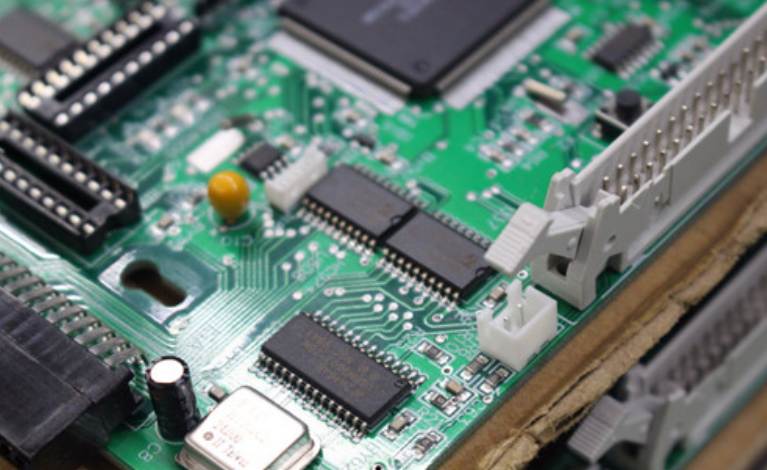
From the technical point of view and the quality point of view, as long as we check the most important links in the entire SMT process, we can roughly see whether an SMT factory is capable of producing boards that meet our requirements.
Relatively important projects in SMT production control:
1. Whether the quality of solder paste printing can maintain consistency?
2. How to test and judge whether the furnace temperature meets the requirements when reflow is used.
3. How to avoid wrong parts.
4, how to avoid hand ornaments.
5. Ability to calculate and modify the thickness and opening size of stencil to meet the actual demand.
6. Is there sufficient equipment or instrument to analyze defective welding products?
Among them, the quality control of solder paste printing is the most important, because if the solder paste is not printed well, the back of the patch is accurate and the furnace temperature of the welding is adjusted well.
In terms of the overall process capability of SMT today, the solder paste printing ability is the worst. Because the solder paste printing more or less or the printing offset are related to the quality of the solder behind, it is the most need to be special control. The accuracy of other SMT machines already exceeds the required level, so there is nothing to say, unless the program of X-Y position is not written well in the beginning, and the temperature curve of the backwelding furnace has already been determined. As long as you understand the damage that the melting temperature of tin and enough heat may bring to the material, there is nothing else that needs to be specially adjusted.
How to evaluate and ensure the consistency of solder paste printing quality?
Solder paste printing on printed circuit boards can basically be divided into two key points:
One, the ability of solder paste quality control
Solder paste brand recommendations or the use of a reputable company will be more insurance. As for the fresh-keeping degree of the solder paste, it is necessary to check the time tracking after the solder paste is removed from the ice, opened the can and stirred. Each company must have internal rules that stipulate how much time the solder paste is exposed to the air to use up, so as to avoid excessive oxidation of the solder paste, resulting in poor eating of tin in the subsequent back welding. In addition, the control of the solder paste applied on the steel plate is the key point, as long as this is well controlled, The rest should be generally fine.
Another project needs to be asked in detail. If SMT of the factory is not in 24-hour shift, from shutdown to opening, how will the first batch of solder paste be treated by ice removal and temperature return? Because it is unlikely to stop the entire SMT line and start the line only when the solder paste returns to the temperature, generally the solder paste returns to the temperature will be more than 4 hours. If so, it means that the production line will not produce for 4 hours. Therefore, will some staff be arranged to come to work 4 hours earlier to return the solder paste to the temperature, or let it return to the temperature the day before? If the return temperature is more than one day in advance, there will be the problem of reducing the activity of solder paste. Generally speaking, if the return temperature of solder paste is more than 12 hours, it will be scrapped.
As for why the paste should be refrigerated at low temperature? This is to keep the paste active; Why do I need to return the temperature before use? It is to make the solder paste consistent with room temperature, so as not to produce water condensation on the solder paste and sputtering at high temperature backwelding.
Two, the ability of solder paste printing
As for the assessment of solder paste printing ability, it is required to take the board with fine spacing (0.4mm or 0.5mm) BGA on the circuit board to do the solder paste printing test, so that the same PCB can pass the repeated solder paste printing for many times (5-10 times is appropriate, if it can be done to 25 times, of course, but it takes too much time). After each printing, the printing result should be observed under a microscope (it is recommended to take a picture of the four corners of the disk), to check whether there is tin phenomenon or whether the printing deviation exceeds the welding pad, welding pad 1/3 tin ball to judge its printing ability.
If there is SPI (Solder Paste Inspector) in the production line, it is recommended to measure the solder paste printing quantity (volume) and then calculate the variance. It is not significant to calculate Cpk, because the tolerance is difficult to define.
In addition, the steel plate wiping and cleaning is also one of the factors that affect the quality of solder paste printing, because the solder paste printing for a long time will have the problem of tinning (solder paste sticks to the back of the steel plate), which is a big killer of tin, so every once in a while (printing several times PCB circuit board) to wipe the steel plate with a dust-free cloth will become the focus, There is also the steel plate printing how many times to use ultrasonic cleaning once can avoid the hole plug problem.