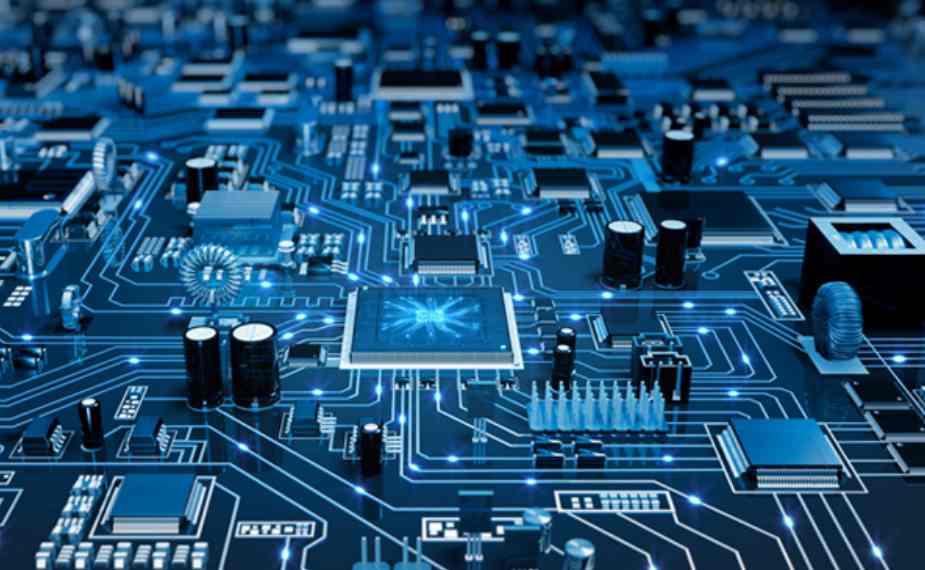
At present, ANSJ-STD-001E, IPC-610E and IPC9 620B are widely used as the quality standards for electronic assembly in domestic and foreign civil electronic products manufacturing industry.
The formation of solder joints for printed circuit board components is directly affected by the pad layout design, so the implementation of ANSI-STD11 00E and IPC-610E is predicated on PCB layout and pad design complying with the constraints of IPC-7351, IPC-2221 and 12 IPC2222.
If the quality standards of GJB and QJ are adopted, the requirements of GJB3243, GJB4057, GJB4907, QJ201B, QJ831B and QJ3103A15 must be followed if the quality standards of QJ165B, QJ3011, QJ3012 and QJ3117A14 are implemented. Without compliance with these design standards, neither IPC-A-610E, ANSI/J-STD00E16, nor GJB and QJ quality standards can be implemented.
The execution of IPC7351, IPC221 and IPC-222 is the prerequisite for the quality evaluation of ANSIJ-STD-001E and IPC-610E. To achieve the quality objectives of ANSI-STD001E, IPC-610E, or GJB and QJ, the following four factors must be in place.
1. Good design quality
Good design quality includes assembly method, package type of components used, component layout design, pad design and density design, solder joint reliability and technology design, PCB circuit board structure, material and process design, etc. "Design should be designed for manufacturing", strengthen the circuit manufacturability, make the circuit design in accordance with the requirements of standardization, standardization design, improve the design quality of circuit design, eliminate the problem as far as possible in the design stage is the fundamental purpose of manufacturability design. Design for Manufacturability (DFM), another general name of DFX technology, is an important part of the key technology of concurrent engineering and runs through the whole process of enterprise development. DFM is designed with manufacturing in mind. Only in the initial stage of the design of the design of manufacturability, usability, detectability and manufacturing economy, quality stability of the full demonstration and attention, it is possible to achieve the dual purpose of "zero defect design" and "zero defect manufacturing", only such enterprises can provide customers and the market with cost-effective quality electronic products. Manufacturability design is a brand new topic, a brand new design concept; People have a process of understanding, understanding and mastering it. Practice has proved that those who master and benefit from it can master and benefit from it early.
2. Qualified material quality
Qualified material quality includes process quality of components, process quality of PCB board, storage and distribution management of components and PCB. Our management and some process personnel like to consider simply from the perspective of improving the process. In fact, many defects are caused by unqualified materials. Strengthening material quality control will get twice the result with half the effort.
3. Process optimization and control
The defects and material quality problems of the congenital design lack of manufacturability are difficult to be compensated by improving the process measures, that is to say, the process is by no means universal! Good design quality and material quality will not naturally lead to reliable welding quality, so it is necessary to optimize welding process parameters as the core, to establish a complete process quality control system as the goal, to carry out process research and development.
4. Production site management
Production site management includes operation standard, anti-static management, environmental management, key process control point management, temperature and humidity management, and 5sS. Its core is to improve the execution! Many electronics research institutes and electronics factories do not have standards and norms, but the implementation is not good, the main reason is that the enterprise management needs to strengthen the cognition of the process.
Organizational assurance measures to achieve high and reliable quality objectives
To achieve the above four goals must be achieved: the establishment of a complete process system, including an independent process research department; To establish relatively perfect electrical equipment process specifications, including specifications for PCB circuit design and manufacturing specifications, to establish the corporate culture of manufacturability design; Have the innovation ability, can carry out advanced manufacturing technology research and establish a complete system of electrical equipment technician as organizational assurance measures.