically from the back end of the product design and manufacturing chain to participate in, everything is already "wood has become a boat", too late.
2. Timing of assembly process design
DFM can be divided into four stages according to time, which are as follows:
Collaborative Design
Strictly speaking, this is the real sense of manufacturability design. Throughout the whole design process, at the early stage of the design cycle, we start to comprehensively analyze the requirements of design, cost and quality at the same time as the design to find the most reasonable design balance point.
Comprehensive Analysis Comprehensive analysis
According to the requirements of the product's tactical and technical indicators, the product's operating environment and installation density, the possible assembly mode was proposed. The welding process was determined by the assembly mode. On this basis, a set of PCB layout and wiring design requirements and welding pad design requirements suitable for the welding process were sorted out from the mature process specifications according to the characteristics of the product.
Basic Pre-Release Analysis
Mainly check the design content before trial production, from the aspects of DFM, DFA,DFT and design documents to check the rationality of product design; Most of the manufacturability analysis or manufacturability analysis that we currently use in electronics companies, including the use of DFM software and manual analysis, is a pre-trial analysis.
Post-Release Review
The quality analysis of products after trial production mainly refers to the feedback after trial production. Problems found in trial production are summarized and fed back to designers, so as to timely update the design within the feasible scope and improve the manufacturability of products. However, after all, it is better than never. Different stages of implementation have different impacts on product design and production costs. The earlier the stage of DFM involvement, the easier it is to solve the problems found and the less damage it will cause.